I think I have most of the parts now
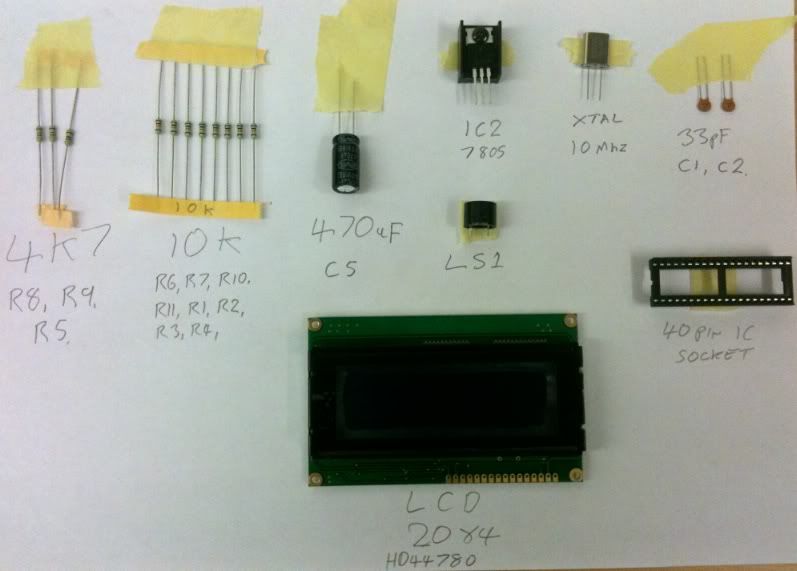
I found a nice heat sink for IC2 off of an old board (I have a box of old boards

) and LC1 I found on another board
The pic and 10k preset are in the post and I still have to order the keyboard,diodes,100nF caps and SIL socket.
I am unsure about the two 33pf caps as they are just marked 33

Anyway some pics of the board
I used toner transfer paper and a laser printer
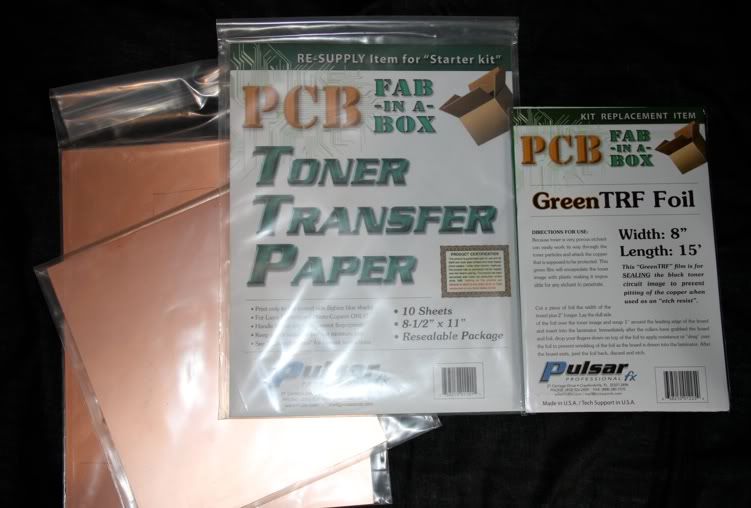
I printed out a test image to make sure it was the correct size

Then used the print to cut out a piece of copper clad pcb
The pcb that comes with the kit is 0.8mm thick which means it cuts great in a paper guillotine
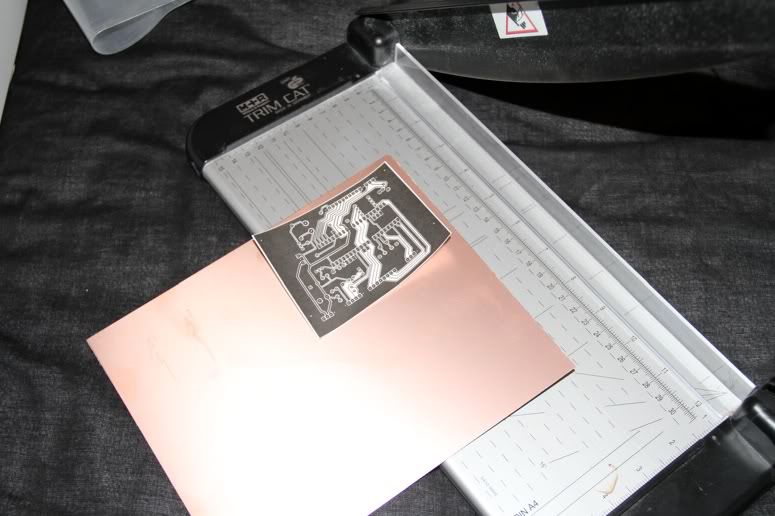
Next I print out another copy and tape a piece of toner transfer paper over the image
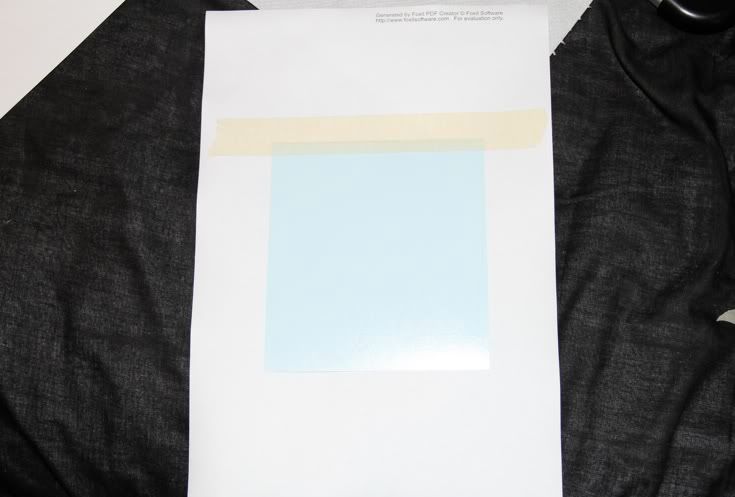
And run it back through the printer again
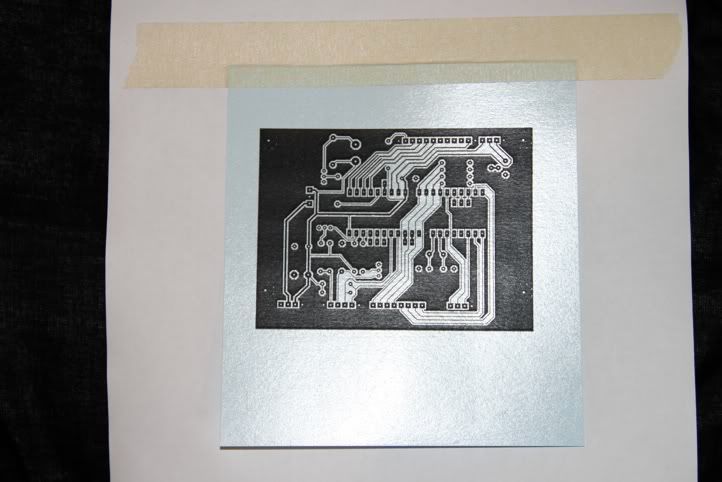
Then I take the toner transfer paper and tape it face down on to my piece of pcb
and run it through this laminator (this is apparently the only laminator that will do this I got mine from ebay)
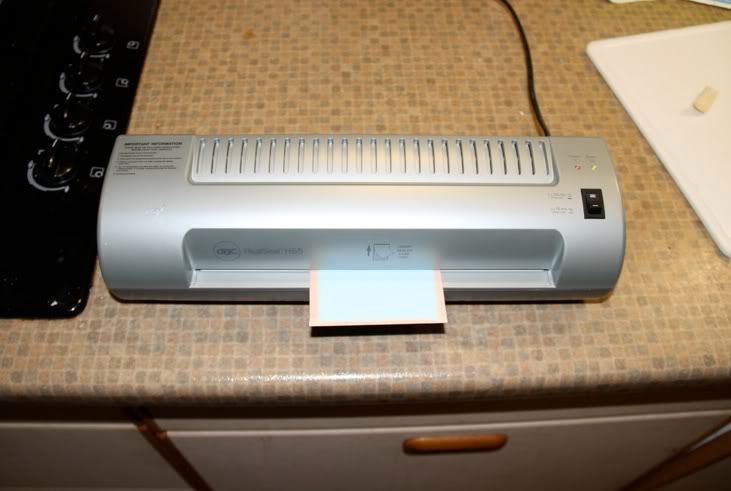
After it has been through a few times I let it cool and then soak it in water which removes the paper leaving
a black toner mask on the board
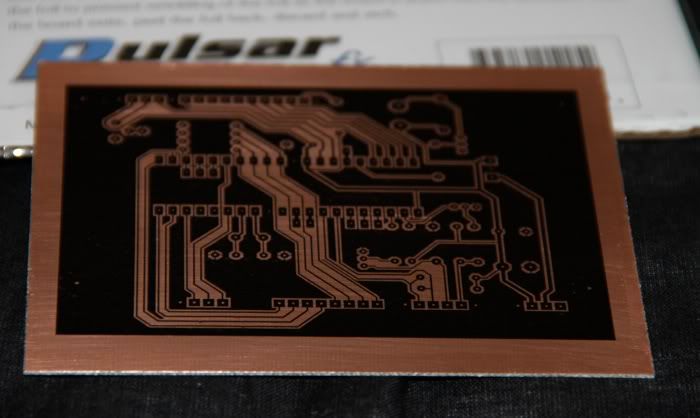
Next I wrap the board in a piece of the green foil which came with the kit and bung it back through the laminator
This is to seal the possibly porous black toner
As you can see it blocks up some of the holes but these lift out with gentle use of masking tape
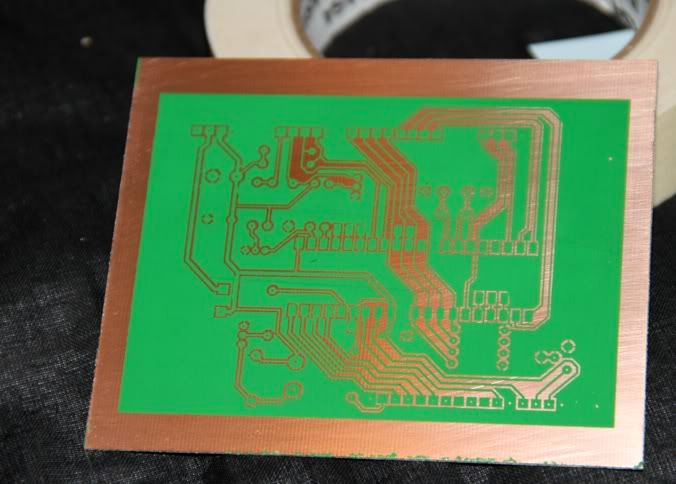
Almost there now but no pics of the etching process
I placed the board in a plastic tub with warm ferric chloride and gently brushed the board with a paint brush ( as I'm impatient )
Rinsed the board and cut off the edges with the guillotine then finaly removed the toner mask with some scotch brite
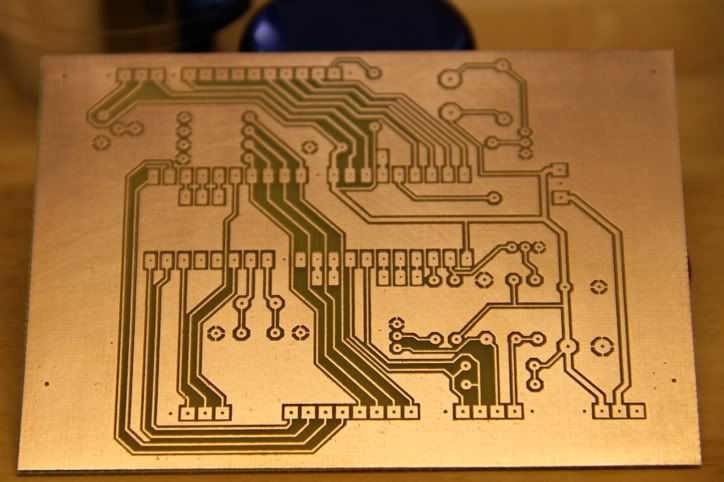
Just need to drill lots of tiny holes now
