hi mat same lathe that i have
Krv,
I'm very pleased with the Emco, my first screw cutting lathe!
On to the casting, when I started looking at the dividing head project, I spent some time thinking about the casting. Three things came to mind:-
i.From my little experience of casting, I thought that I'd never manage the gap the middle, so I left it out.
ii. The original being made of cast iron, (I presume) so I made mine with fatter flanges to have a stronger base.
iii. My banjo pattern I made without the ribs as I thought that they would make the moulding more difficult. Rob Wilson had told me that the ribs were to make the milling easier on the lathe so that decided me!
It's been nearly ten years since I cast anything, I've been preoccupied with my major home and workshop building project. I had bought "regenerating paste" for my petro-bond sand, it was already in need of reconditioning when I left it, now, it was in a sad state, so, first things first, re-work the sand, by hand, a couple of times, as I didn't want to overdo the "paste" and I just couldn't remember what it felt like when "right". It took four goes at ramming the mould before I got it right, without forgetting the the breathers, having it collapse and the worst, putting it on backwards, as I hadn't put eccentric guides to make it go back only one way!
I've been following John's excellent videos very closely, I owe him my gating (Thanks John!!).
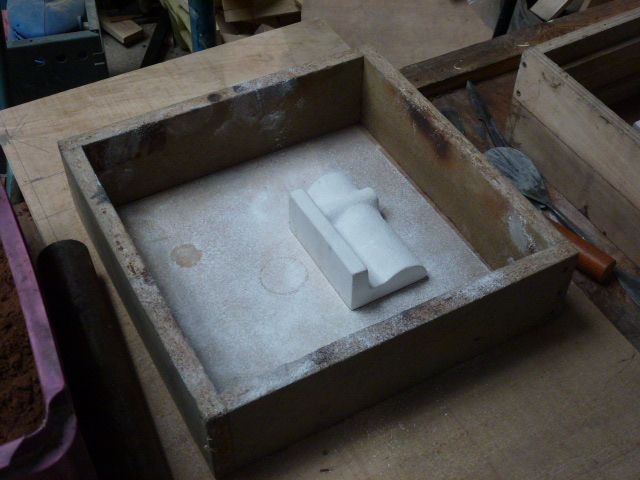
It had been so long since I'd done any casting, that I really hadn't much of an idea about how to go about it! I realised that my pattern was smaller than John's and probably less volume, so if his last casting wasn't too bad (I couldn't see it in the video), mine might work out. So between John's videos and the US Navy Casting Manual, I went with a 30mm diameter sprue and a 50mm hot riser with a fairly generous gate.
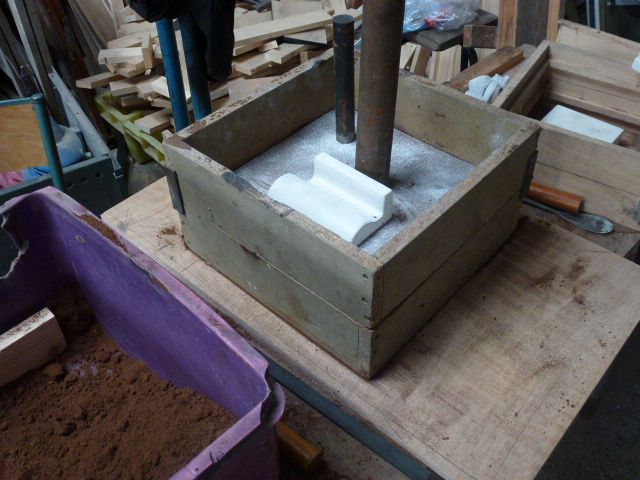
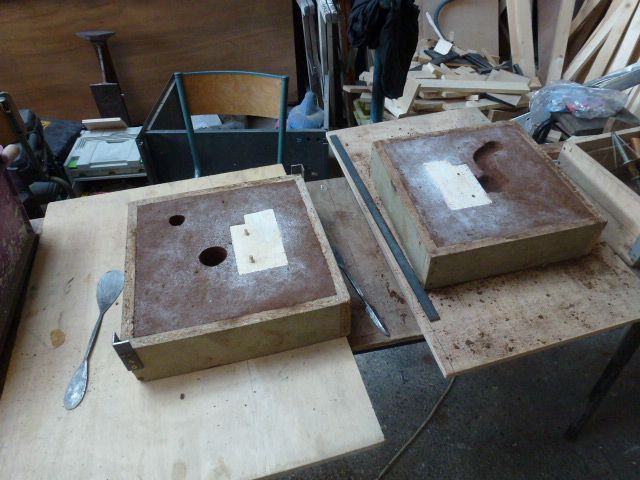
Scatter brain forgot the breathers on one ram up, when I opened it up again, the sand collapsed, I rammed it harder for the next one!
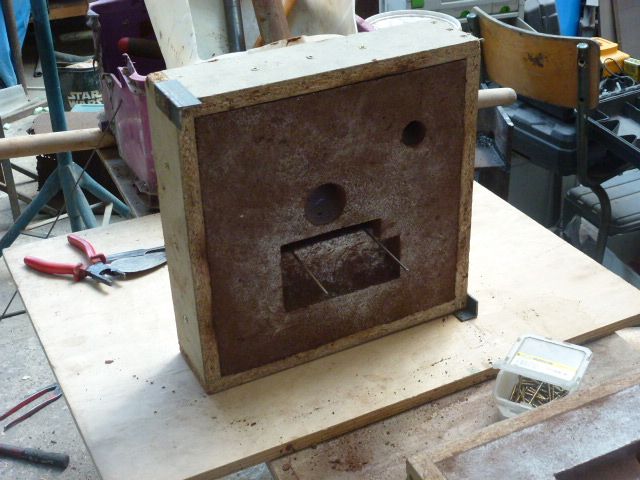
I don't remember where I found this idea, so I can't give credit to it's inventor. It gives a nice smooth sprue funnel easily
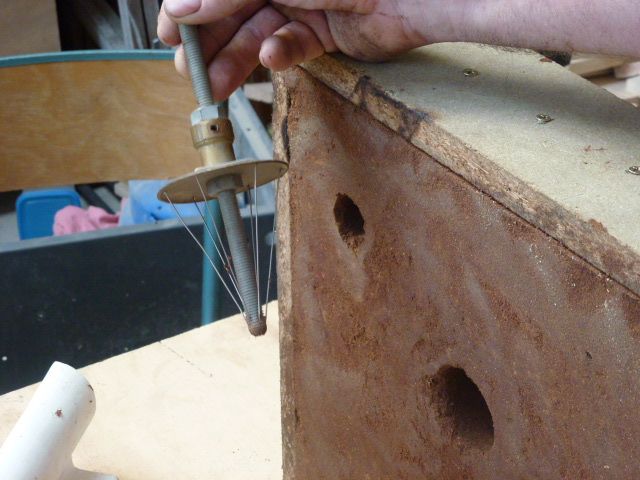
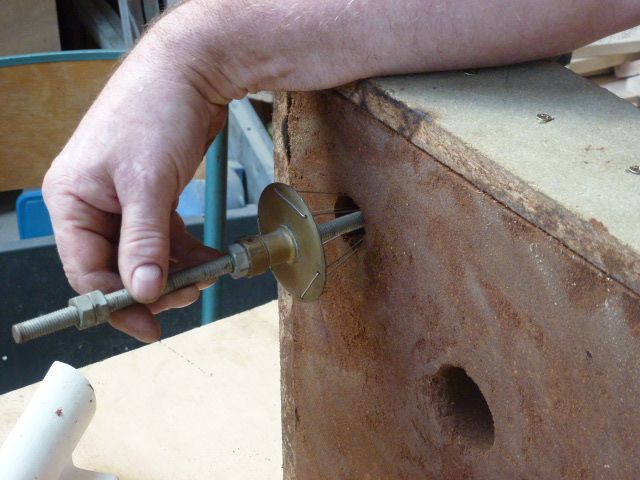
my foundry.
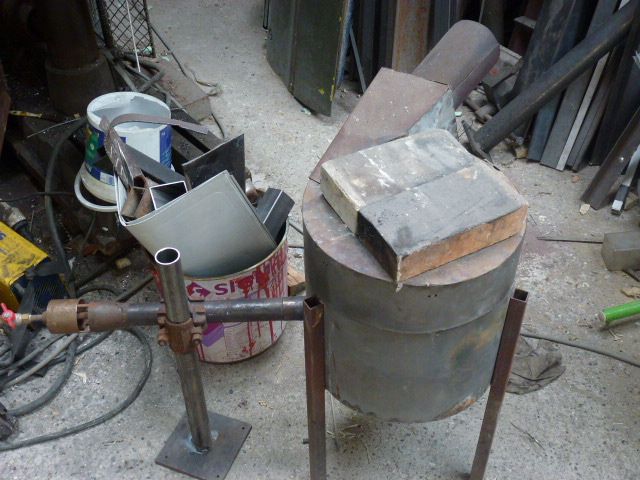
I broke the lid a long time ago, so it's two firebricks for the time being!
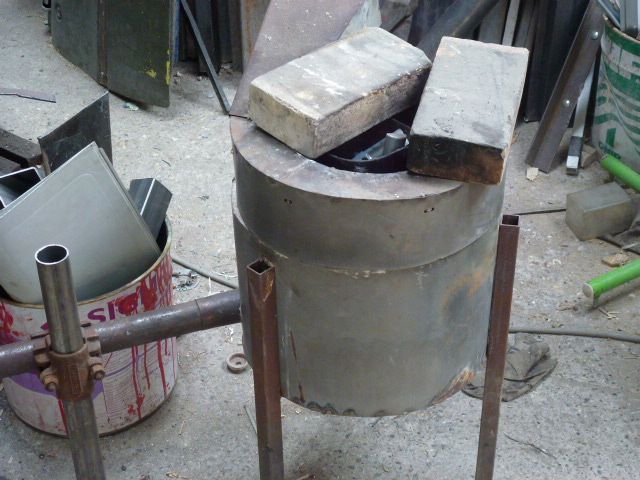
The result, with which I'm pleased (Thanks again John!)
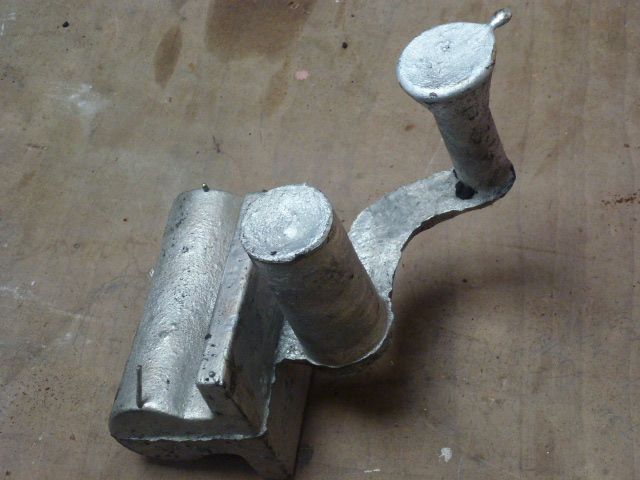
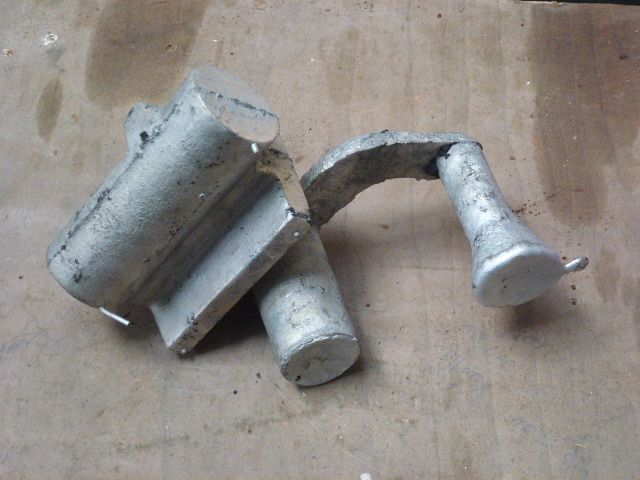
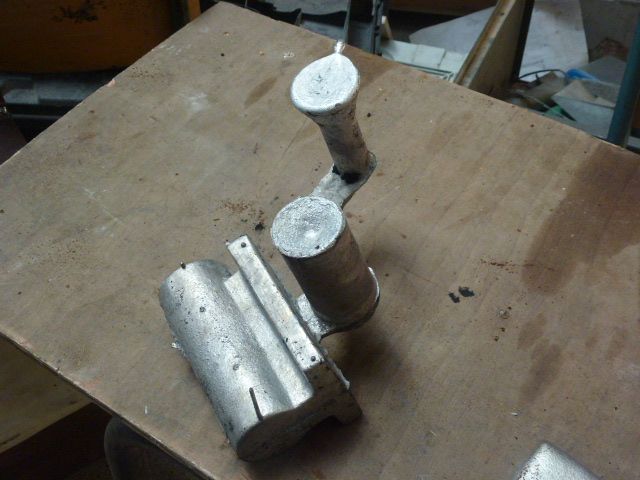
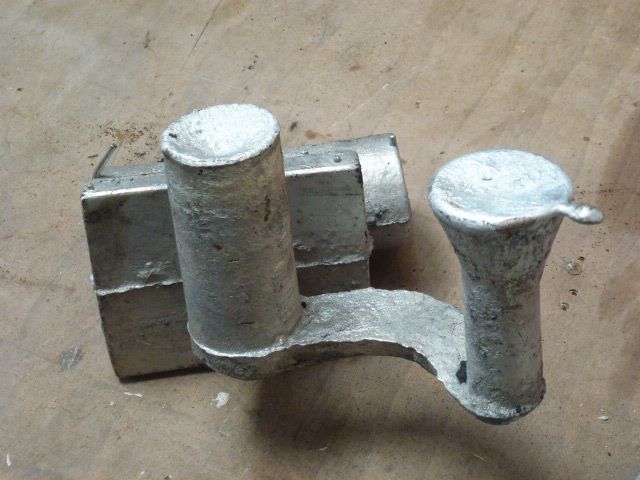
So while I'm at it, it's time to ram up the banjo and the riser block!
Regards, Matthew