Got a salvaged pump taken from a scrapped industrial drill press: they told me it’s three phase, but it can also be wired to single phase. I don’t know how, yet.
First of all (that’s even before knowing whether the pump is working or not) I made the sump out of an old plastic tank, a plastic IKEA chopping board and lots of sillicon glue.
Turning that chopping board into the lathe was fun: once in a while the machine didn’t complain about the depth of cuts. (Them chips were a pain to clean, tho).
Here’s the pump.
A quick glance into the “plumbing stuff” box revealed some usable items: a second valve is missing, together with some small fittings,
but the problem will be easily solved next time I will get close to an hardware store during opening hours.
The two plastic strips with holes and screws in the above photo should act as a (temporary, You bet) pipe securing clamp:
I will put it upside down under the bench top, tighten the clamping screws over the pipe and then screw in the other two
(maybe four) screws against the ‘roof’ to hold it steady. A 14mm nut will do a better job, the day I will find an M14 die.
Threading that short pipe into the lathe could be an option, too.
The idea being to have the coolant feed line split into one line going to the work area and a second line (that short black rubber pipe) going back to the sump
for flood regulating purposes. Of course that second line might be used to feed coolant to the lathe, the day I will get around to it.
The hardest part of the job was hand drilling a 13mm hole into the bench top for the pipe to pass through: had to deal with a wobbly gun drill and a blunt bit.
You might appreciate a picture of the mill and her dentist’s lamp, sitting on the self made workbench
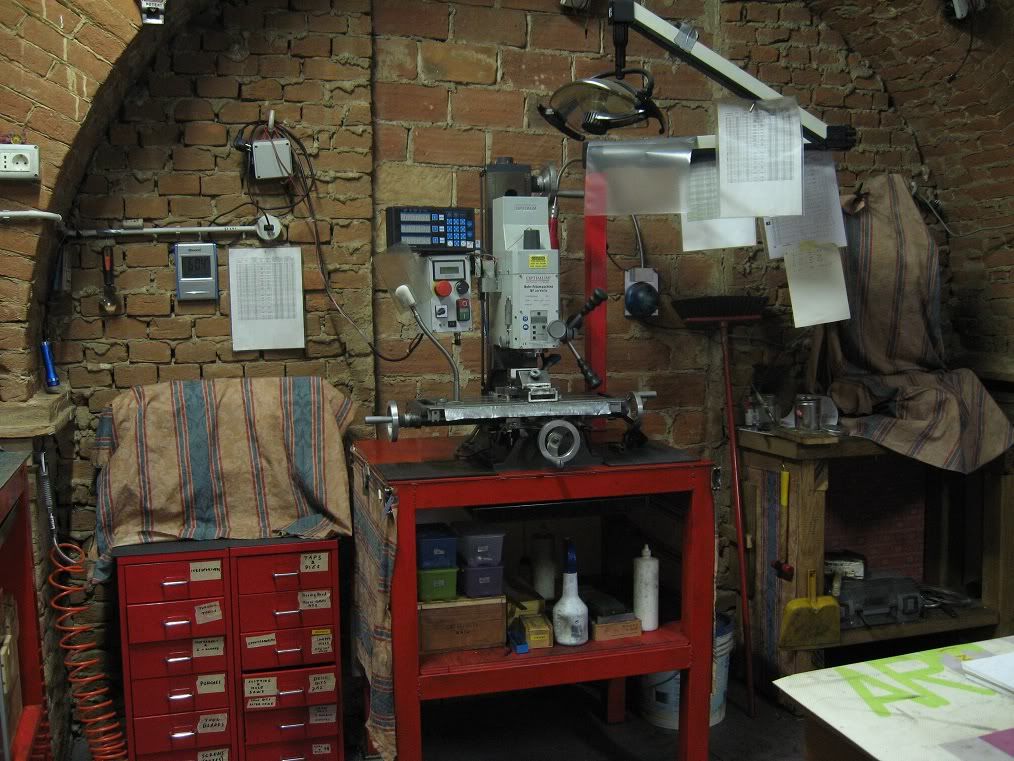
(Please, do not ask for close pictures of the

welds).
Marcello