Hi,
I've been a bit apprehensive about the next bit. I've only done a couple of threads before. I decided to make the spindle threads first, I've got a lot of work in the spindle, so get it right, then even though it's supposed to be easier to fit an outside thread to an inside I wouldn't mind making nuts as I would making another spindle!
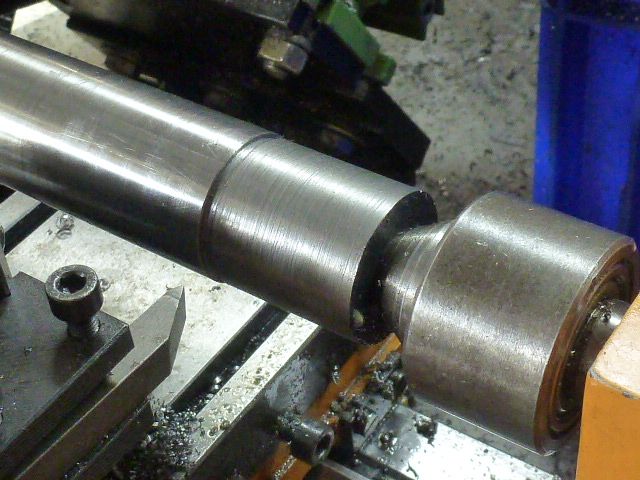
I turned the end of the spindle down to 28mm, (2mm under the spindle diameter) and turned a run out for the thread.
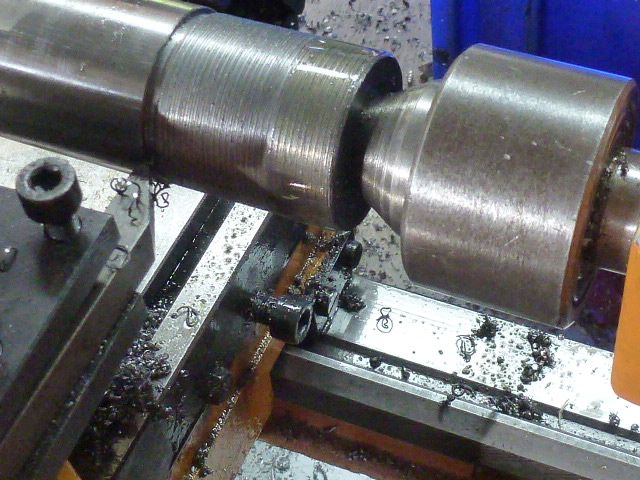
So far so good, M1 thread, first pass OK with the right pitch.
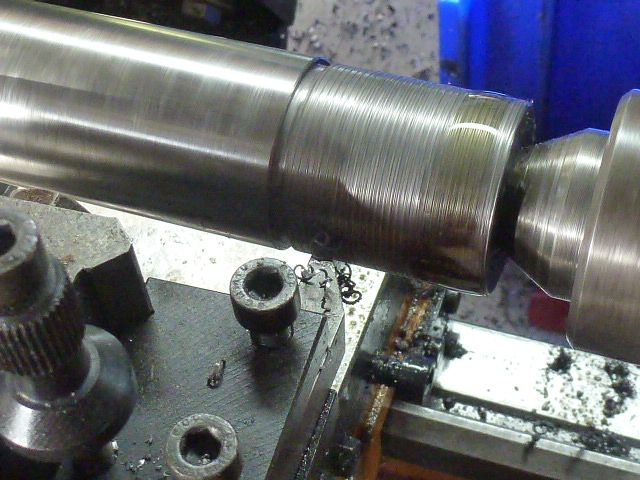
I didn't use the top slide although it was set at 29.5°, I felt I' mix things up, a 1mm thread is only half a millimetre per side the depth of cut is easier on the cross slide.
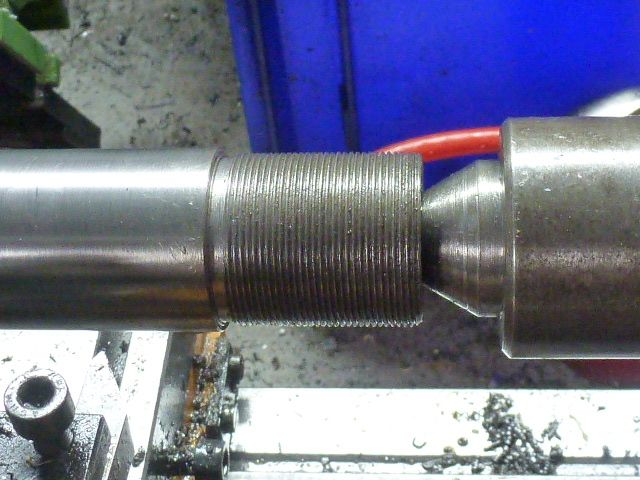
That was a lot easier than I thought! Had I screwed up I could always make it a 27X1mm thread!
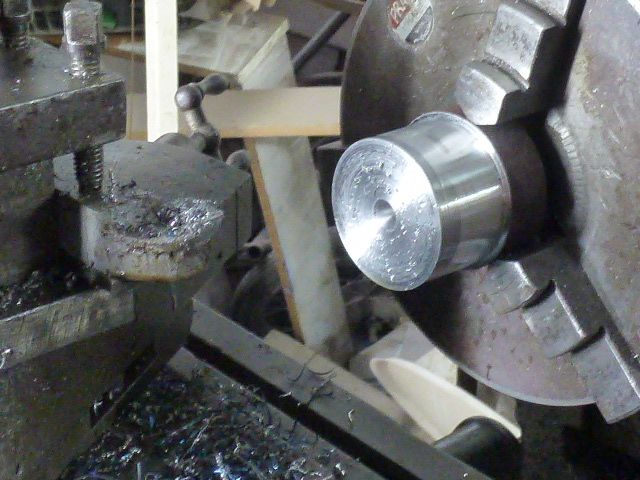
On to the nuts, I roughed these out on the Colchester, faster and capable of drilling bigger holes.
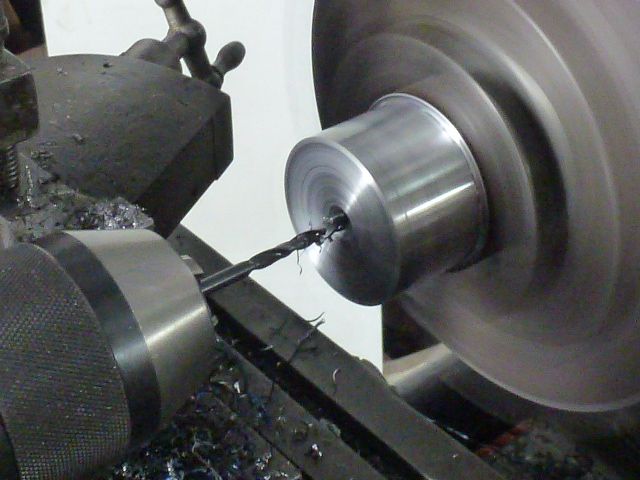
The usual, after centre drilling step drill.
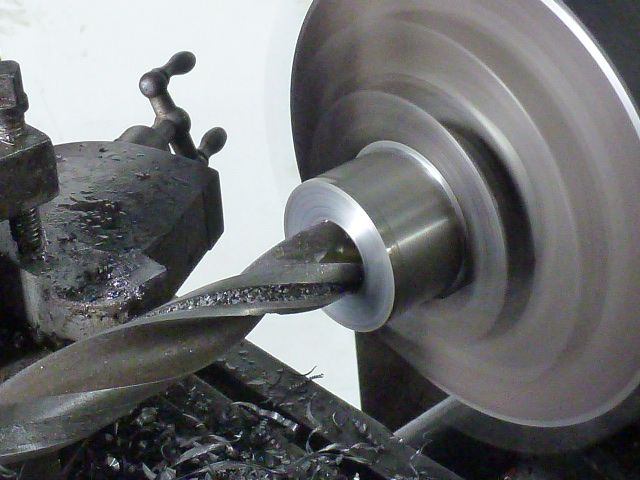
I seem to have missed out a few steps, I've gone from 6mm to 22mm, there were a few intermediary sizes in between.
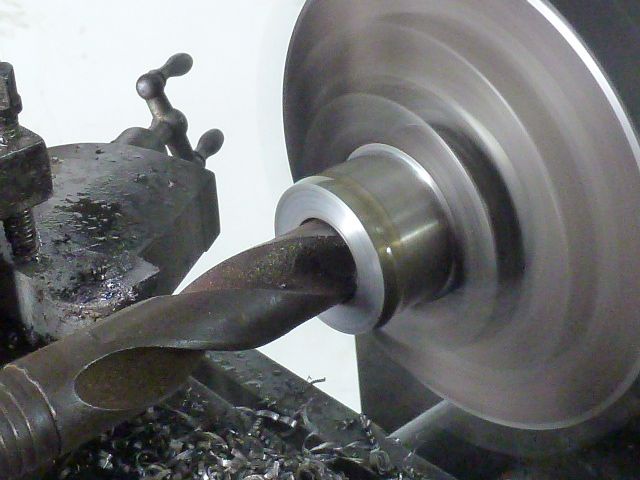
Final size, 25mm.
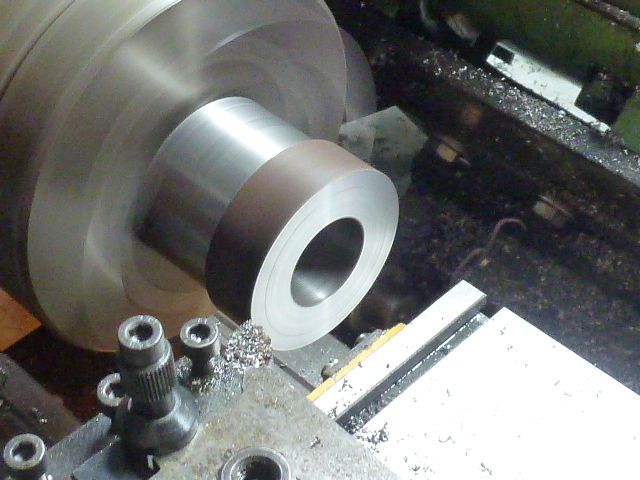
Back to the Emco, the three jaw chuck is pretty accurate, I could now true up the rusty bit to be able to have a nice symmetrical part.
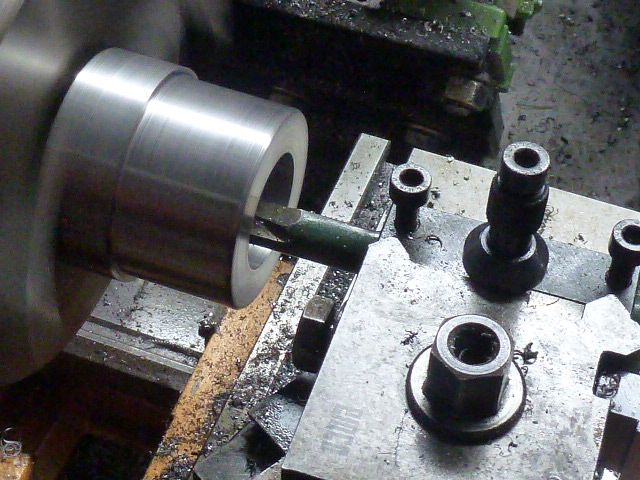
Boring out to 27mm for the 28x1mm thread, which is close to a 24tpi thread.
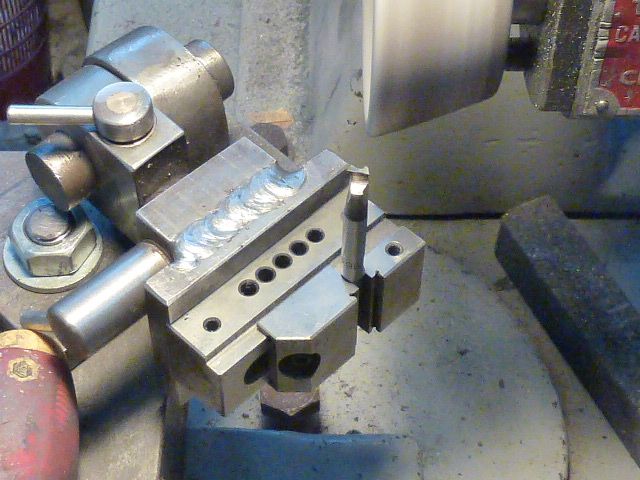
I re-ground a broken tap which was easier than making an internal threading tool. It would have been easier to use a larger metric tap as they are all 60°. As the "point" is only a 0.5mm triangle, it's hard to see. A longer reach would have been better.
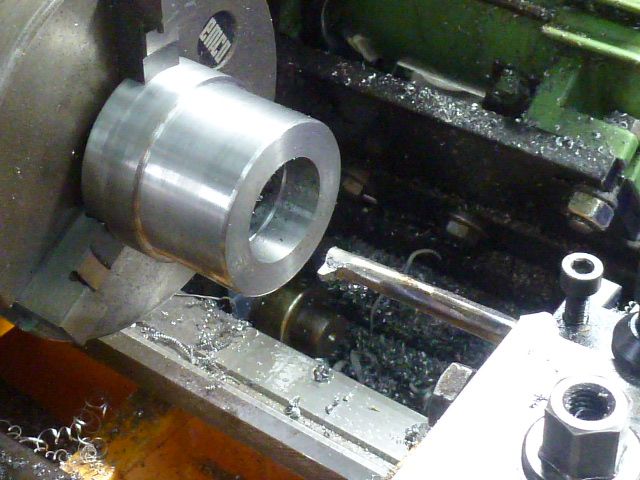
I had amongst my second hand tool bits a an acme tool bit which was a good size for making a run out groove for the thread.
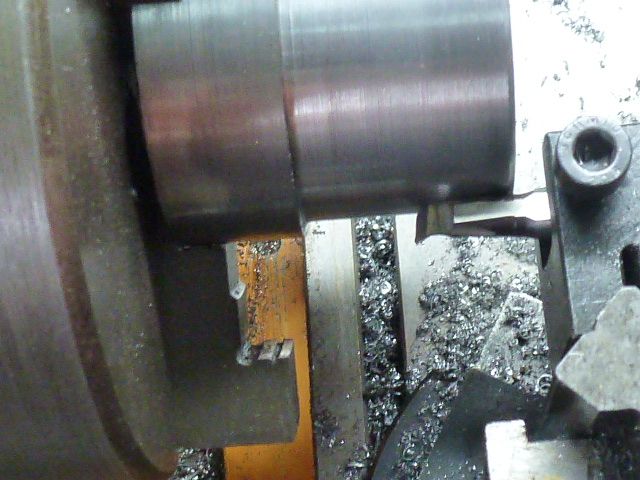
When I ground the tool, I ground the back of the tool parallel so that when lined up with the part, I knew it was square with the job.
I was a bit concentrated on the work in hand so I forgot a few photos. Amongst other things, I had to run the carriage half the length of the bed to be able to test fit the spindle. It all went smoothly and I ended up with a nice fitting thread.
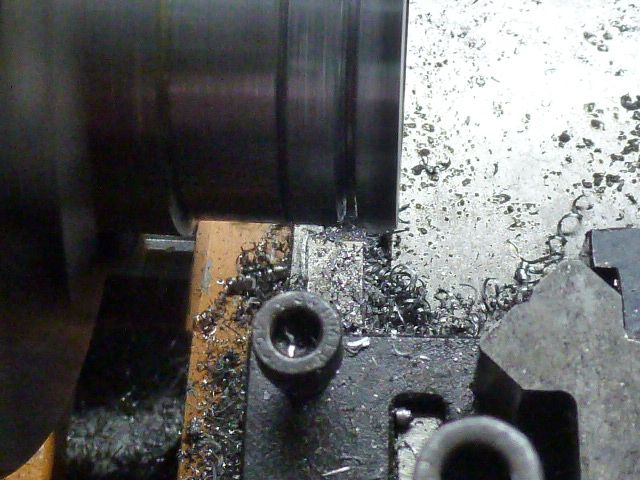
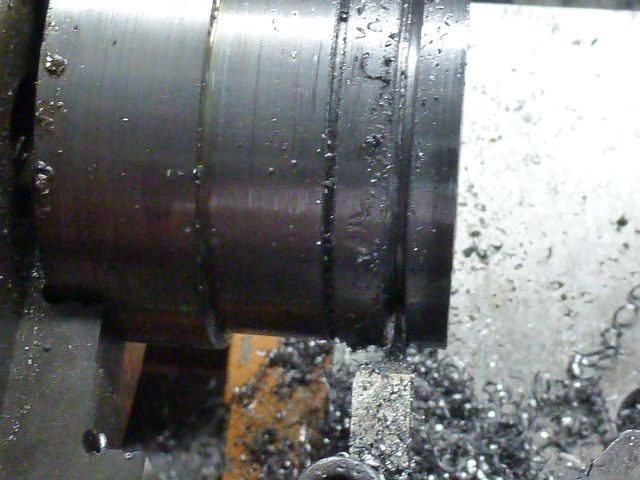
I need to make myself a decent rear mounted parting tool. I improvised and ended up finishing with the hacksaw. It was the last straw for the 25 year old drive belt which had already stretched, it snapped in half.
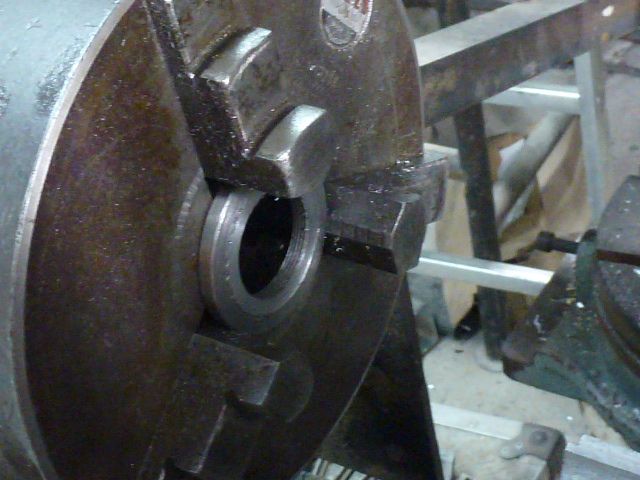
The broken belt meant that it was back to the Colchester three jaw, which, isn't the best thing to surface thin nuts. however, I was able to work on the centres which at least were parallel with the face of the chuck.
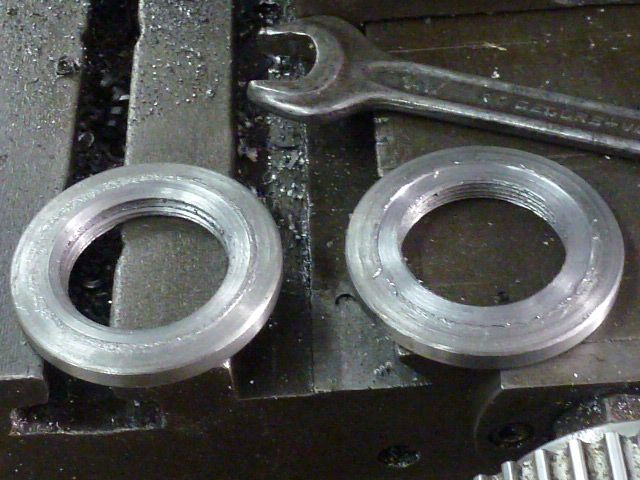
The two nuts.

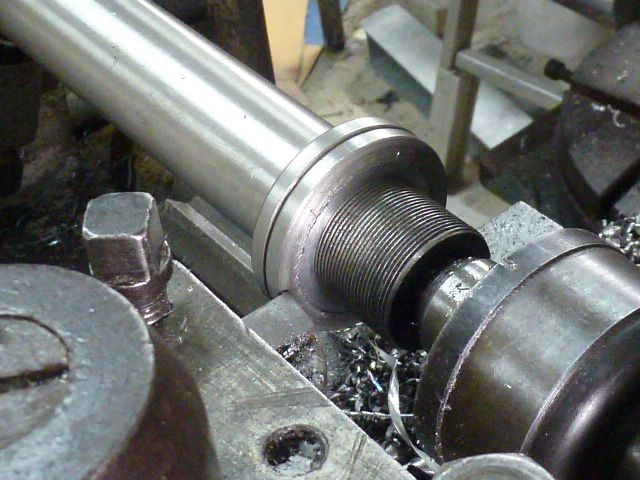
I was able to use the spindle as a mandrel between centres to surface the nuts.
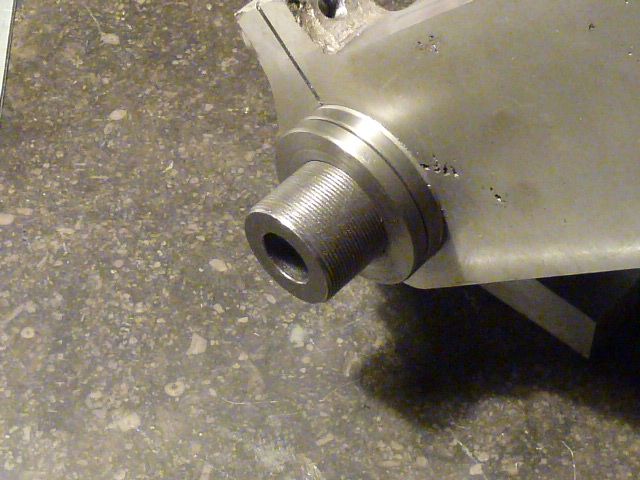
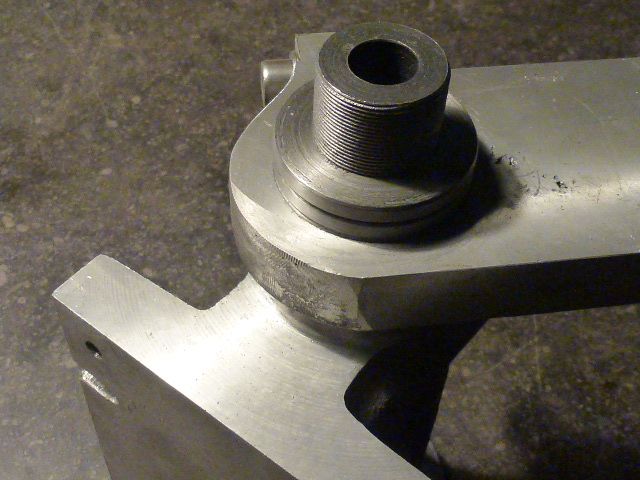
I had thought that I could use the dividing head to drill the holes in the nuts, but without the drive belt, (It's on order from the UK, out of stock in Belgium) it would be a bit difficult.
I'm pleased with my threading and the end result, now it's make all the little bits.
To be continued.