The title says it all really; this will be a medium term project to get a 1946 Myford lathe up and running with a good selection of tools and ancillaries. I've given myself until Jan 1 to get the job done; at that point I either take it round the back of the barn and stick a round from a big bore Webley in it's ear or move it out of intensive care and into rehab. Pic below from the Myford publicity dept.
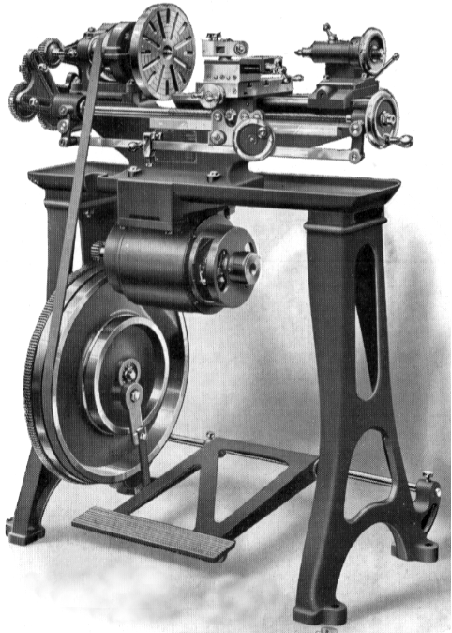
Post retirement I wanted to develop my interests in amateur gunsmithing and automata, so a lathe was an obvious necessity. The choice lay between "Any old British Iron" or a Chinese machine composed of old bean tins, bicycle frames, sand and bad paint. The M type has an interesting history being the standard model makers machine prior to WW II, and then being issued in large numbers to the armed forces. REME workshops, RAF bases and HM ships and submarines all had them; some folk have even traced which ship their ex RN machine came from. I got mine off Ebay for a princely £300 plus a trip from Wales to Sheffield. I'm still unsure if I made the right choice ... neither option is without it's difficulties especially for the beginner, which is definitely me.
The m/c came in good basic condition (plus a coat of rubbishy black paint) the original guards, motor, stand were all present and correct. The bed ways showed rust speckles but you cant get a .0015 feeler gauge under a straight edge at any point nor can you see daylight. What it
didn't have is a much longer list than what it
did. Viz.....four jaw chuck, fixed and moving steadies, face plate, complete change gear set (about one third present), cutting tools or multiple tool holders. As a novice I didn't realise the significance of all this and thought getting the bits and bobs would be simple and relatively cheap.

My first efforts at turning a bit of printer rod were awful; the tool climbed all over the workpiece, the finish was terrible, and lots of noise accompanied proceedings. I found accurately setting the tool height to be impossible using all the usual methods advised on the 'net. Lining the bit up to a centre, the nearest I managed was about .030" off; up or down please yourself. The steel rule trick was another fiasco; hopeless, so I determined the exact centre from the bed with a second hand Microball height gauge (£20 off Ebay worth it's weight in gold) and set the tools with that. I reckon I'm just about spot on now and never get even the trace of a pip on a facing cut. Result.
I soon discovered that I was a chump at hand grinding HSS tools. With great help and advice from Jenny at JB Cutting Tools I have used carbide inserts for virtually all the development work; under the right conditions they work a treat. Under the wrong ones they chip, break and die which for me is a good sign to stop what I'm doing and have a re-think. Even so I still couldn't take a cut over .010" without chatter; if I stayed within that limit I was usually OK and got a very nice finish, anything more bust the tool as chatter kicked in. I then started to work back from the tool bit, to the top slide gibs, to the cross slide gibs, to the carriage gibs, carriage stop, you name it, looking for sloppiness ... nada, nothing improved matters.
It slowly dawned (I know, I know) that if I fed the tool in with the leadscrew handle and kept the pressure tight on, the chatter diminished; ease off and chatter returned. I tightened up the phos. bronze bearings according to the book, but I still couldn't get any forrader and the scrap bin was filling up with inserts. The problem it seemed to me must lie in the headstock bearings and was probably end float. This was quite a leap for mankind because I'd never even heard of end float at that point ..... now I'm an expert! There is a collar on the rear spindle end which is supposed to tighten up an internal thrust bearing; I did that and still got no improvement but there was a clue something was amiss and needed rectifying. If I turned the collar finger tight as hard as I could and ran the lathe the bearing got hot very quickly. Time for invasive surgery..... When I took the spindle and bearings out I saw this ....



At first I was really depressed, they looked pretty gruesome, but I have access to an ultrasonic cleaning unit and after a good blast virtually all the black crap was gone off the spindle. A bit of gentle work with steel wool and the difference in appearance was remarkable without any measurable dimensional change. I'd had a bit of a head scratch in the meantime and formed the theory that the scoring was preventing any axial movement when the thrust collar was tightened up and thus allowing end float, but pressure from the tool overcame this and pushed the spindle against the internal thrust bearing. What was needed was a second, but very thin, thrust bearing on the outboard end of the left hand bearing to pull things together. And here it is ...
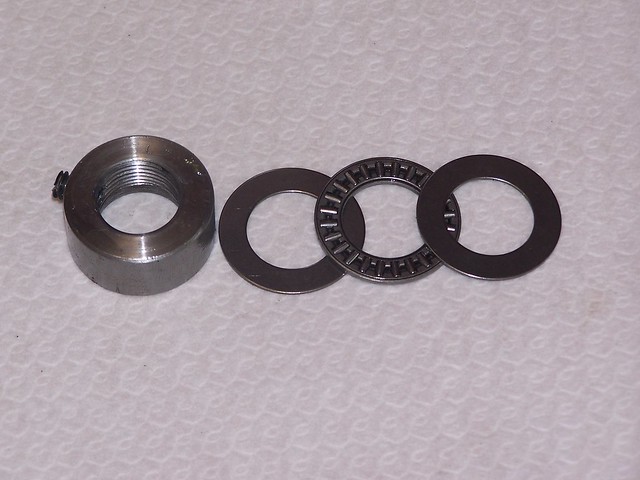
It's an Imperial size, 3/4" ID by 1.25" OD and fits exactly! On reassembly and oiling the whole shooting match slid together as sweet as nut, much nicer than before............... and the cursated chatter has gone, departed, it is no more, finito, ab est

It sits in the recess between the threaded collar and the bronze bearing nut as if it was made for the job, and still there is a bit of wiggle room left.

.060" cuts off diameter (might be more, haven't tried) and an acceptable finish; so now I have a workable machine and it's onwards and upwards. You can't believe how long it's taken to get here, and how frustrating it's been but I feel I'm on the way now. Next stop tool grinding and tool holders with incremental height setting.
Eug