Four years ago, I bought a Chester Conquest lathe...... Cleared a little workbench space & made a few turnings.
It was so tiny & lightweight, compared with anything I had experience of!

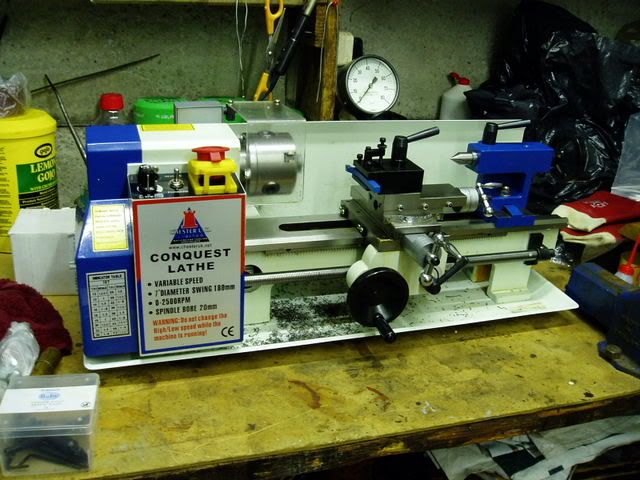
All ok, BUT.....

The hole for the toolpost screw had been tapped at an angle, so the toolpost would not sit down squarely.
I drilled out the 10mm threaded hole in 1/2mm increments to 10mm, then counterdrilled the underside 10.5mm x 5mm deep.
I then reduced the head of a 10mm caphead screw to a press fit in the recess.
This produced a nice rigid fitting, square toolpost!
The thing rocked on it`s rubber feet, so I made outrigger supports from 1" square tube.
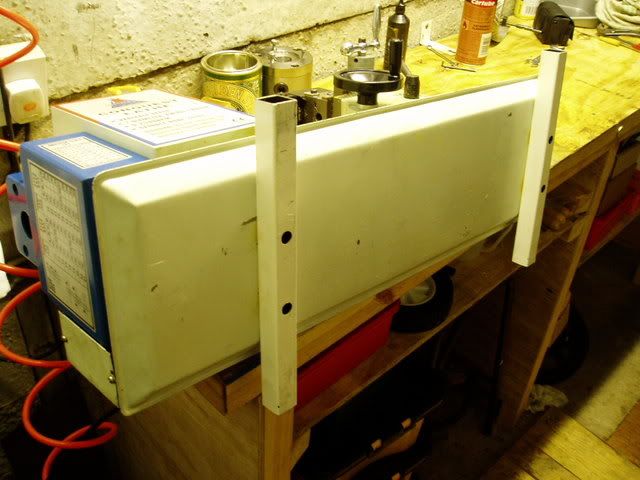
Also there was a rythmic
SKWARK! from the machine at increased revs... Polishing etc.
It sounded as though the leadscrew bearings were very dry. (They weren`t).....
I tried many times to cure the noise... But it could only be from inside the headstock.
Prompted by Boggy/ Darren`s posting, I finally bit the bullet & stripped it down the other day.
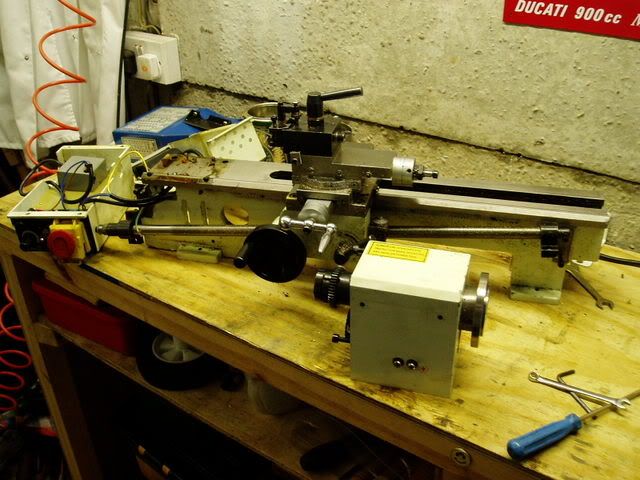
Headstock. Waxy dry grease.....
I sprayed liquid grease into the bearing recesses & waited for it to seep through to the outside of the bearings.
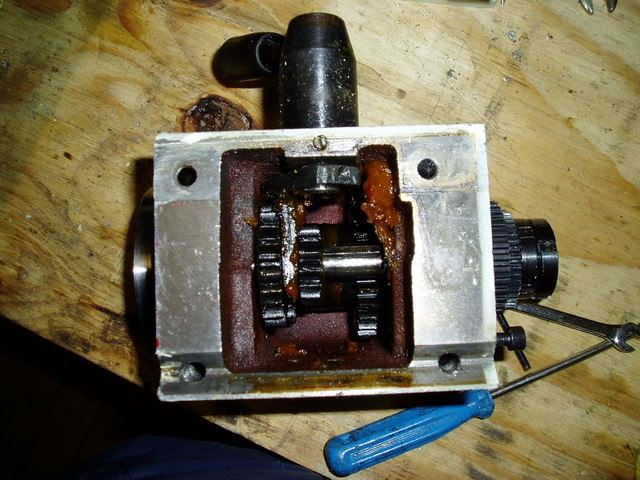
After 2 days, back together again, quiet, with no change in accuracy...... 1thou variation from chuck to tailstock!
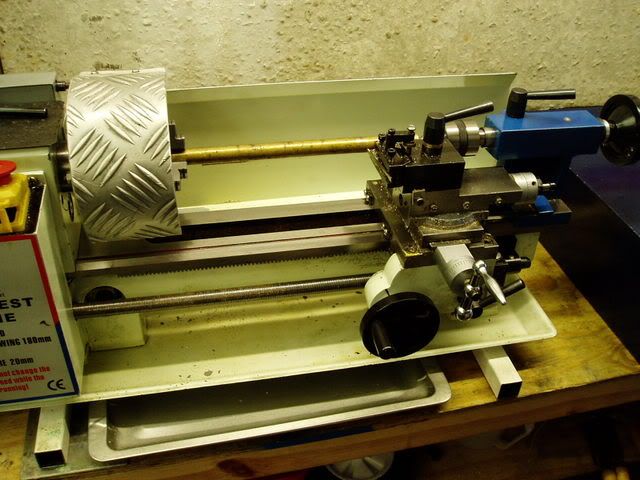
I`m a bit pleased...... Again!

David.