Hi All
I just though I'd show you what I've been working on this week.
I've been trying to clear some space on the bench

and one of the things getting in the way is a bench grinder. I bought it off ebay a couple of months ago because it was more powerful than my existing grinder, it was cheap and it was local (no delivery offered so that's why it was cheap). So far so good.
I tested it and it ran nice and smoothly but then I realised that the wheels were only 16mm thick rather than the more common 20mm. That was quite irritating because 16mm wheels are more expensive, and my grinding rests have a 21mm slot in the table to fit around the wheel. Well part of the plan was always to get some decent wheels so I thought "I'll fit 20mm wheels".
I took the guard off and realised that was easier said than done.

If I fitted a 20mm wheel I wouldn't be able to put the nut on. I left it on the bench while I thought about it and eventually concluded that the solution was to change the washers for thinner ones. The supplied pressed steel washers were 5mm thick and I thought that if I made new washers 3mm thick that would allow a 1mm deep recess for the side in contact with the stone and the central portion would be 2mm thick which would be adequately thick to avoid distortion.
This publication
http://www.hse.gov.uk/pUbns/priced/hsg17.pdf gave me a bit more confidence that this plan wasn't going to result in exploding grinding wheels.
So I made the washers by turning a recess in the face of a drilled bar and parting off the washers. One was a reject as the parting tool deviated making it too thin in the middle. On another the parting tool went the other way so it had to have the other side faced too.
Here they are with a couple of the originals for comparison.
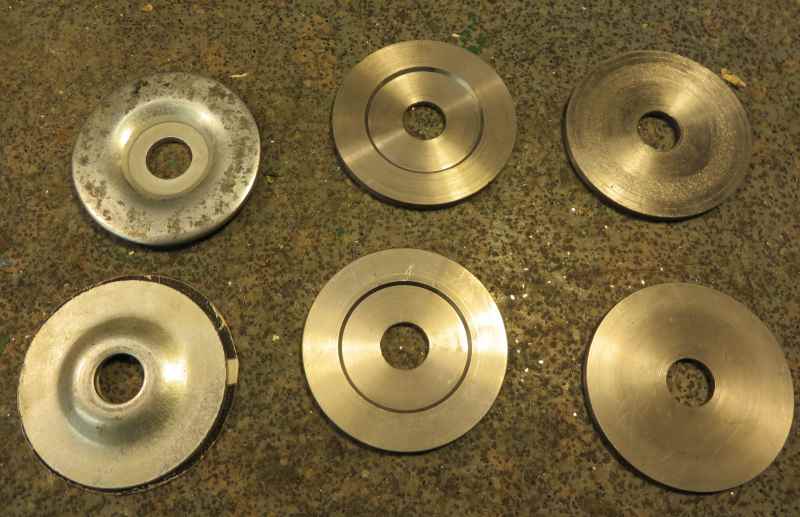
This shows the difference in thickness.

I then tried them in place with the 20mm wheels from the other grinder and discovered that they weren't central in the guards and one wheel fouled the guard. I could have ground a bit off the guard but instead I took the grinder to bits to discover why the wheels were off centre.
On measuring the shaft at one end was 2mm longer than the other which puzzled me. I took the grinder further to bits to see if there was a corresponding assymetry somewhere else. I discovered that behind one of the bearings was a wavy thrust washer.
One bearing housing was tight, and the other was less tight - and I concluded that was so that one bearing could float slightly controlled by the thrust washer to take up changes on expansion etc.
So I reassembled it, putting the thrust washer on the long end of the shaft (which meant the ends of the housing had to be swapped) and it all went together with nothing fouling and no need to gring anything. I tested it using the new washers and 20mm wheels and all was well.
I've ordered new wheels and they'll fit on here.
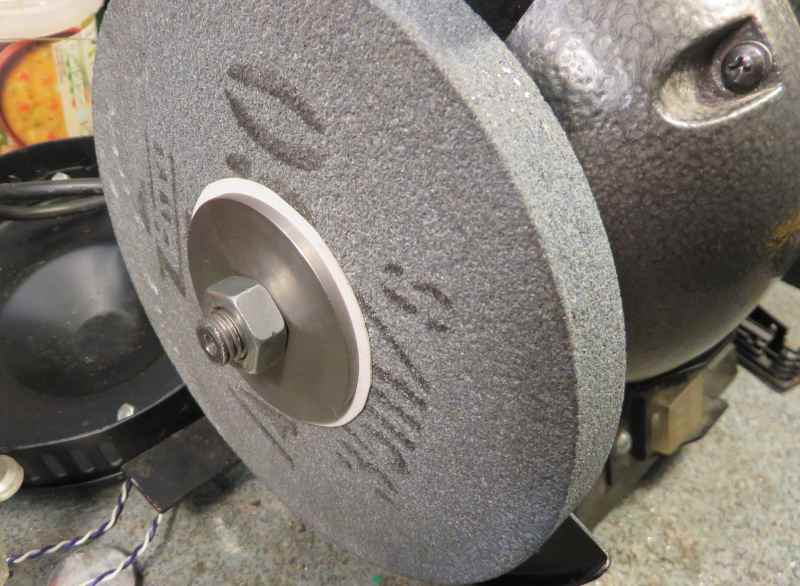
Nothing is that simple though is it?

When I tested it I had some trouble eliminating side to side wobble of the wheel - I thought it would be better with turned rather than pressed washers. I took the grinder to pieces again and put the shaft in the lathe and took a tiny skim off the shoulders where the wheel mounts and I could then get side to side wobble down to an acceptable amount.
Now I'm just waiting for the new wheels to arrive and I'll put the old grinder on ebay.
Russell