Yes sir, Andrew, there's nothing like melting metal, and in melting metal, nothing like melting iron. It definitely get's the adrenaline going for me. And the mystery of what you're going to uncover loooooong hours later in that molding box.... Will it be a disappointment, or the prize you imagined?
So, the next day, though originally predicted to be less suitable, actually was even warmer than the day before, and the precipitation predicted, turned out to be only a few flakes of snow in the morning. Then the sun came out and temps rose to 50F. A true winter thaw.
So out with the second pattern for a cylinder. I scraped off the bottom of the crucible by "sanding" it on the concrete pad. The bottom was restored to a flat surface again. (btw, I had placed cardboard under the crucible last time, but that didn't prevent the sticking.)
Where the crucible had sat in the furnace, I removed all loose material, and painted on some of the lining hot face compound. Then I dried it with a torch, and put cardboard over that, and used a quarter piece of firebrick as a new plinth. Firebrick had worked in my old furnace, though it didn't last more than a few melts in the role as plinth without cracking. But it did work, and I thought I'd give it a try again. On top of the brick, more cardboard, and then the crucible.
I did a rough calculation of the metal I'd need for the cylinder - 7-1/2 pounds, and this time charged the pot with chunks of cast iron I broke from an old cast rail. Shaped like a railroad rail, though not one obviously, since cast iron. I knew that stuff had worked well in the past. I also wire brushed it, and rinsed it in fresh water to get it clean as possible. No old sprues, this time.
In molding, I did also try a little of my first attempt at sawdust facing sand mix, but it had no bond strength and simply crumbled. I removed most of it (but a little remained at the bottom of the pattern cavity, only). So again, no facing sand.
Melting: I added a little more ferrosilicon to the melt (estimated by eye only). I also melted for a shorter time, because I think I overdid it the prior melt. After all, iron doesn't really melt in 10 minutes from cold does it? Well yes it does, in this furnace! So this time the melt took 20 minutes total, instead of 40 for the previous one. I was able to slag it part way through, in the furnace - which netted quite a big gob of the stuff (some of it no doubt left over from the day before.)
The crucible lifted easily from the new plinth, and I was able to set it down properly in the ring shank, I tried slagging it again there but didn't do a perfect job, as the slag was sticking to the tool, and the handle was overly long and clumsy for the job, out of the furnace. I'll have to make a new shorter one for that purpose.
The metal poured nicely though I saw one bit of slag run into the sprue after detaching itself from the crucible wall. Maybe it would get trapped in the sprue or gates. The metal poured perfectly down the sprue without a spill, until.......it stopped. Oh no!
Oh yes, you miscalculated the amount needed, you idiot, and short poured!

Well it came part way up the sprue, maybe there's hope. Fingers crossed!
Yeah, right. Afraid not.
Anyway, the concrete core worked perfectly, just like ironman's. Thank you IM for all the information you give people, all the great ideas and experience!
As for the casting, well it probably would have been good, other than the rough sandy external finish. The internal finish was quite nice (due to plumbago on the core). It would have machined reasonably. Also the metal was much nicer, when drilled producing bigger crumbly graphite laden swarf, as it should for good gray cast iron.
Interestingly the short poured top of the casting had a good finish (probably reducing gas from the small amount of sawdust. It did have rounded ridges suggesting the edges of a gas bubble under some pressure. However this would likely have dissipated though the sand if the pouring head of iron were higher in the sprue. The height of the casting surface and the sprue matched.
So, needed: new slagging tool, new sawdust facing formula, new spreadsheet calculator for common shapes (being worked on presently) for estimating metal, and ferrosilicon required. And we'll try again when the weather cooperates.
Finally, besides the learning involved in these two pours, I also had to re-think my design for the patterns and the need for subsequent machining, as well as the actual design of the engine. People may have noticed I removed the original rectangular flange from the cylinder pattern. But I've also realized these castings are just too thick and heavy for machining in a reasonable time on the equipment I have.
I think the piston pattern would work as a tapered greensand core type, but the machining would be unnecessarily time consuming. It would better be a split conventionally cored pattern, with a much thinner casting thickness. And the piston top might be a pressed in piece instead of cast in. And likewise the cylinder pattern could be reduced in thickness if not only the flange but the water jacket support rings were altered in design.
Anyway, good to be casting again, and very happy with the new furnace lining. I wish I could have afforded it a decade ago, but I used what I had on-hand and got what experience I could with that. That informs what I do today.
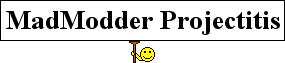