Thanks all! It's one of my favorite tricks since it's cheap & easy and one can brag about being "green" and a loyal recycler.
The lathe project started as a quick (hah, that's a joke!) experimental mod to the Denford CNC MicroMill I got off Craigslist last summer for $100. It's a "training" mill with a tiny little Sherline mill in a VERY robust enclosure. I worked over the mill and hacked the control (thanks to the Brits over on the Denford forum) to get it working via TurboCNC and the parallel port instead of serial FANUC control with a dongle & proprietary software. That's why it was $100; no software, no dongle, etc.
After I got it working, I got this crazy idea to do lathe ops by mounting a treadmill motor (already had that) powered homemade ER32 spindle mounted to the left side of the enclosure floor, run the mill table almost all the way to the right and stick a toolholder on the left end of the table and use its X/Y movements to do small part CNC lathe ops. I added 1.5" X 4" rectangular steel beams (from the scrapped treadmill) under the enclosure to tie the mill into it more rigidly.
I have it crudely working and it looks like it's going to be useful but I have a ways to go yet before I call it done. I have a spindle encoder & wheel mounted and have to get that working. If it all works OK, I plan to get a Homann DigiSpeed XL to let TCNC control the spindle speed via the KBIC-10 cheap eBay speed control...who knows, maybe even threading? If it all works OK, I hope to build a bigger lathe to put all the good stuff on. This one's work envelope is very small.
That's the synopsis but if you want more gory details & pics, I can start a new thread here later and post links to threads on HSM showing how it all came about. There's a lot of stuff and it'd be easier to do that instead of typing it all over again.
Here's a couple more pics; cuts a mean taper, yay!

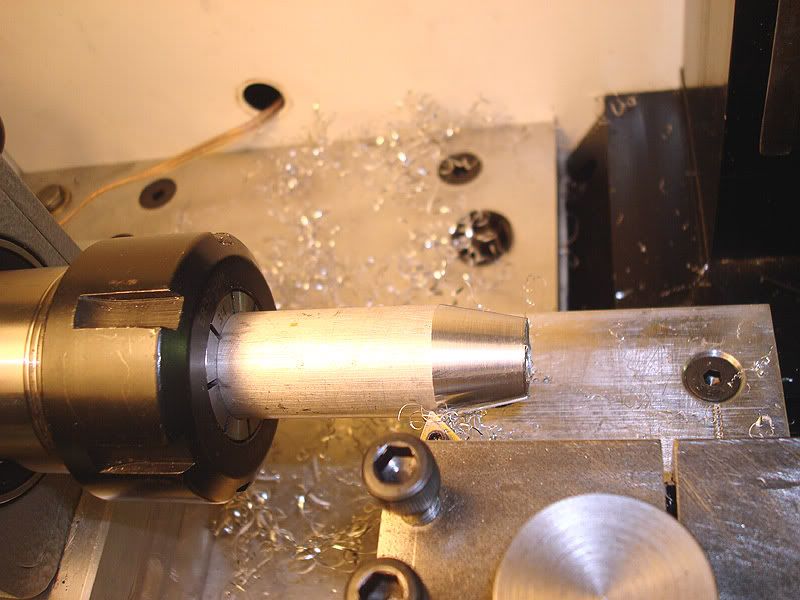