Hi Jonny, I knew the holes were for bars to go through the boxford shaper has the same type thing, I have never seen anyone use them mind, I will have to look for the M16 threaded hole , I can't say I have noticed it, I will have a look tomorrow. In the past I have moved the lathe as you say with crow bar in the end cut outs but not easy when things in the way at each end so hope the jack idea will be big improvement.
I have been distracted again , this time its linked to the lathe getting done, I have things lying about all over on trollies etc like chucks , rotary table , milling vices, dividing head etc and can't get moved for them. So after Rob Wilson kindly gave me some box section (

Cheers Rob ) I decided it was time to make a storage shelf unit to hopefully get all the heavy stuff kept in one place and take up less room, making doing the lathe a bit easier ( I hope )
The box section with end brackets from a previous life.
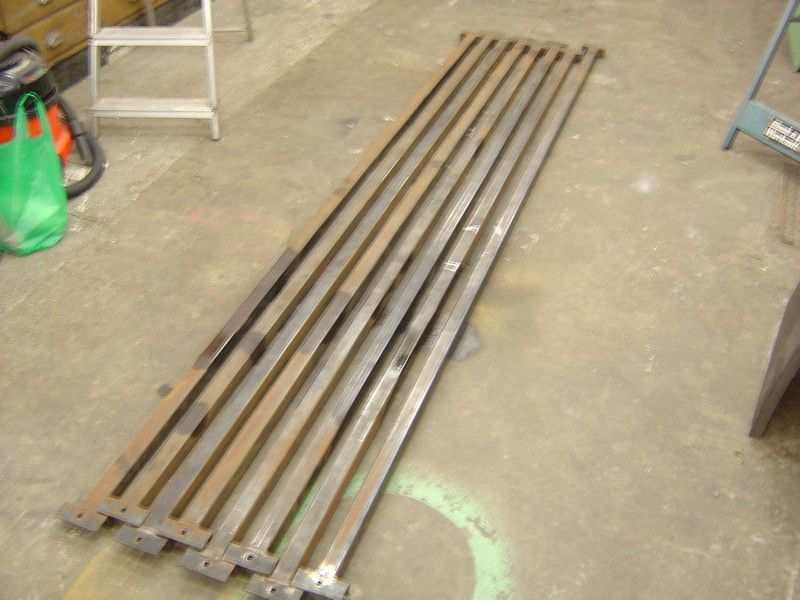
Cut up into bits to make the shelf unit.
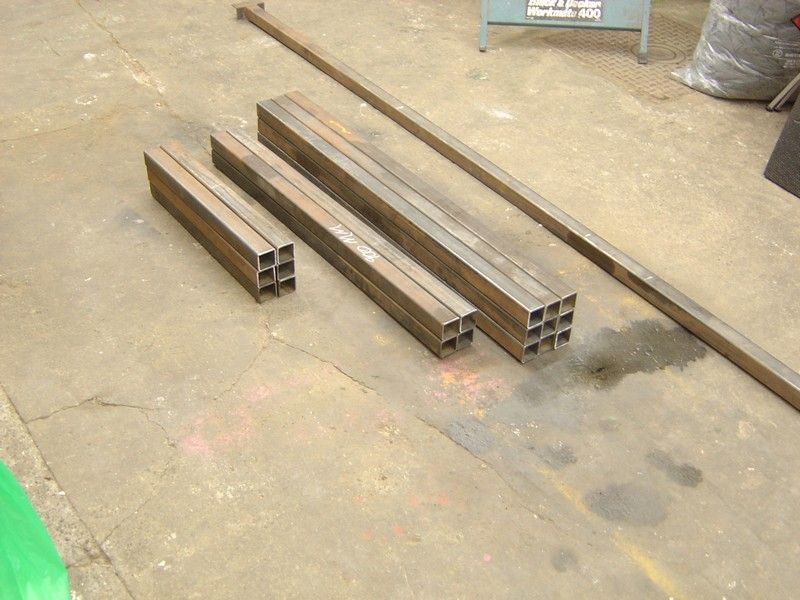
Laid out on top of life size drawing on the floor for tack welding.
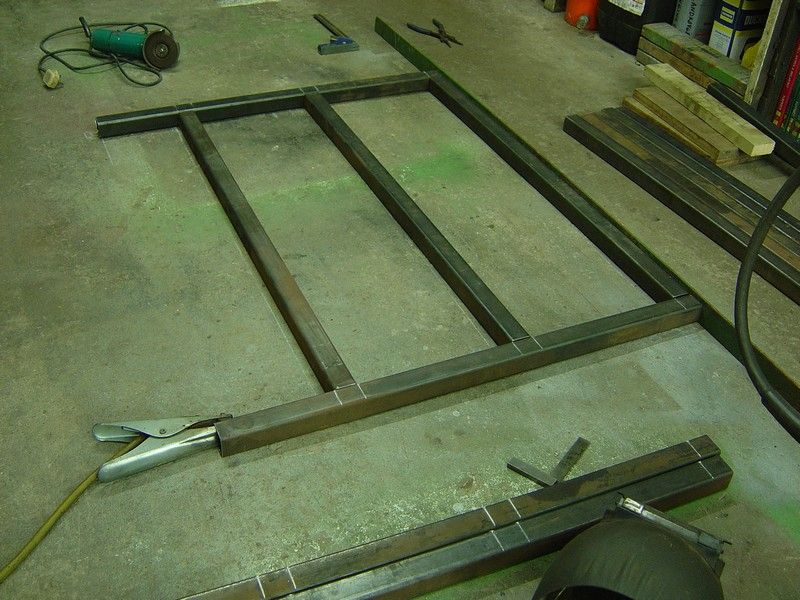
Starting to take shape, just tacking everything at this stage so it can be knocked into square.
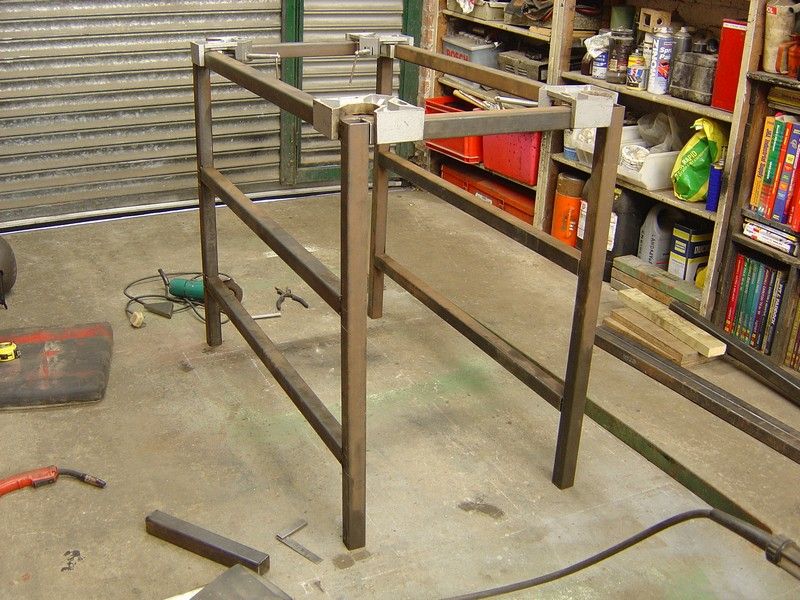
Main frame square and tack welded , just the middle shelf supports and the height adjustable feet to do.
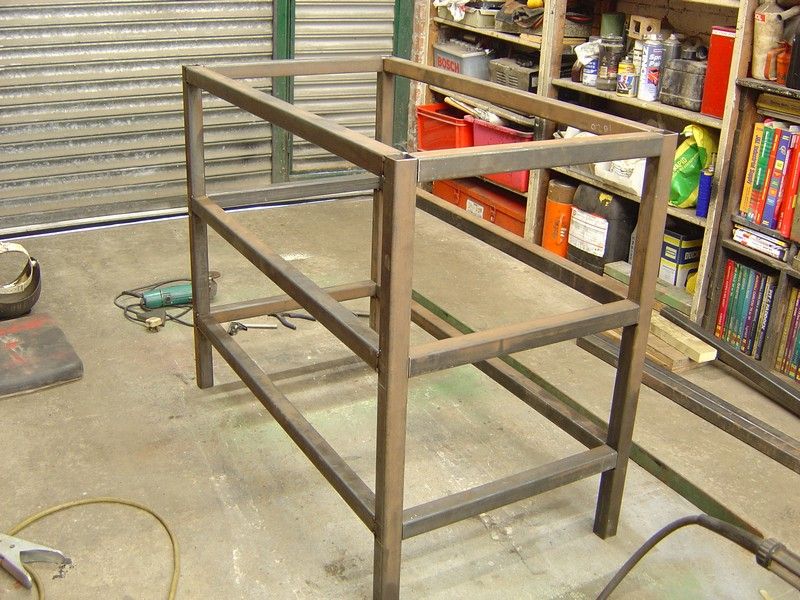
The floor is miles from level where the shelf unit will be positioned so I am welding some big nuts into the leg bottoms and the matching blots will act as levelling jacks, tacked into place in this shot, then welded all around.
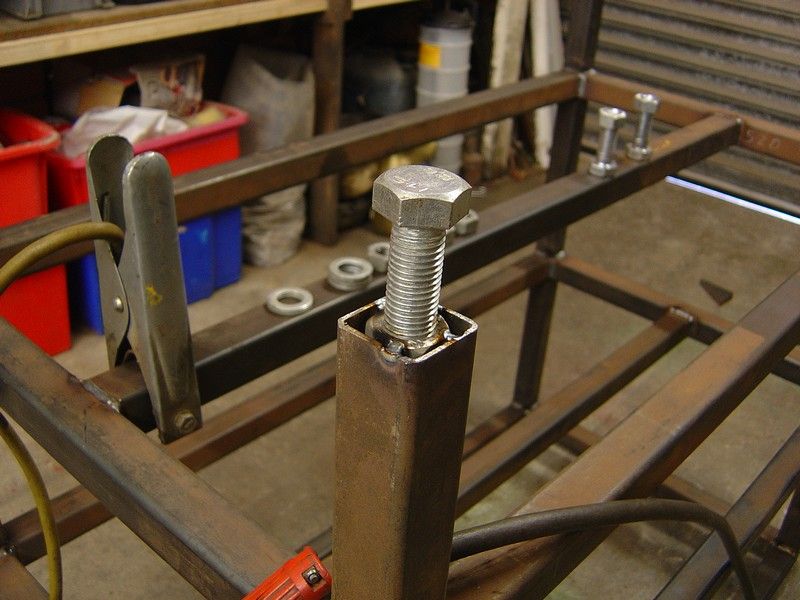
This is the bottom of a leg once welded up , works great for unlevel floors and cheap to do

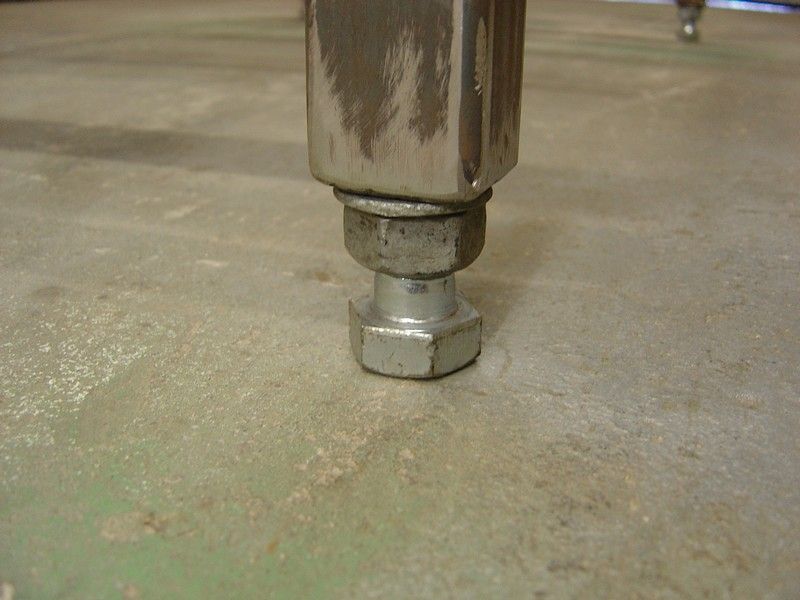
The finished frame sitting on its adjustable feet. Every joint is fully seam welded lol , just like the good old days

, I like things I make to last

, unlike most things you can buy these days , one tack weld and an M6 bolt each shelf so the first time you move or load it up it disintegrates

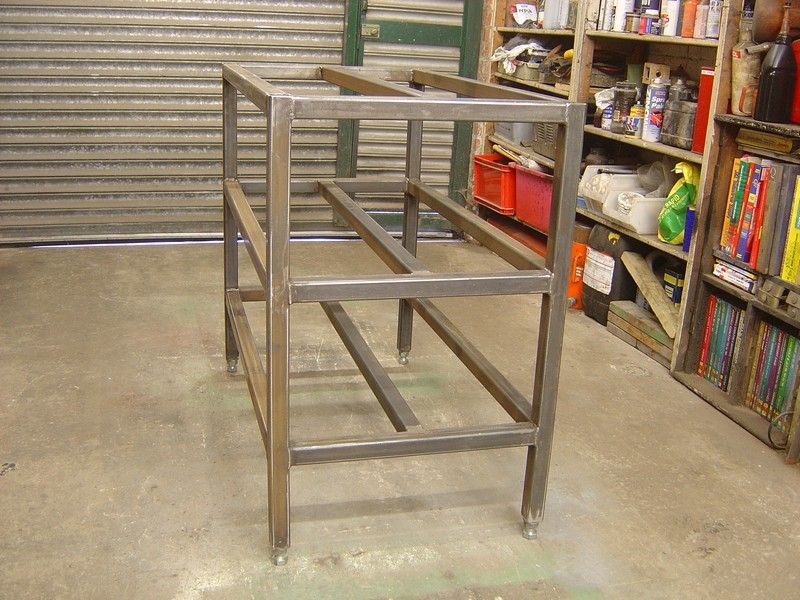
Primed up with etch primer, I find the small size paint rollers ( 1 inch diameter, 4 inch long , cotton type , used for household decorating ) work best for this sort of frame, brushing is hard work and leaves rough finish and spraying wastes loads of paint and also covers everything in 3 foot radius of the frame with paint

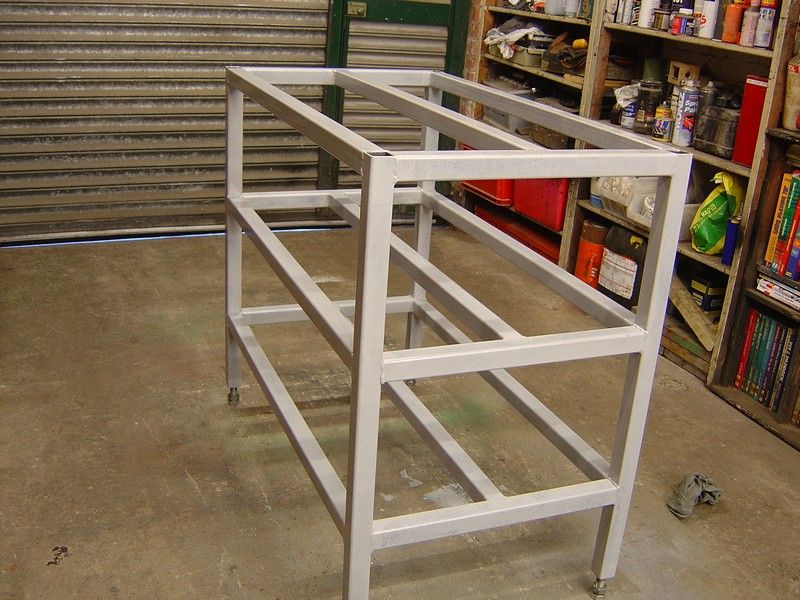
I will paint it the usual RAL6011 Machinery green

tomorrow and fit some 3/4 plywood shelf tops, then try to fit everything on it

, I hope it will all fit

Cheers Mick.