Hi all modders,
My next project was more an exercise to test my skills and the capability of my lathe. The First step was turning an exact replica of the register on the lathe spindle.
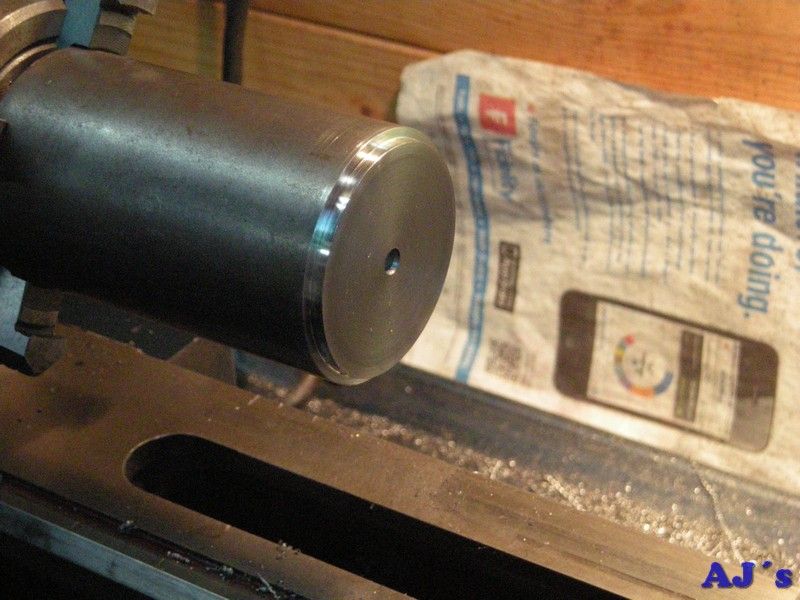
Facing and turning the female register in a 80mm dia. lump of steel.
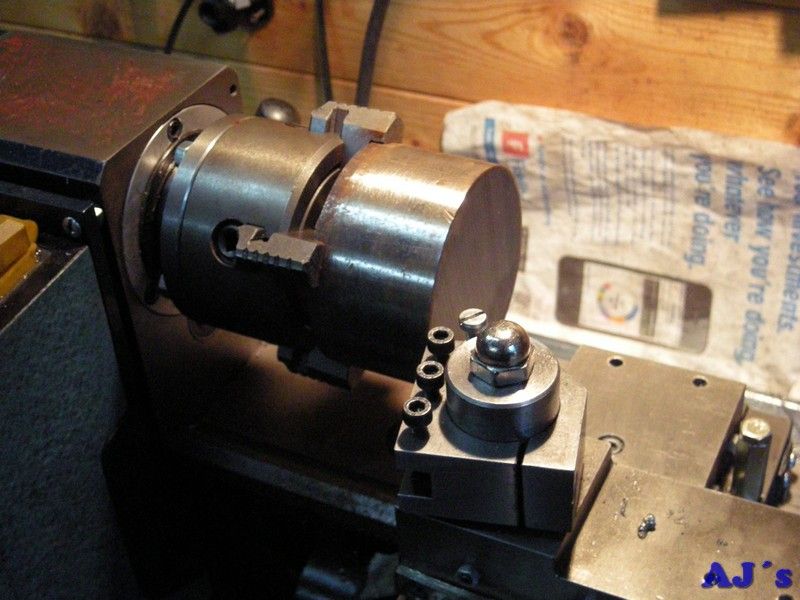
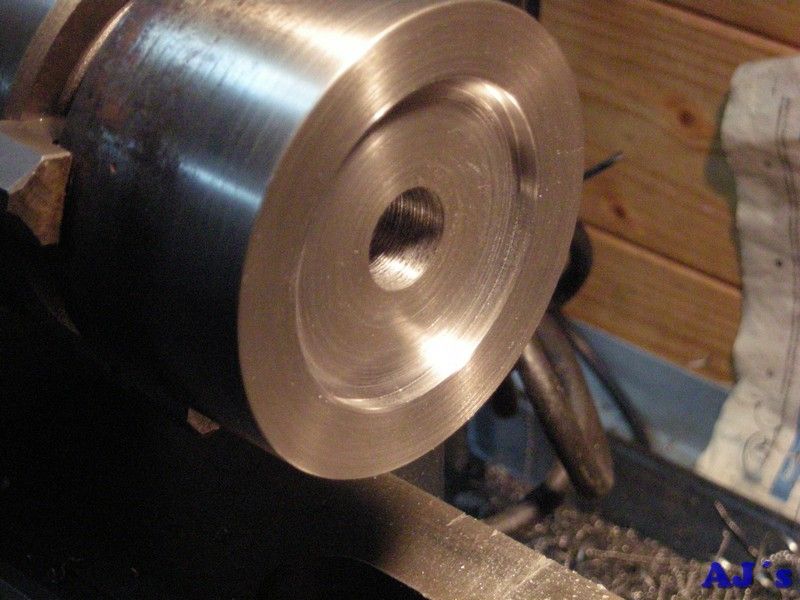
Testing the fit with the replica.
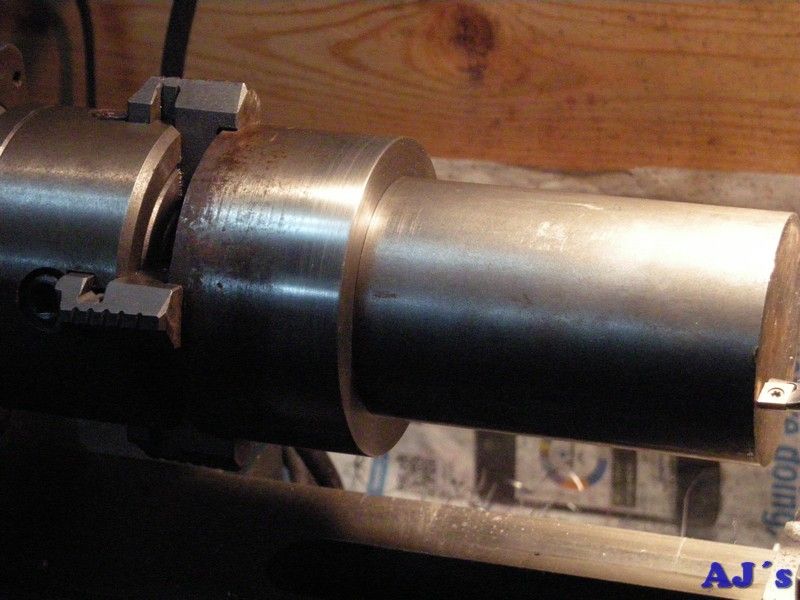
The lathe chuck was then removed without disturbing the work and put on the mill for drilling and tapping of the mounting holes.
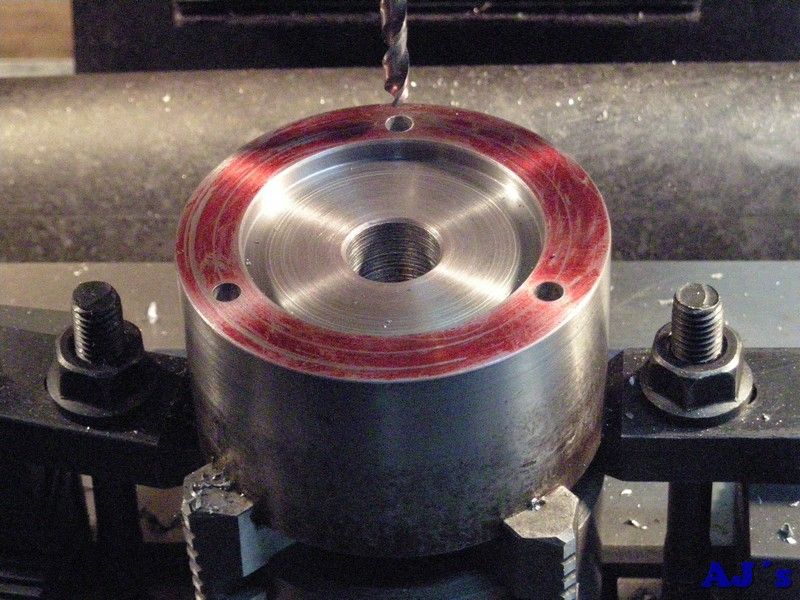
The new chuck was then bolted to the spindle, still mounted in the other chuck for in case adjustments were needed.
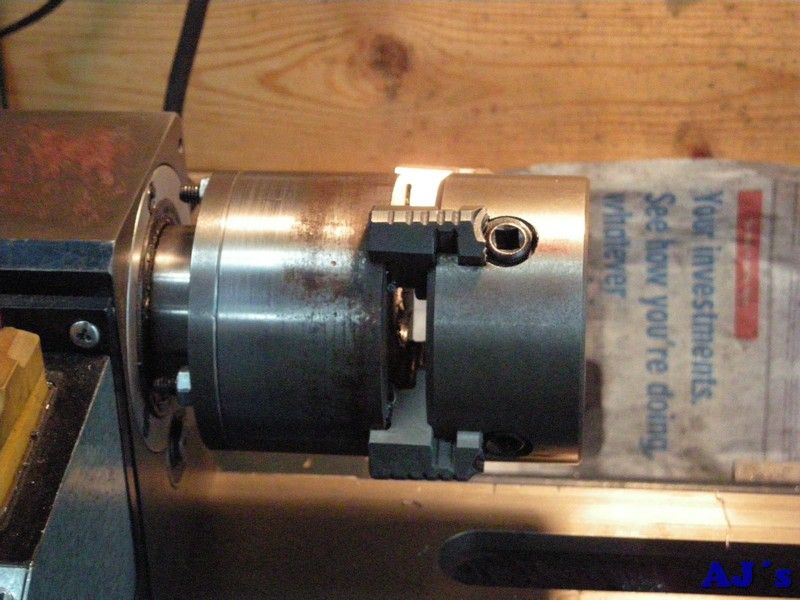
The slow process of turning down the front was done.
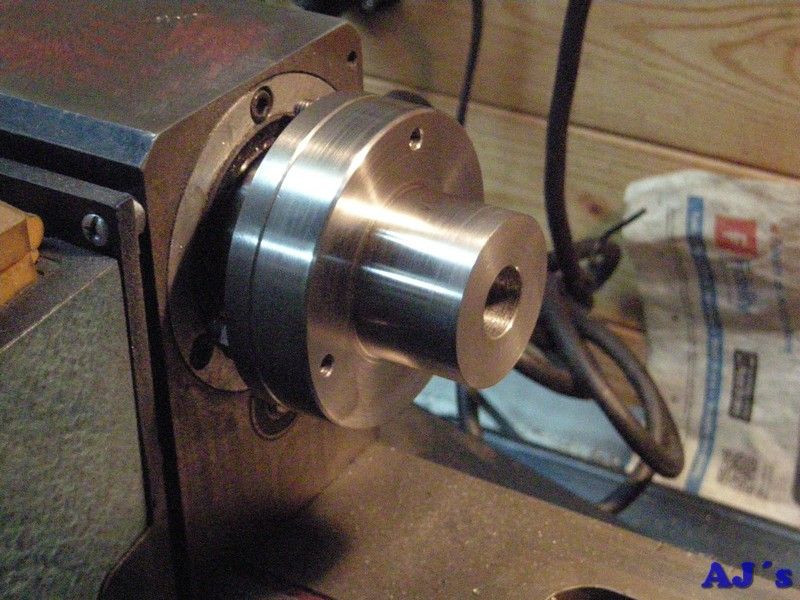
The thread section turned down with a relief groove at the end.
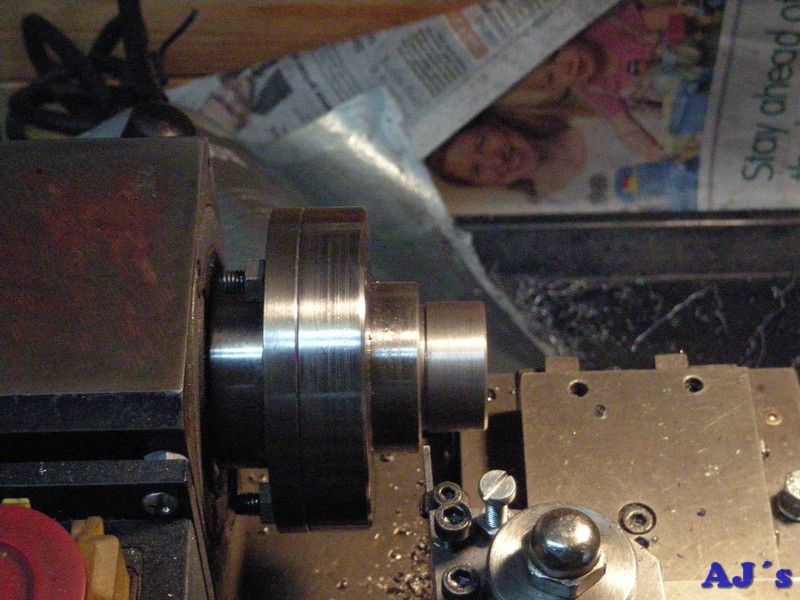
The finished thread.
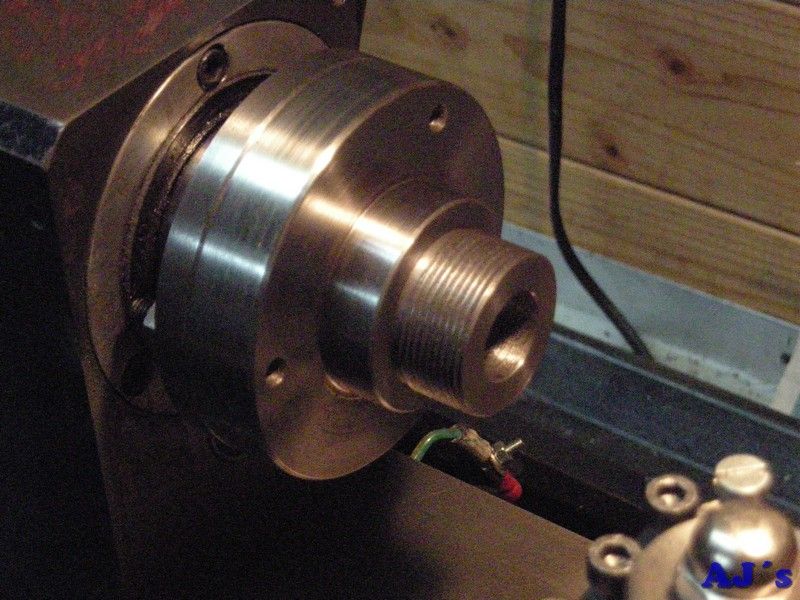
The compound was then set to 8 deg. And the inside turned. When it was close to size it was tested with mechanics blue on a collet with an end mill in it to keep it open.
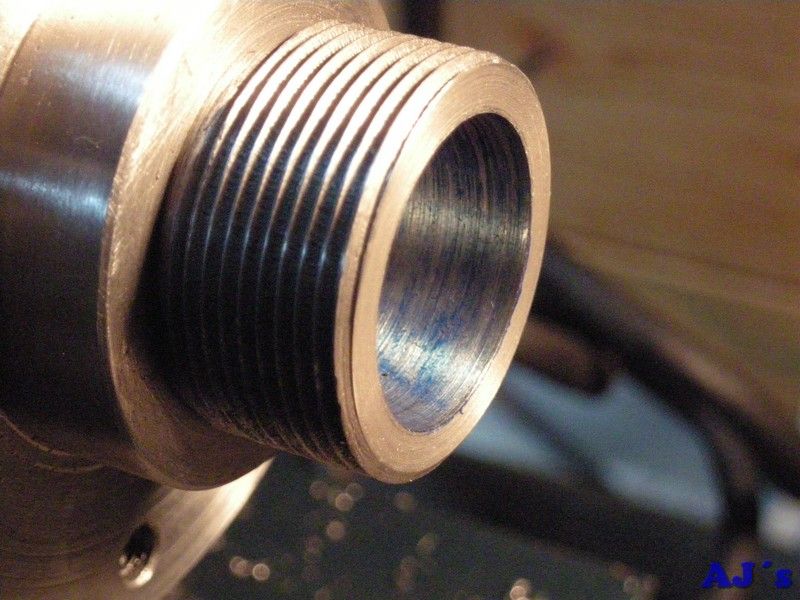
Turned out the angle was spot on and was finished to the correct depth.
A piece of bar was mounted and the run out tested, it was less than 0.01mm.
(Dial gauge was not zeroed)
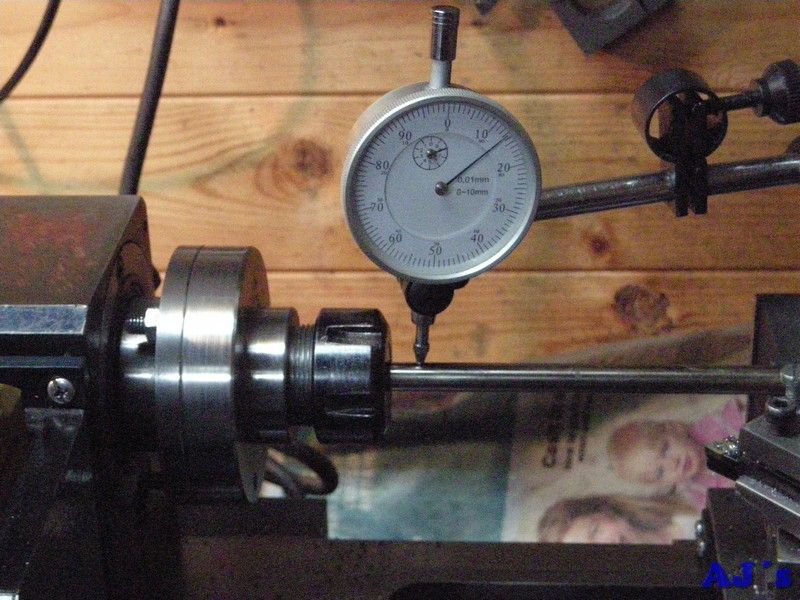
The chuck was marked for orientation when refitting.
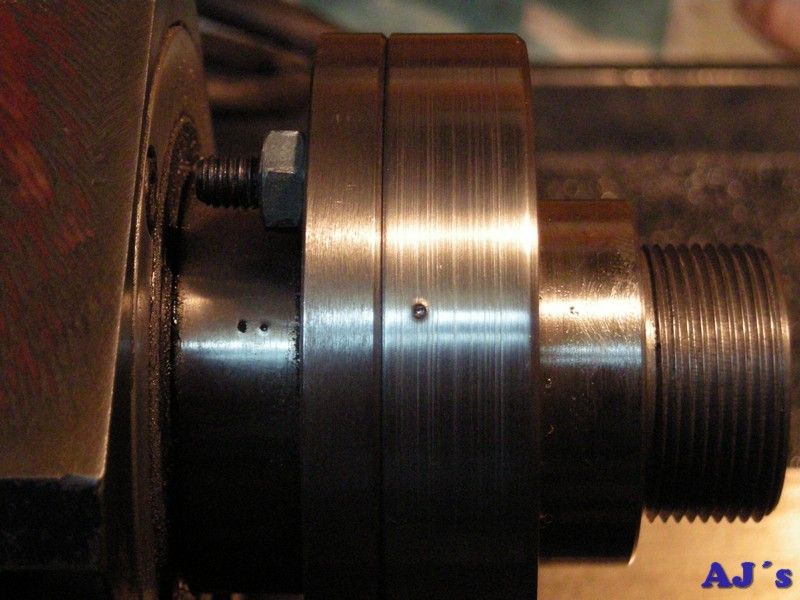
It was setup in the mill to drill a hole for a tommy bar.
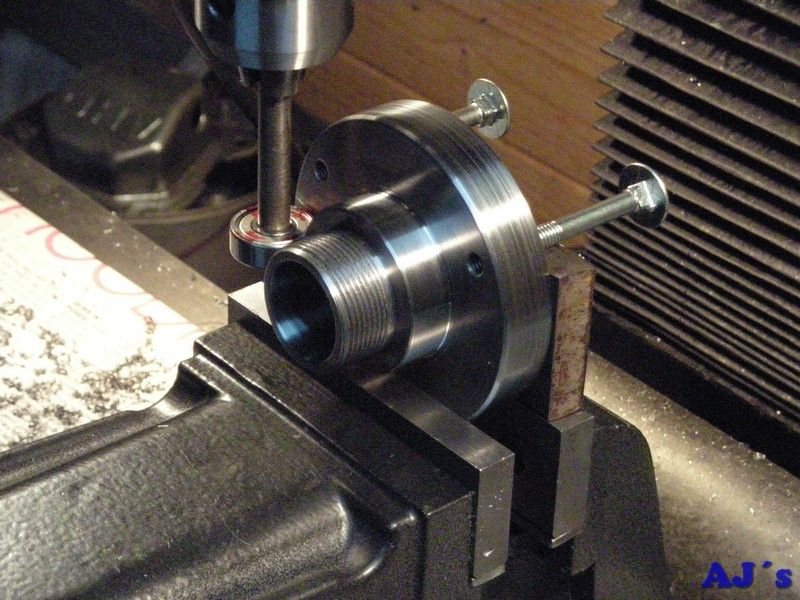
And all finished. I was quite happy with the result, and will be using it for my next project.
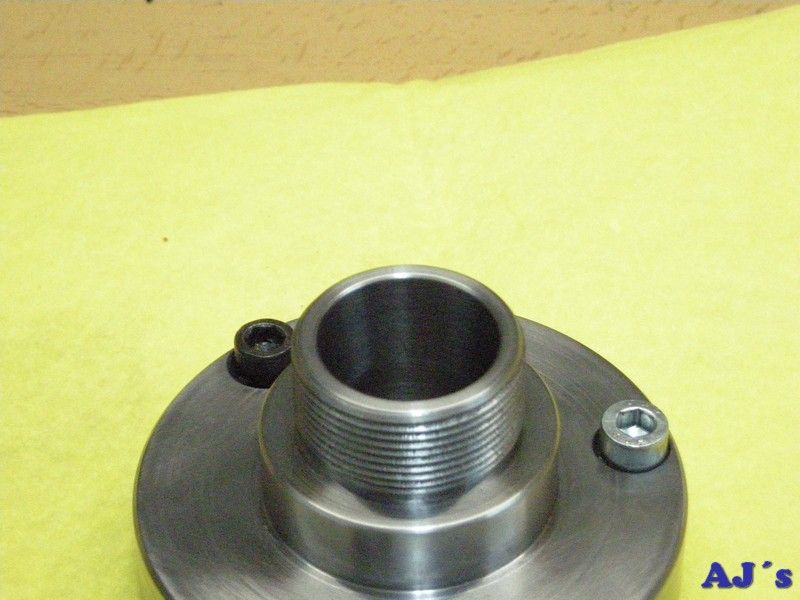
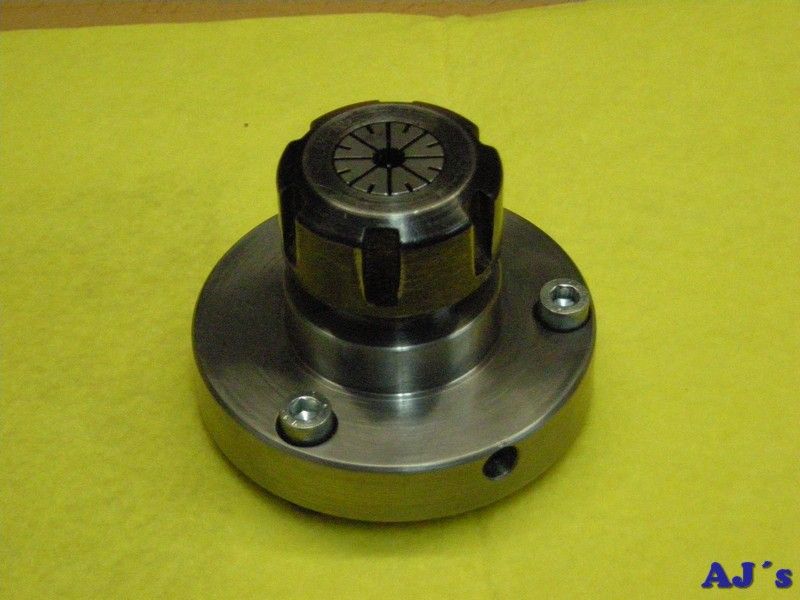
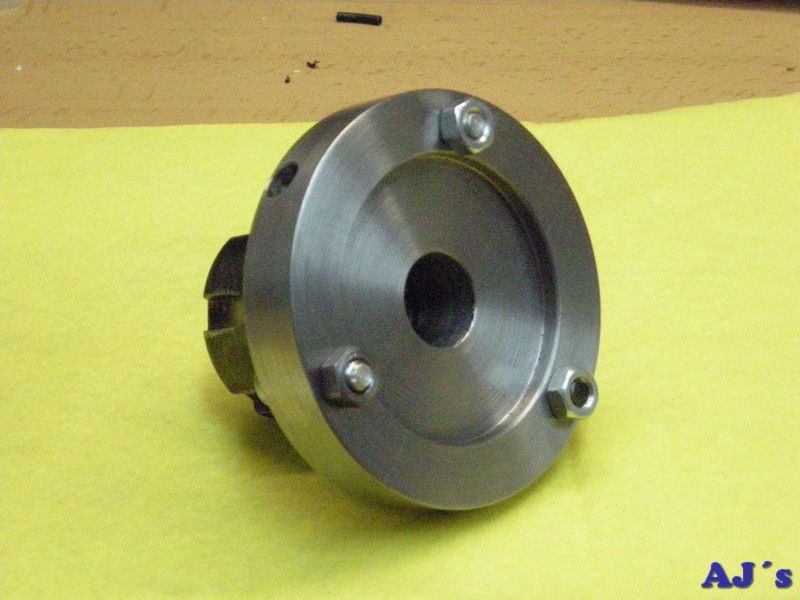
Cheers

Abraham