One of the reasons for buying the laser cutter was from a post I saw on this forum where some guy [ only posted once and never returned or answered PM's or email ] mocked a cylinder head up for a model Subaru out of 1.5mm card.
Can't show some of the work as it's proprietary and the customer doesn't like work splashed round t'internet so did this instead.
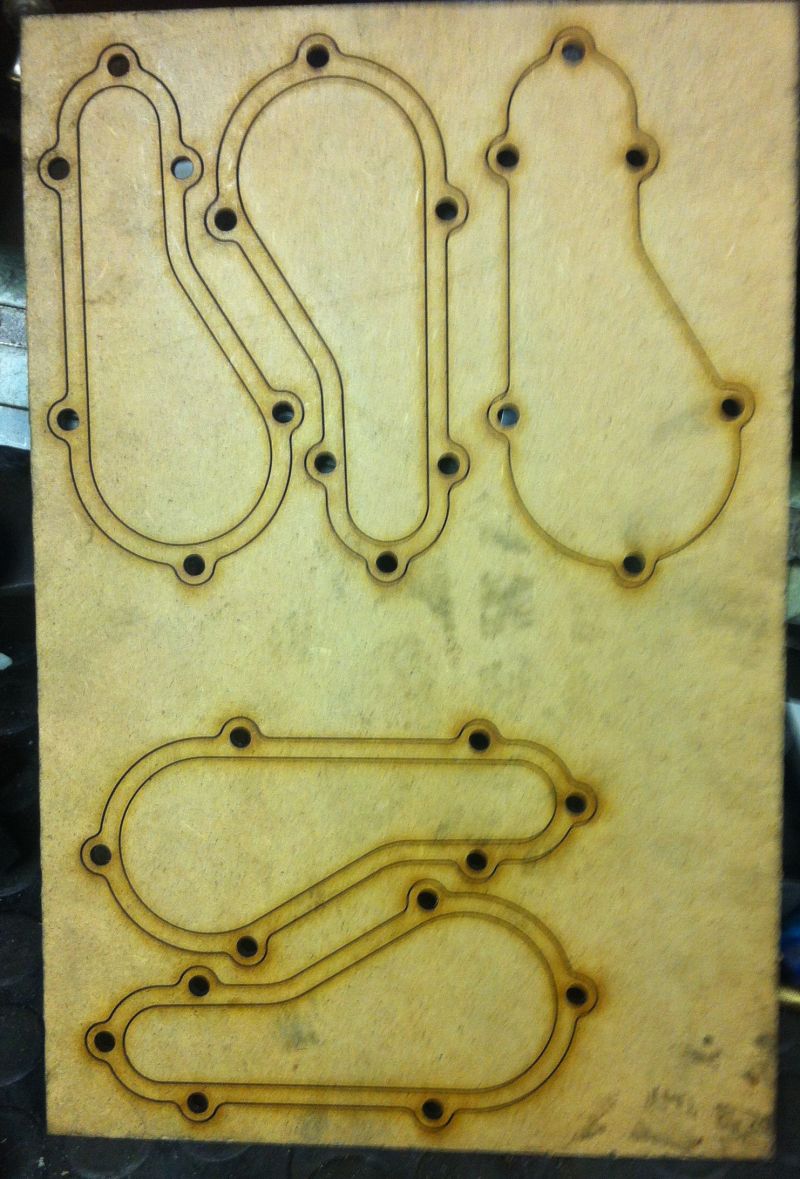
Five layers cut out of 3.2mm thick MDF to replicate a timing cover or similar.
The holes are needed to accept wooden dowels to line up whist the glue is drying under clamping pressure.
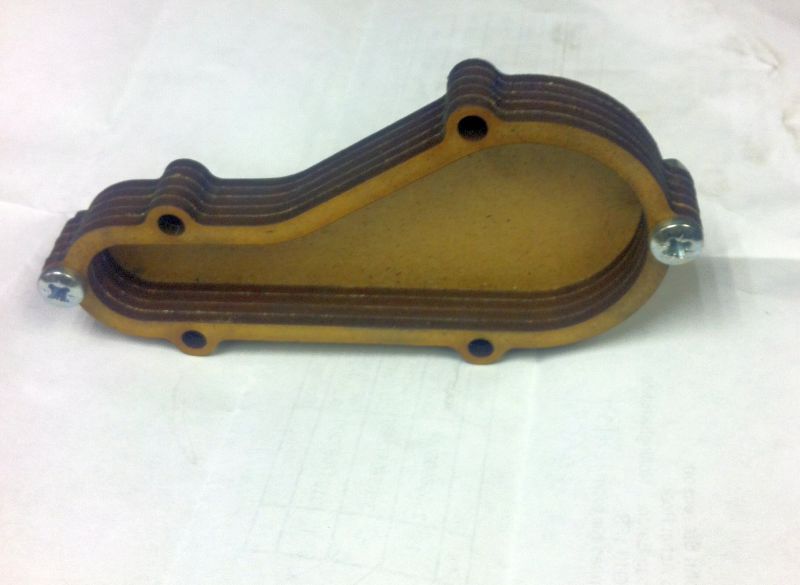
Assembled with M5 screws holding it together for the photo shoot, as an idea of size the small inner diameter is 20mm and the larger inner diameter is 40mm, bosses are 10mm.
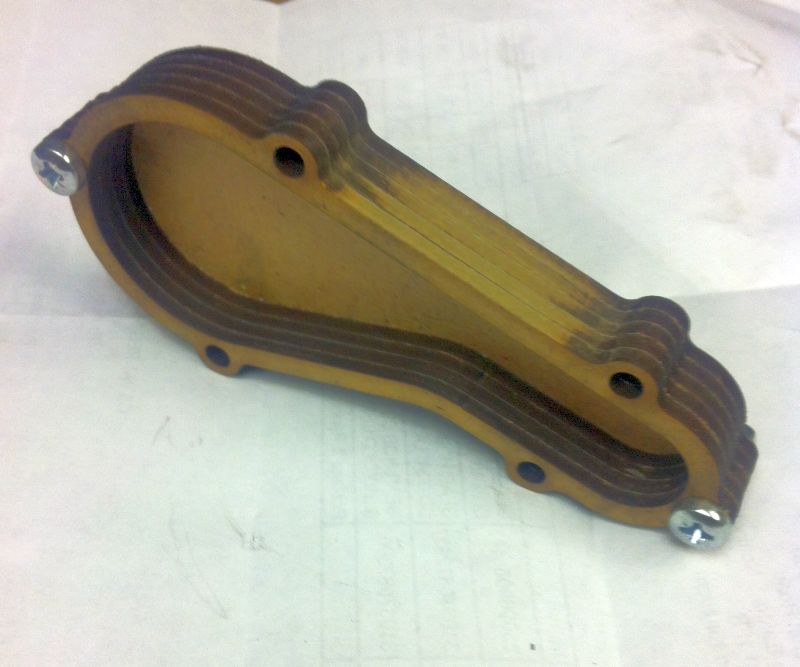
Angled shot of the same showing a bit of scrubbing with a strip of emery. If this was a genuine pattern each layer would be slightly larger than it's predecessor to give a draft angle.
It's a doddle to do this and also allow for shrinkage as it's all a question of scale in simple 2D CAD.
Simple job and not using draft angle it took 20 minutes from off the top of the head drawing to bolting the cut parts for the photo shoot.
Local foundry has seen the prototype patterns [ with draft angle ] and have OK them, they are also very, very interested in the process as this can knock literally days off conventional pattern making.
Roll on retirement < BG >