Right, this morning I had slept off the beer, so it's time to finish this chuck off

.
Here’s a Perris spindle. I have now fitted one in better condition, and the old one will save me making a dummy spindle nose. The first 0.375” is threaded ½” UNFis with a ½” register diameter 0.125” long. The overall length is around 5.25”/135mm, so it’s definitely miniature.
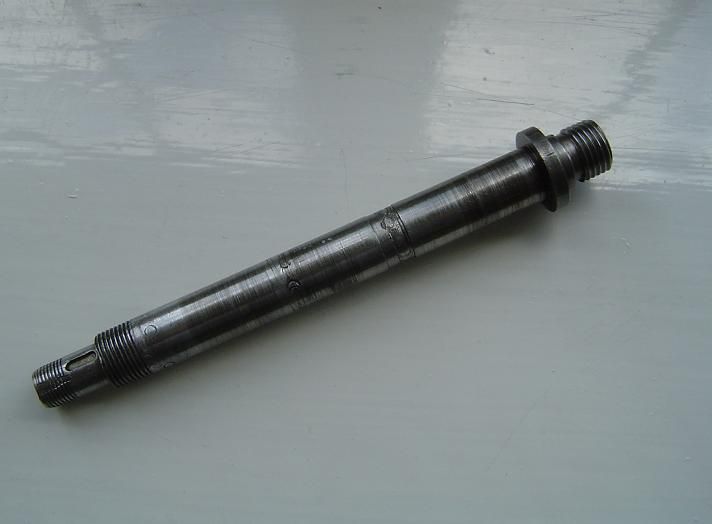
The 10.5mm hole in the bush needed boring out to 11.5mm, the minor diameter of the UNF thread. In a gesture towards concentricity, I assembled the little chuck with the bush Loctited in place, and gripped it on to a 12mm diameter silver steel (drill rod) bar which had been persuaded to run true. There it would remain until the boring and threading was done. The rough flange end was reduced with facing cuts to about 3mm thickness. With no boring tool small enough, I used one of the remaining good tips on a chipped 3/8” end mill, held at a slight angle to the lathe axis for clearance, and used the shank of an 11.5mm drill bit as a gauge. The micrometer showed the shank to be to be 0.07mm undersize, so after getting a tightish fit I took off 0.07mm more. Pics of that bit would be far too boring (sorry!).
I said in my last post that there would be a tricky bit: single-pointing the internal ½” UNF thread. It wasn’t practical to thin down the little threading tool holder I used earlier for the M17x1 thread; there would have been too little metal under the cross-hole.
A few days back, I spent what seemed like half a day pressing a 6mm tool blank against the grinding wheel to make this little threading tool.

Obviously, the tool lacks rigidity, but the thread is only about 0.6mm deep, so multiple light cuts wouldn’t take too long. A day or two ago, a trial run was made on a bit of bar, using a tap to finish off. After boring a ½” register just over 1/8” deep, the test piece was a nice fit both on the spare spindle and on the one in the lathe.
So, on to the real thing: my little chuck was still on the lathe ready for internal threading which went OK this time (phew!) followed by the tap which was supported by a tailstock centre to keep it in line.
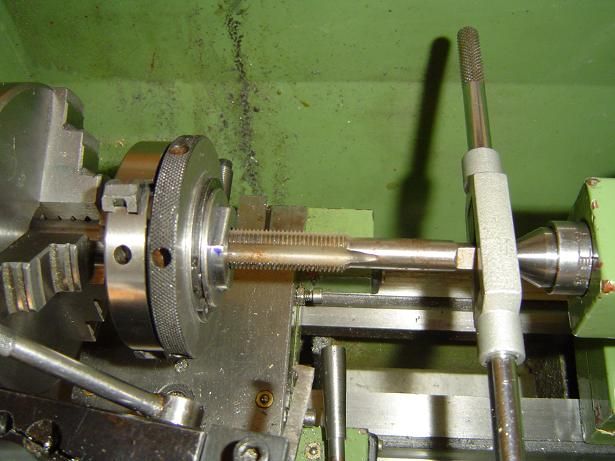
All that now remained was to bore out the outside end of the thread to fit the 0.500” register on my spare Perris spindle, and a bit of deburring.
So, to end this saga, here’s the baby chuck in place on the baby lathe.
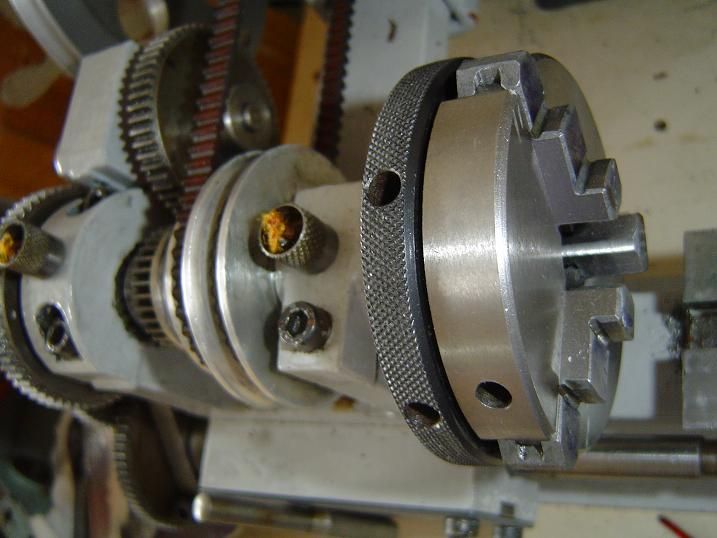
A quick trial holding a 12mm silver steel bar shows 0.004” TIR next to the chuck and the same at 2” out, which is reasonable for what it will be required to do. Other diameters may exhibit different TIRs, of course; I don’t expect wonders from what is just a cheap little Asian item.
If you have been, thanks for looking.
Andy
PS I might mention that a Madmodder in the US sent me a PM yesterday, offering me a very similar M12 x 1 chuck for the cost of the postage to the UK. The one I've been working on seems to have turned out OK, so maybe someone in greater need will end up with his. But it really was a very kind offer.