Hi everyone, long time no post.
Over the past year I've been working on transplanting a 2.5L V6 into my Mazda MX-5 (I'm a slow worker). I've just started to make a dry sump conversion for it and thought it might be of interest to a few of the members here.
On with the pics!
I started with this block of aluminium which I bought from a scrapyard for $15. I think it's 7075 or similar because of the dark corrosion on the surface and the fact it doesn't machine like regular aluminium, it's much, much harder.
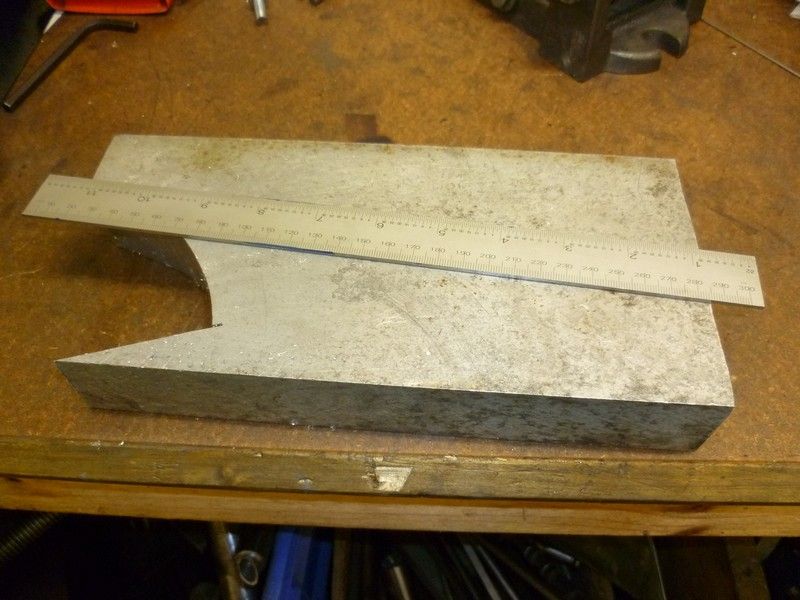
(the missing chunk was used for an oil filter relocation kit I made)
I made a model of the pump in CAD to check clearances and make sure everything would work properly. I'm using two sets of pump gears from a Holden 308 V8 engine.
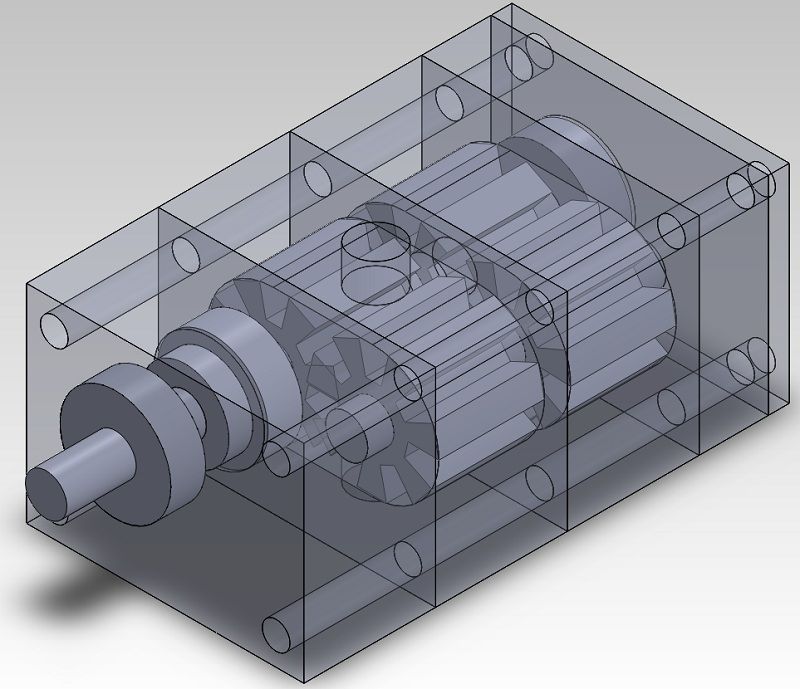
I then made a few drawings and cut the bigger piece roughly to size
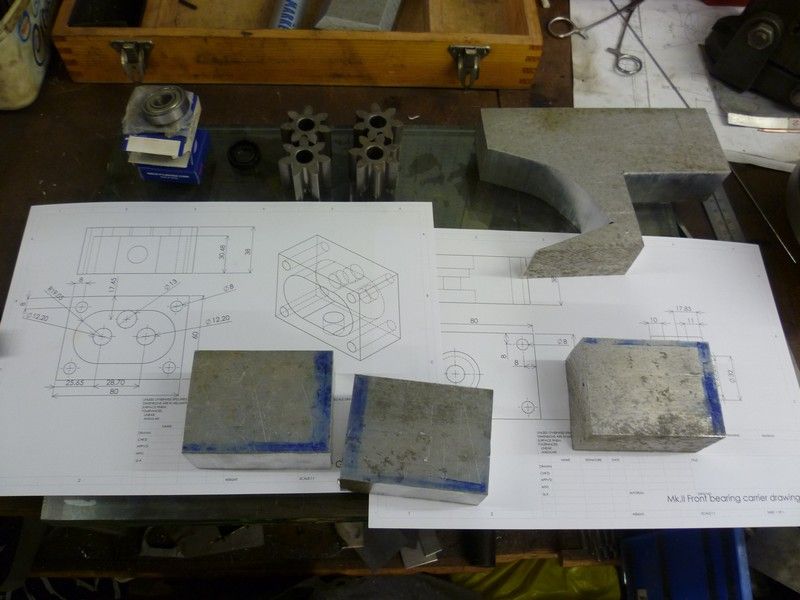
Initially I tried to square up the blocks on my mini-mill using this crazy shell mill cutter, but it didn't give a very good finish.
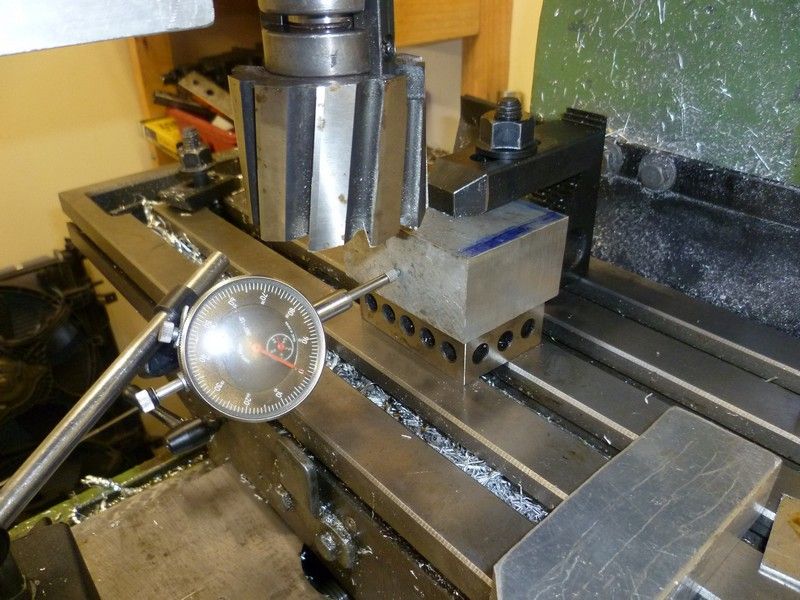
So I decided to dust off my least used machine and give it another try.
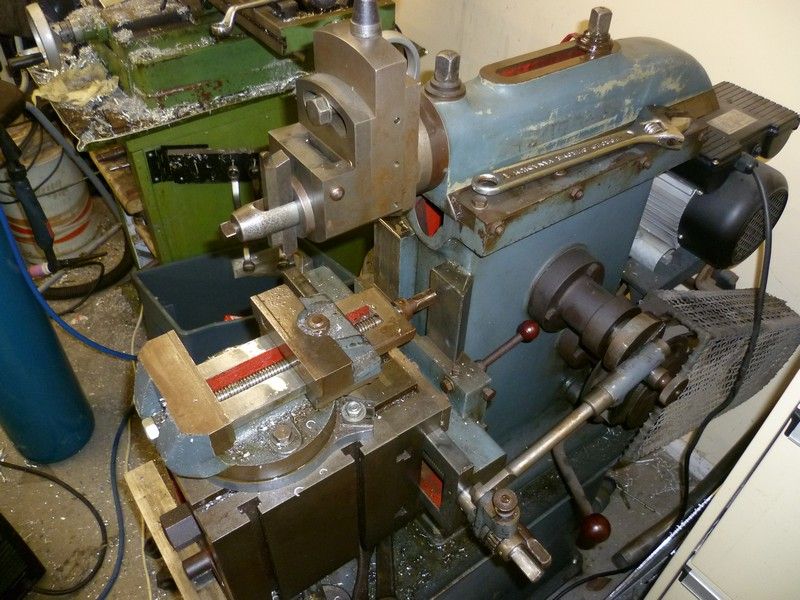
It's absolutely amazing, after a good solid hour of setting up and probably another couple watching it machine the blocks they're very square and with a very good surface finish (except the one done on the mill).
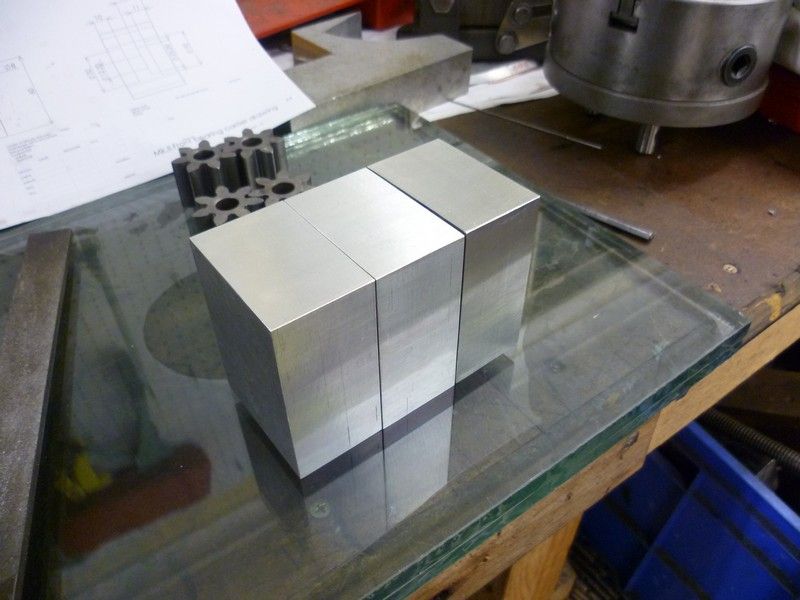
Tomorrow I'm going to try to make a jig to hold the blocks on the lathe for machining. It's critical the bores are exactly the same distance apart on both blocks. I might also try to cut the internal keyways for the gears while I've got the shaper working.
Comments, questions and (hopefully constructive) criticism welcome

Cheers,
Andrew