Been quite a long night and still a bit to go as this will take a while to write up!
Continuing with the frame for poppin..
First job was to saw the job from the parent stock.
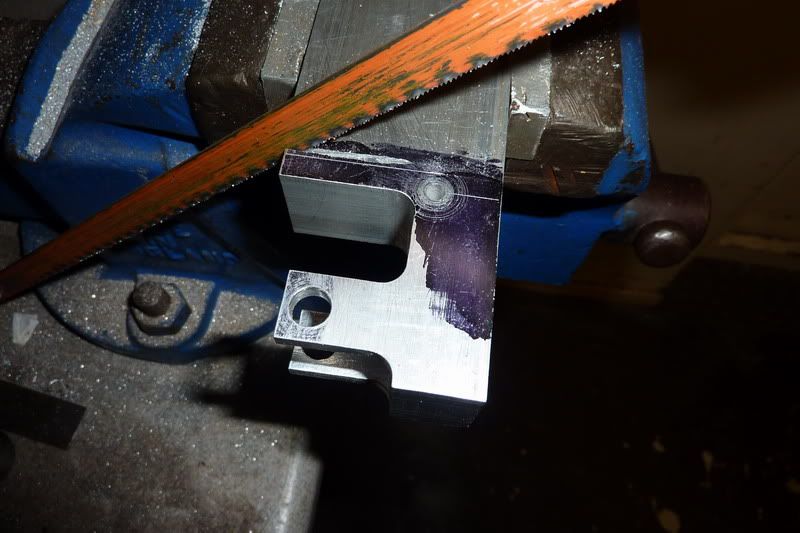
10 minutes with the hacksaw - I did such a good job I thought I'd just touch it up with a file instead of milling.
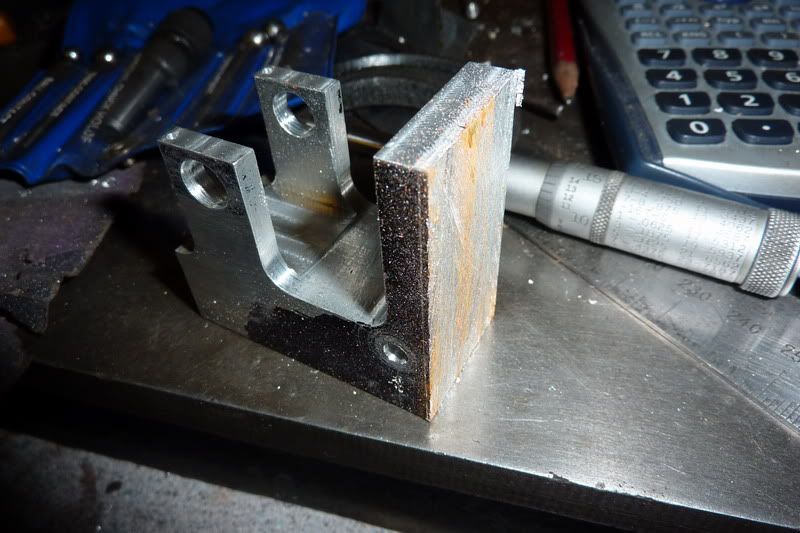
Just checking you're awake... I thought I'd try to get it a bit flatter than that so put it in the milling machine and decided to flycut it rather than take loads of passes with a small cutter. Luckily the flycutter was still set up from when I skimmed the block originally.

Then it came back out to get marked up for all the holes. (large one for conrod to pass through, cylinder bolting holes and hole for valve rod) I decided that as the width of the standard was 1" and the cyl. cover 1" it was fairly easy for me to just position the cover and mark the holes through.
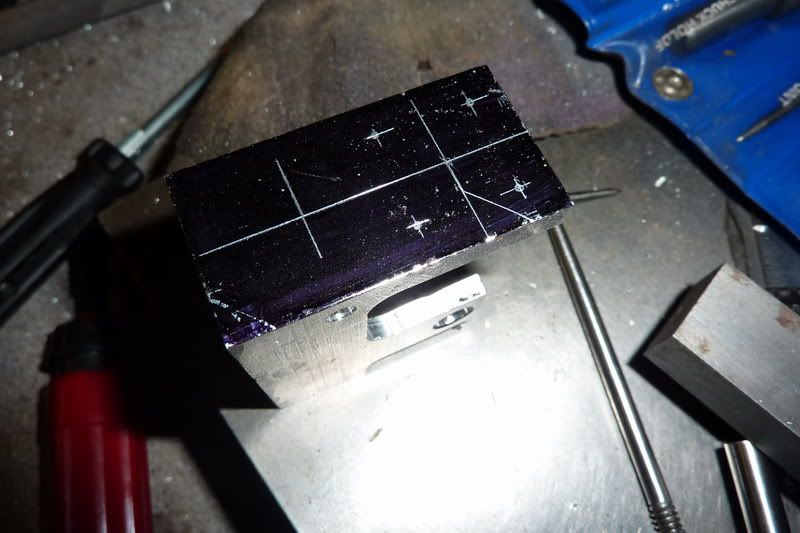
Spotting the holes.


Then starting to open the large one up:
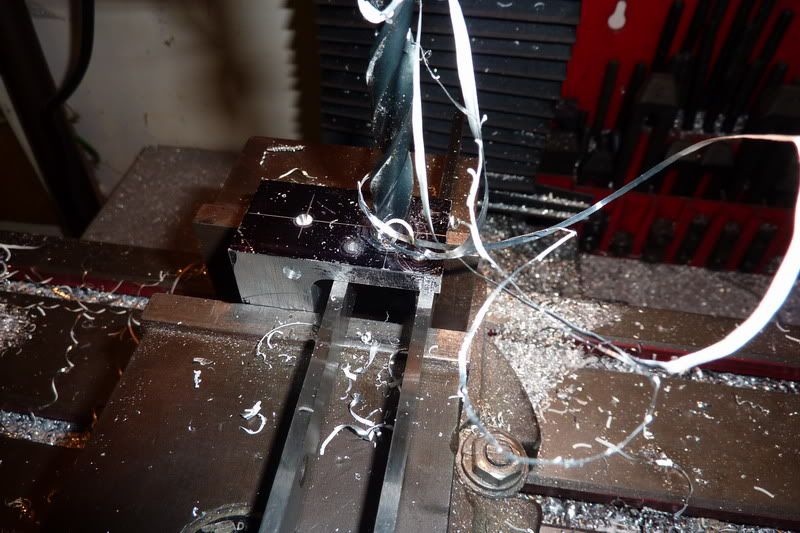
Drills getting bigger and scarier!
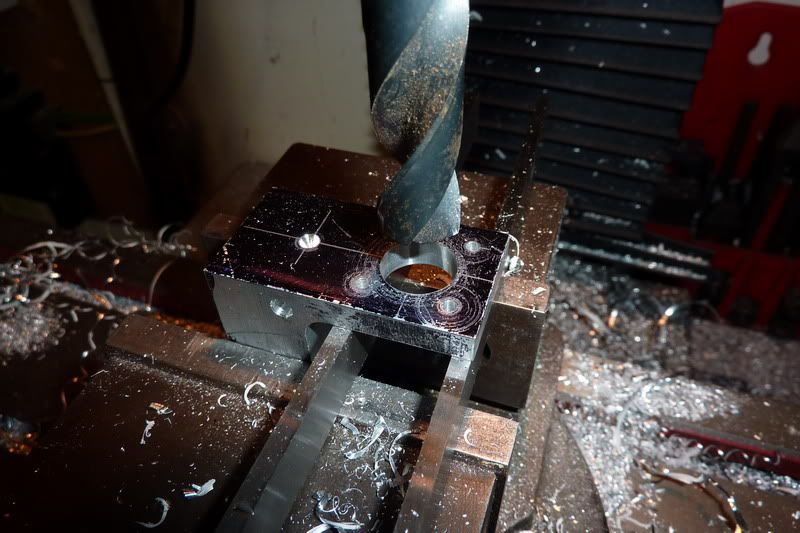
I decided to finish with the closes thing I had to 11/16", a 5/8" slot drill.
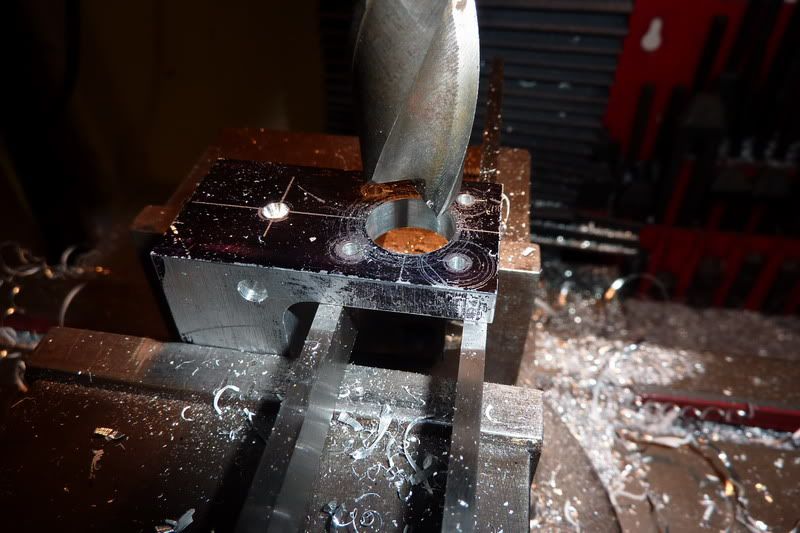
This worked really well and gave a good finish.
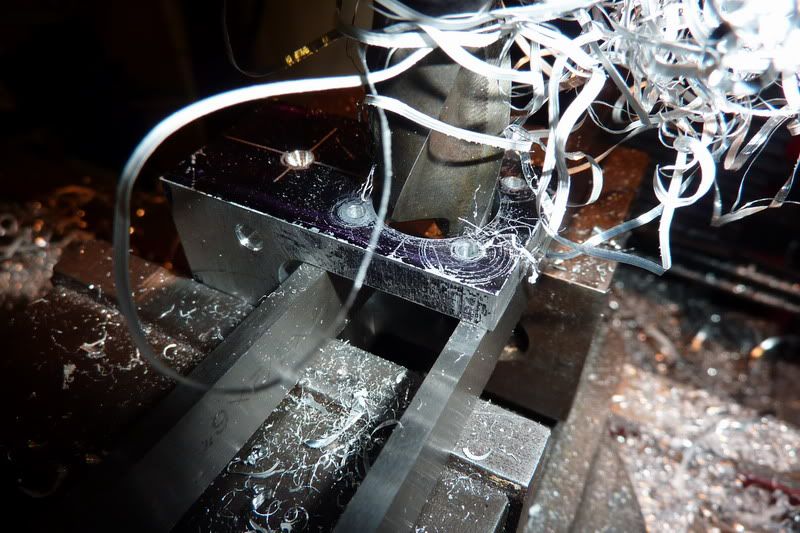
I was going to stop there as I would guess 5/8" would be big enough for the con rod not to foul. But then I thought, no, I better stick to the drawing as couldn't be bothered calculating stuff! So I found an old boring bar:
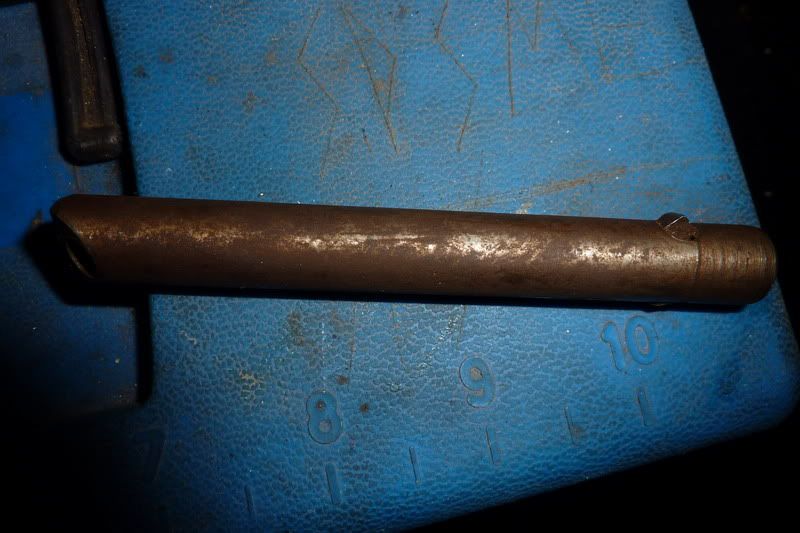
it happened to already have a tool in it. I just had to grind a bit away from the wrong end so it didn't interfere with me trying to measure it to get 11/16". I got as near as damn it to what would give 11/16", put it in the collet chuck and started boring!
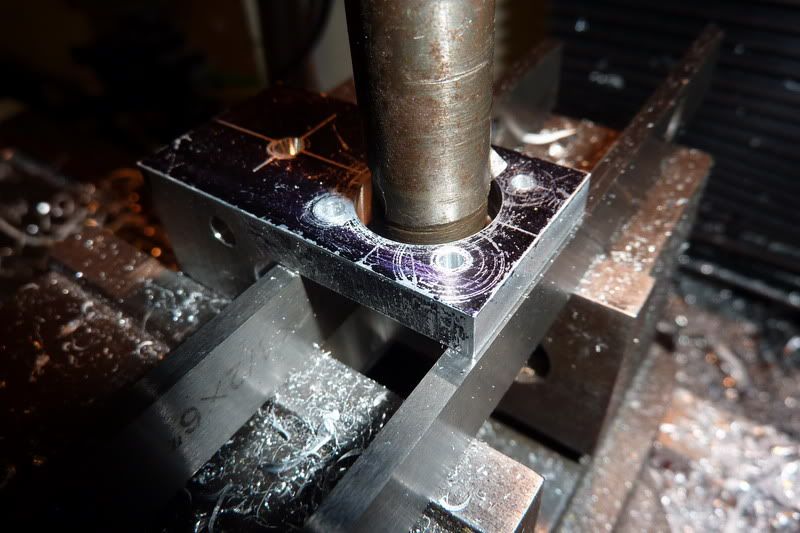
At this point I was pretty scared as it appeared to be wobbling about like a good 'un! No idea why it would do that but I think it was to do with the shape of the tool - it was a sort of v shape but with hindsight I think I should have had a virtually straight leading edge just with some rake angle and a slight clearance. The up shot of this was that it gave a rubbish finish. I think it was partly my haste using the tool that was already there and wanting to stop the operation as I thought I was going to ruin my component.
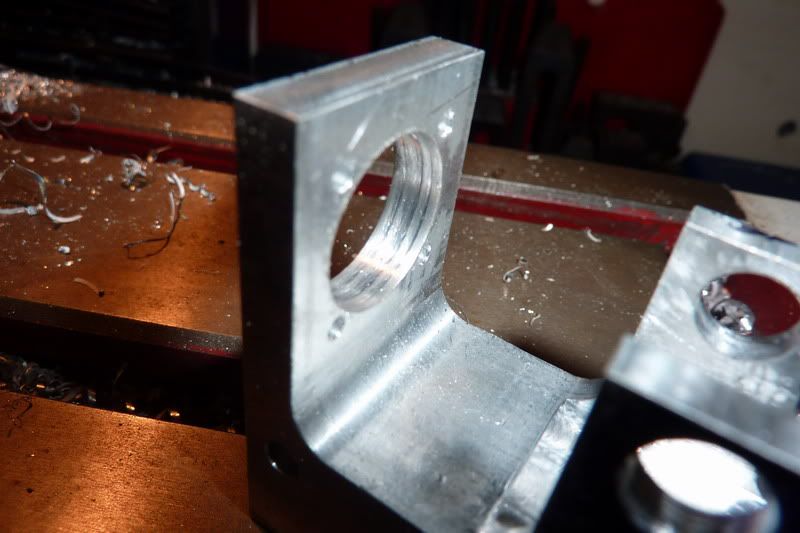
I quit with this while I was ahead (well, while nothing was broken!) with the hole at this point. I'll need to practice this boring lark on some scrap and might re-visit it if I get good results I think, or at least I'll get it right for the next frame.
Next, another scary operation. Milling the slot through the bearing holes to enable the crank to pass through. I thought I'd try out my new slitting saw arbor and one of the saws I cunningly kept from my horizontal milling machine. The concentricity of the arbor or saw must be cr@p as you could visibly see the run out (about a mm or so!). I decided as it wasn't moving up or down it should still be ok and turned it by hand a few times with it touching the workpiece trying to get it into what I thought was the best position. I made sure I wasn't climb milling and that when I'd wound it all the way through it'd cut the slot in one pass.
As I neared the workpiece the tinging noise nearly made me have kittens, I thought it was just going to bend the uprights but I thought with a decent speed (about 400 rpm?) and a slow feed it should be ok. I nearly made a massive booboo though. The slitting saw was 0.1" wide and the slot was to be 0.16". So I started off with the bottom edge 0.080" below the centreline of the bearing holes. Then I'd move it up 0.060 to do the second pass and widen the slot to desired width. If I'd have done that, it would probably have bent the top. Glad I remembered and started at the top first then widened at the bottom where it still had more structural integrity. Sorry, this is getting a bit waffley, anyway, it worked ...
I thought I'd tap the holes next. Another problem here, the 10ba tap is nowhere near long enough to go through the clearance hole and into the portion that should be threaded. It gave me 4 or 5 threads in there max before the shank started to foul - have no clue what to do here. I'll have to read the instructions to see if I've missed a trick.
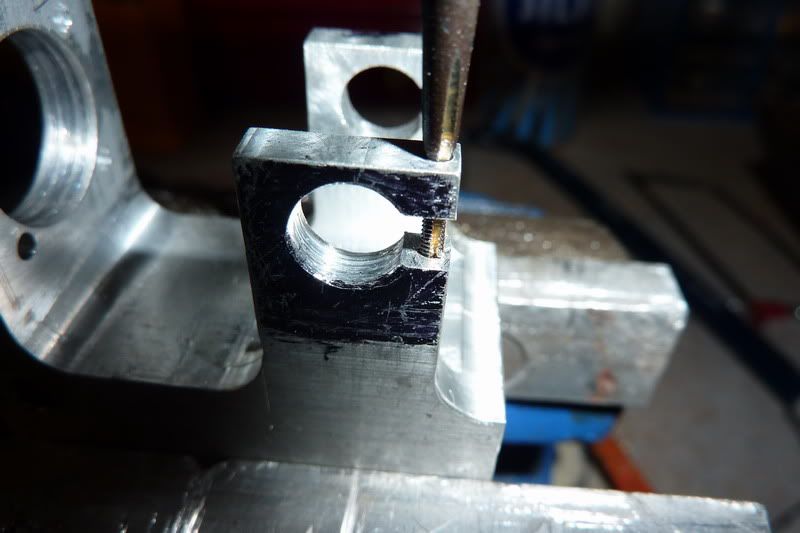
The last thing to do was to drill the 1/4" hole for the valve rod that meets the cross hole for the valve shaft:
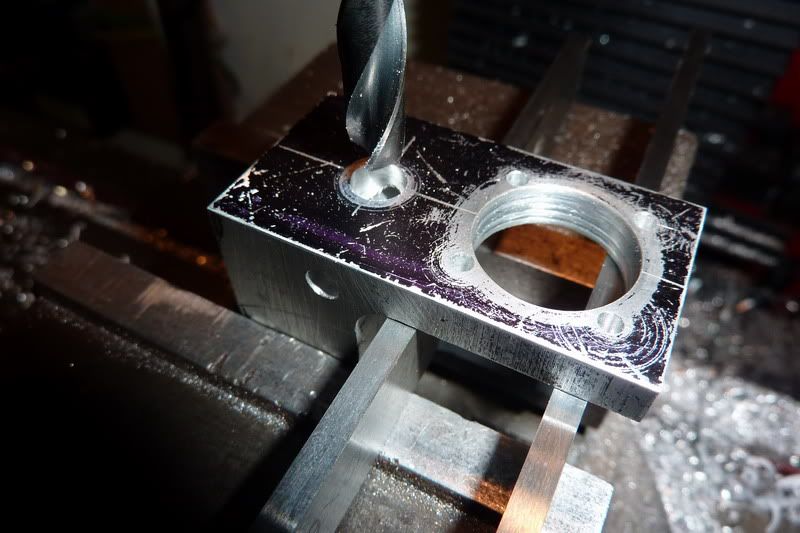
That went well. I cleaned the thing up a little and here is the finished standard or frame:
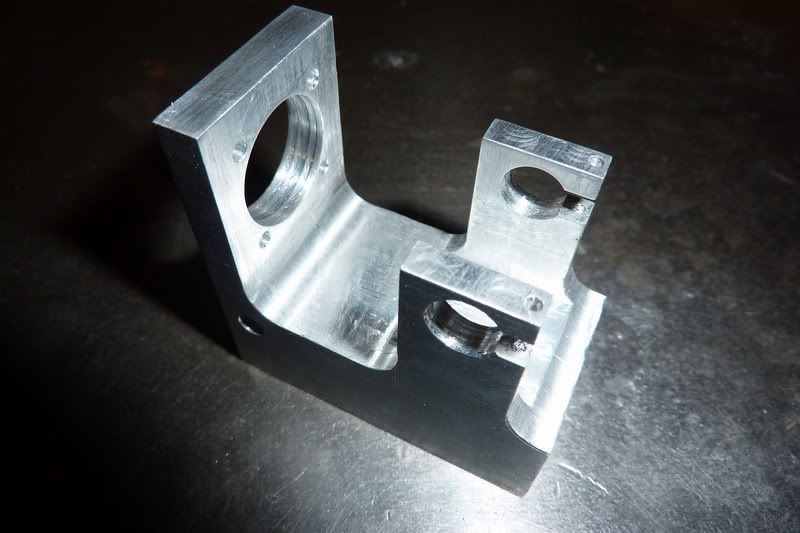
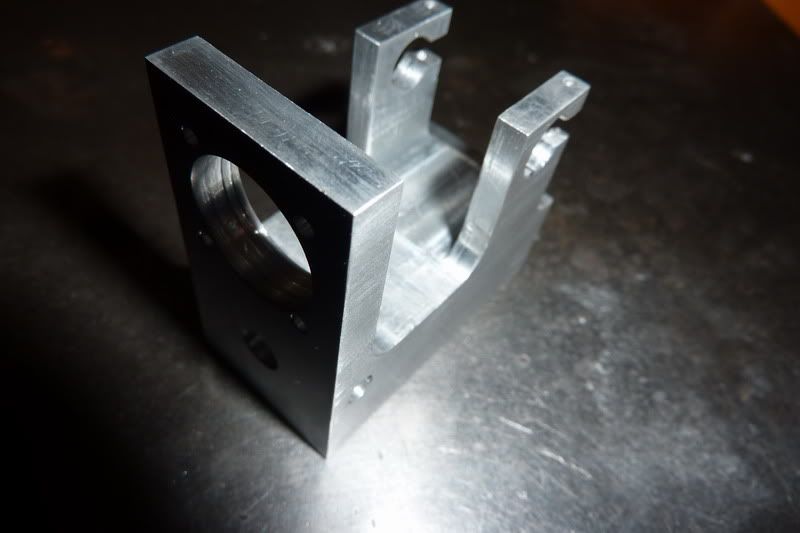
Actually it's not finished - I forgot to drill any mounting holes in the bottom but was too late to start, don't want to ruin anything due to being too tired!
I really don't want to make another one of these right now. I think I want a change of scenery so to speak so might crack on and make some other parts and come back to the 2nd frame!
Nick