As many know most of my work is emergency repairs and some jobs can be very testing in setups and methods
Today got the usual rush job in about 2:00 pm. Stonking great lovejoy coupling off a 75 HP motor off local water treatment plant.
seems the grille on the input for the pump rotted away and it sucked a tree into pump which didn't do it a lot of good.
Screwed the end off the motor which was 65mm diameter and has an 18mm keyway in it.
Motors is no panic, fit brand new motor and later refurb the old one as a spare.
Problem is the coupling, motor side. it's shredded the rubber coupling, no swaet new ones available but it's also ripped the keyway out of the coupling and tatered the bore up.
Ok rebore out, press, loctite and pin new sleeve into position, pretty standard, nothing new or unusual but it now requires an 18mm keyway 75mm deep in the new sleeve.
I only have broaches to 16mm and do not have a 65mm bushing anyway.
Slotter still needs some work doing on it so grab the Quillmaster with right angle extension and off it up to see if it will go 75mm down.
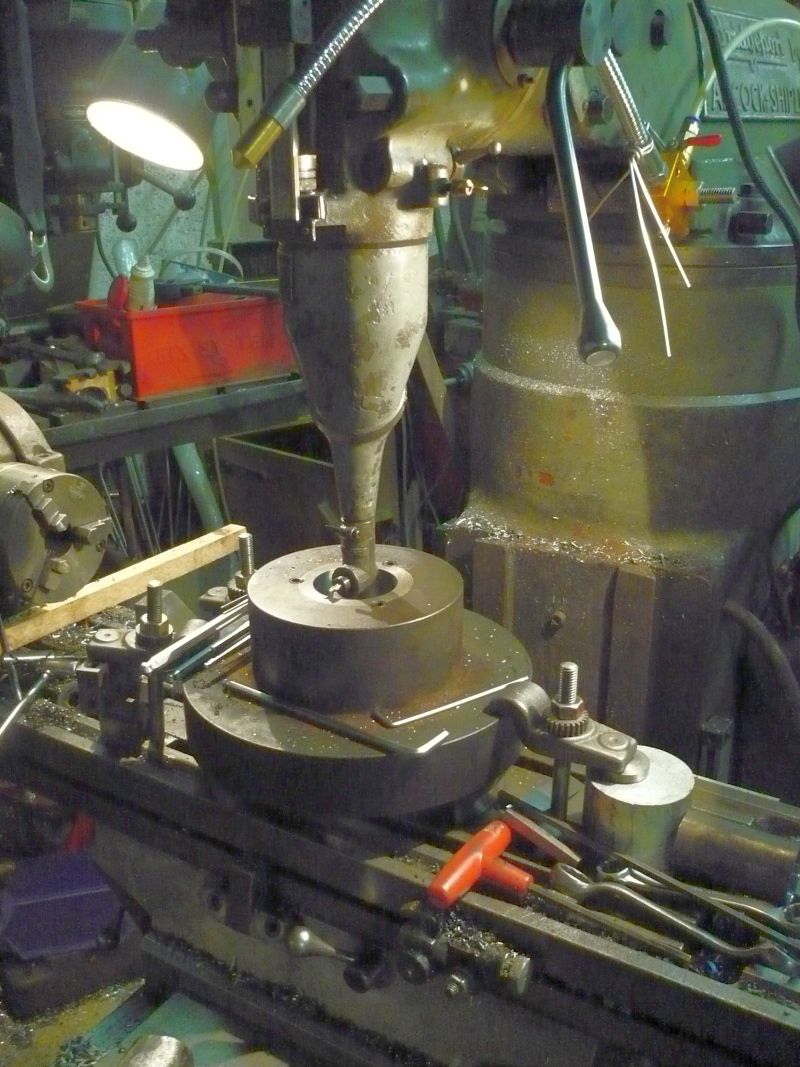
General picture of setup.
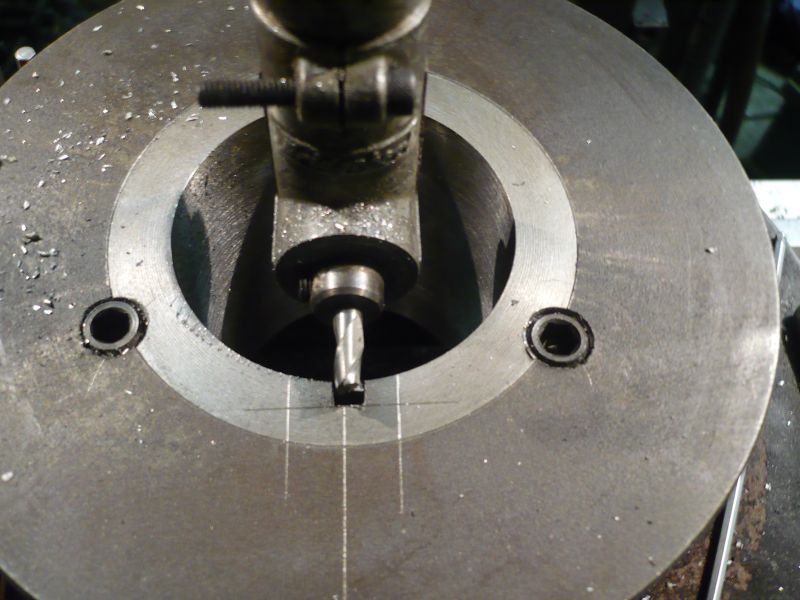
Close up of the first cuts, keyway is laid out to give a guide to follow. Cutter is a stubby 5mm carbide. The right angle extension should take 3/16" shanked tooling but it's hard to find over here so it's been bored out to 5mm.
Head was checked from trap and the quill was used as it's quicker than winding the knee up and down, up and down.
In that much of a rush, forgot to get a picture of the finished keyway as the driver rolled up early