Well at last some real progress on the lathe.
From looking pretty much stripped right down again.
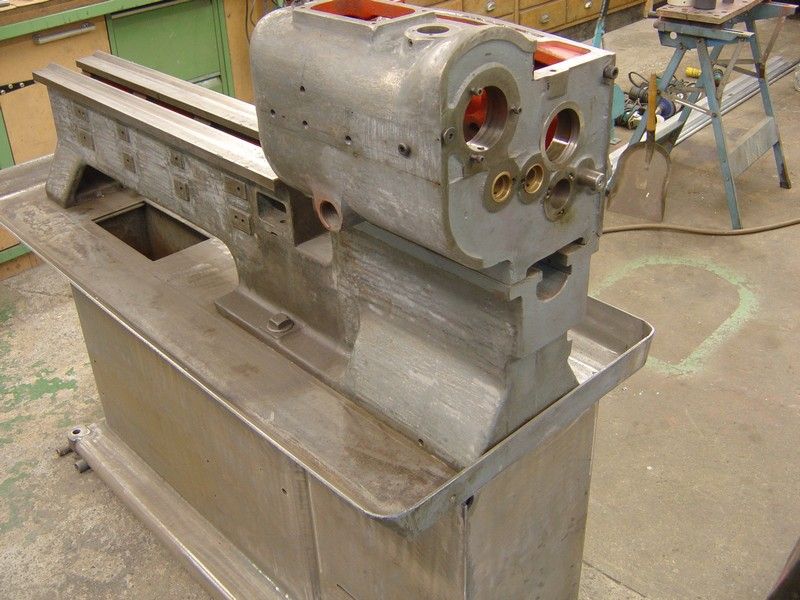
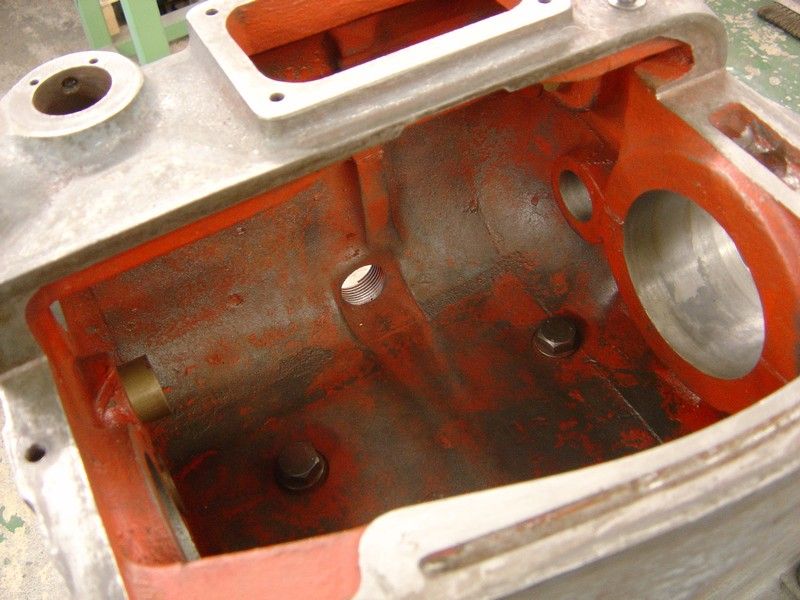
The mission was to get this lot back inside the headstock
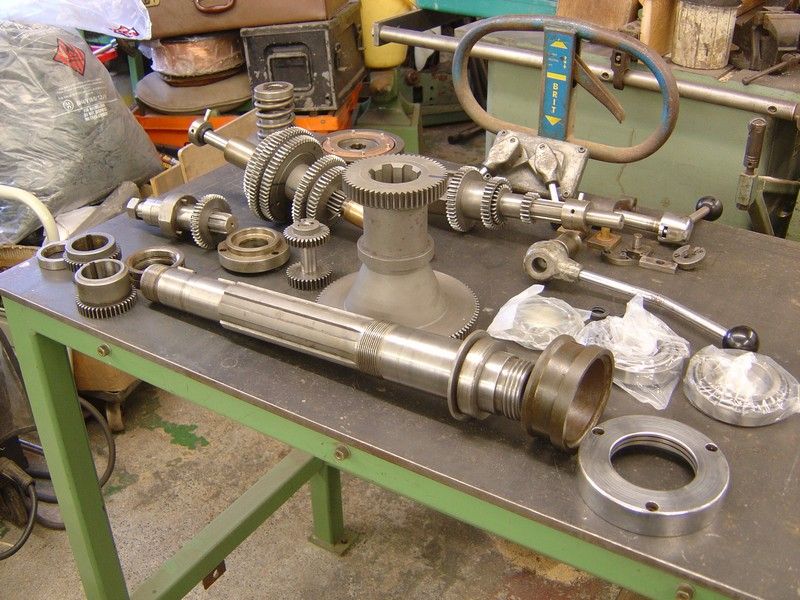
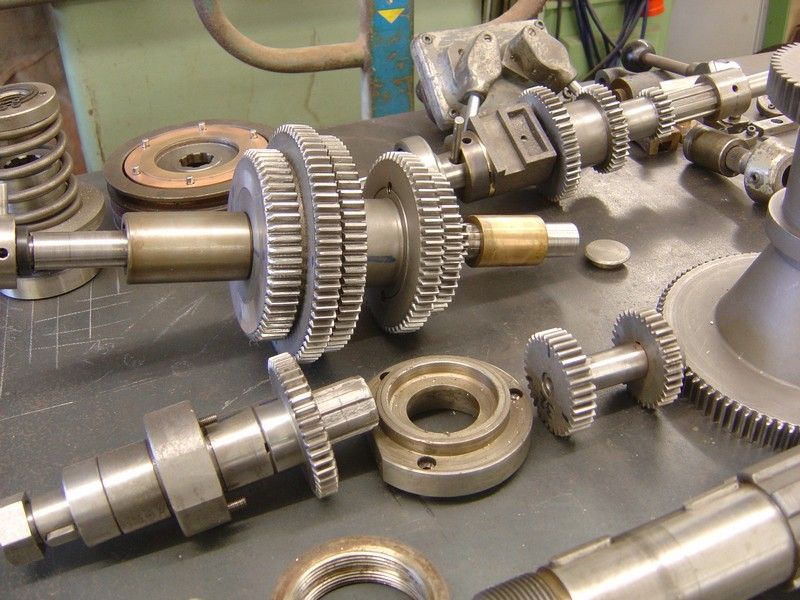
All the gears have been de burred, new spindle bearings and new oil seals, a couple of gears that had chipped teeth replaced and everything cleaned and checked over. The main problem with getting all the parts in seems to be most bits have to be inside the casing in their rough position but not actually in position and held there so that other things can be lined up at the same time, its a good job I had took plenty photos as my two manuals both have drawings that show several things that are not as this actual lathe so can do as much harm as help sometimes. Anyway after much struggling and trial and error , it all went back together and gears select and turn ok.
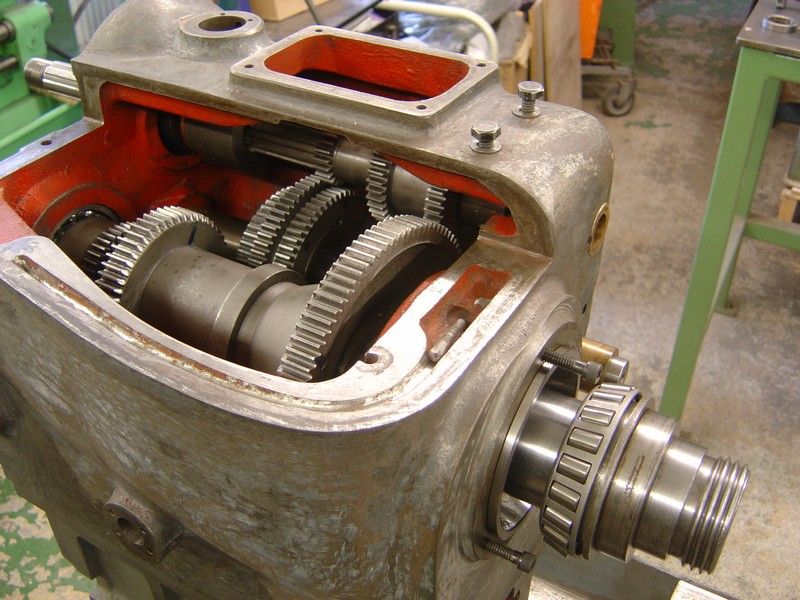
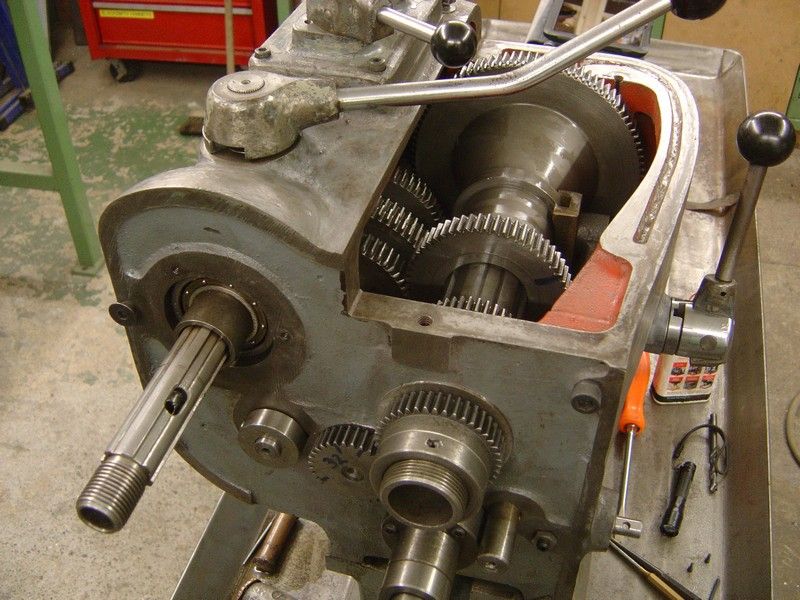
The next bit was the clutch , before the clutch used to snatch and sometimes not disengage, this was due to the pins in the vee pully that the clutch plate slide on having had notches worn into them and the clutch plates holes being worn oval. I was not confident of replacing the pins and drilling the plates spot on myself but Rob Wilson kindly did them for me , as you would expect Rob, he did a cracking job of them, cheers again Rob . You can see the pins in this photo, they have been fitted with slightly larger diameter roller bearing pins.
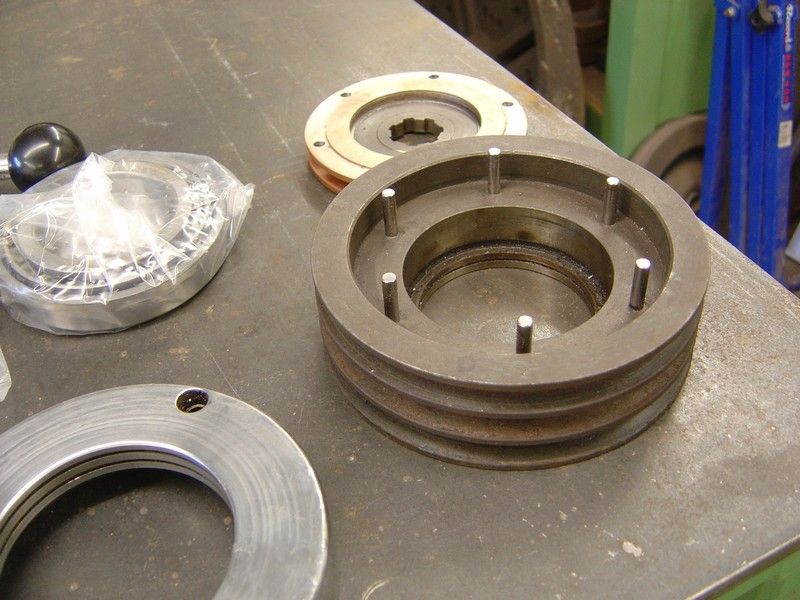
These are the plates with the new slightly larger holes drilled to match the new pins.
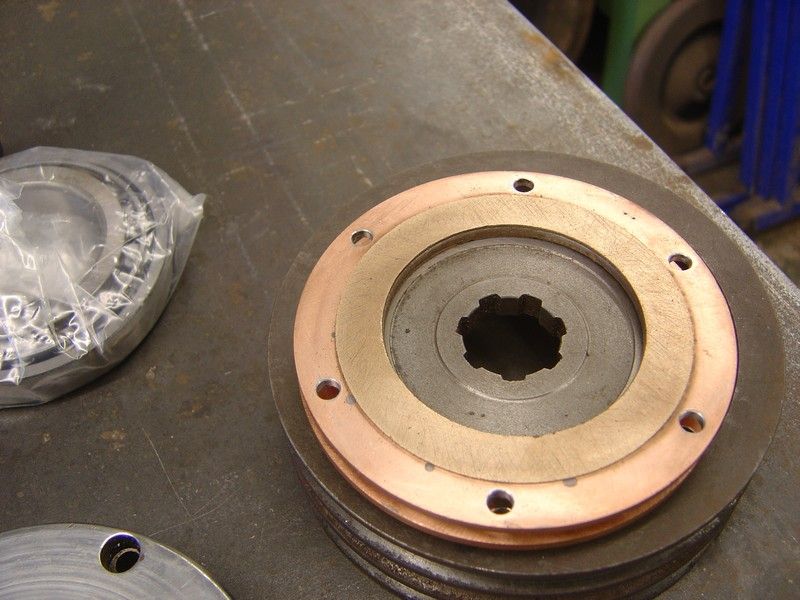
The clutch was then assembled, both the drawings were wrong and I could not remember at all how things went ! good job I had marked things as they came off, everything facing outwards received two small dot punch marks as you can see on second photo down at 12 O'clock , the steel clutch disc is flat one side and had a raised center on the other side as seen in third photo, it would have fit on either way but one way would be the wrong way , these marks ensured I put it in the correct way around so well worth taking the time to do this.
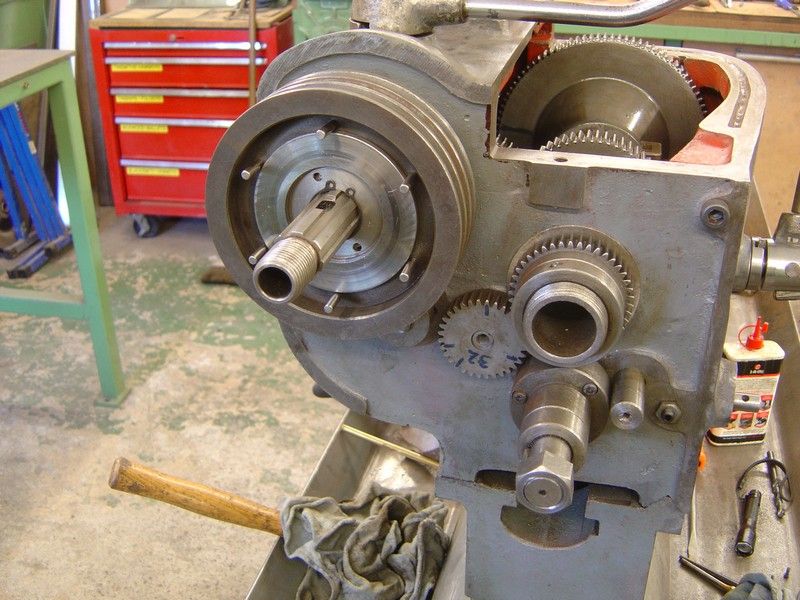
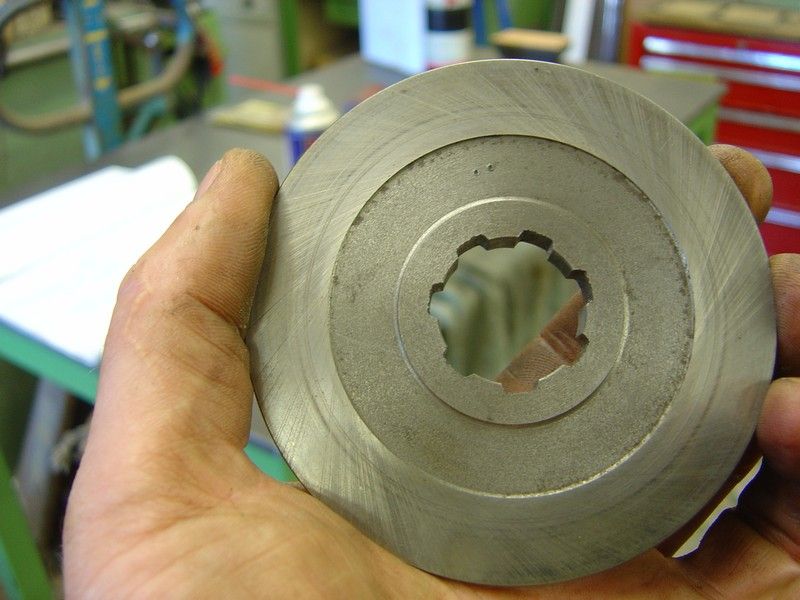
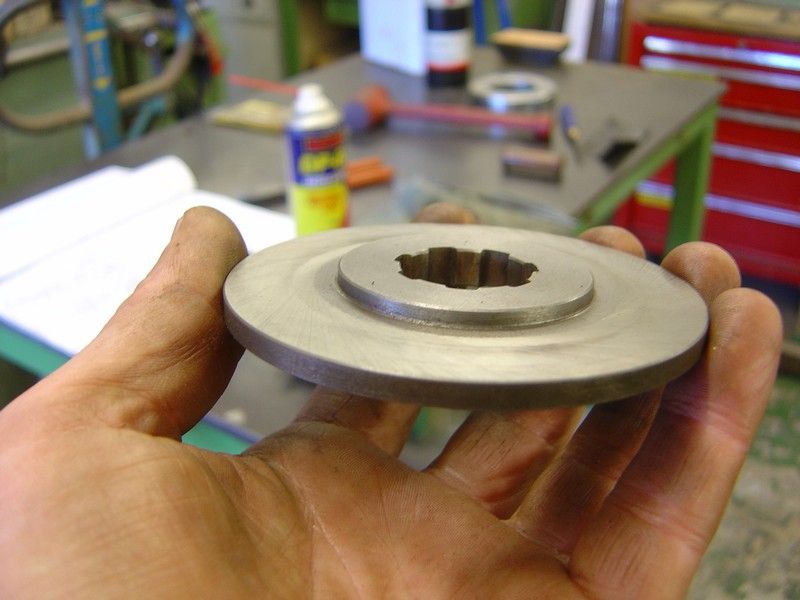
The next thing was a threaded collar on the end of the spindle has the holes chewed up so I drilled some new holes in the collar on the mill, lucky I already had the vee block and angle plate set up from doing something else on the mill as it would have taken longer to set up than do the holes.
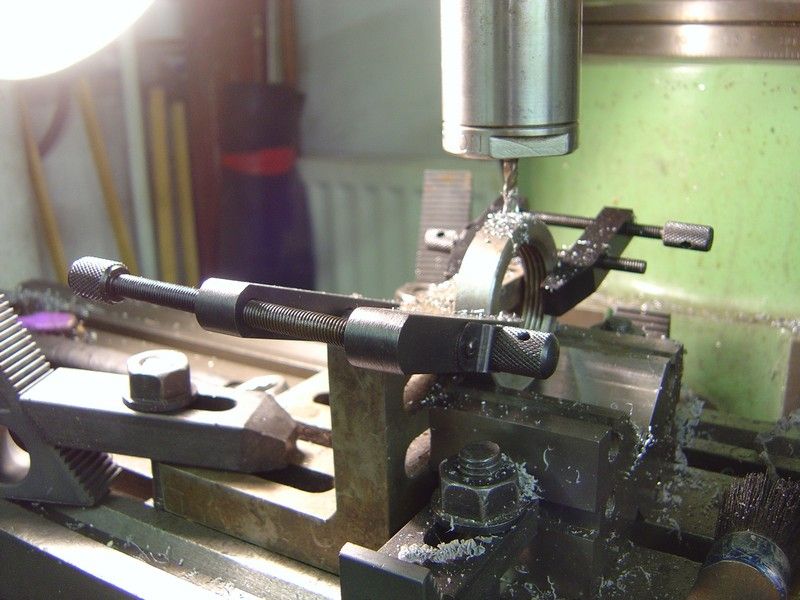
This is the collar back on the spindle.
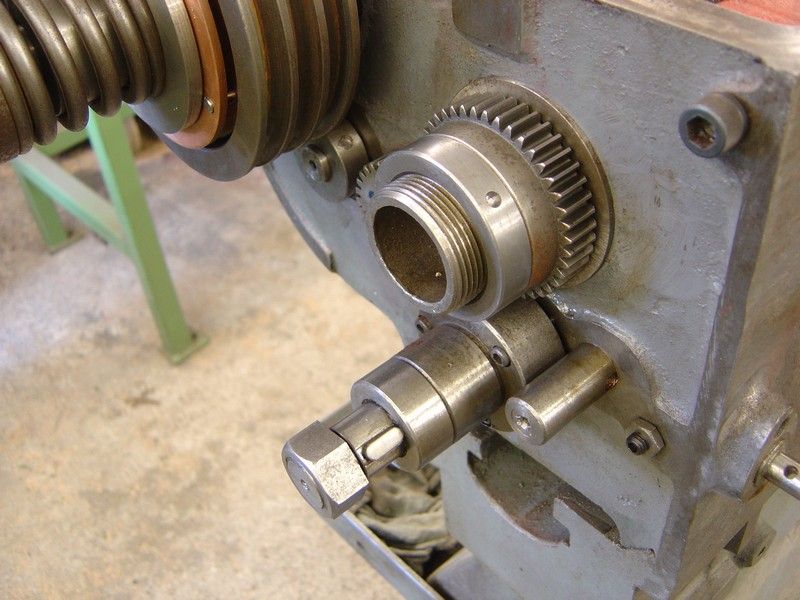
The clutch was then trial and error assembled, but would not seem to work, after looking at it really carefully I noticed witness marks inside an adjustable collar and remembered that I had put a small pin in a separate place in case it got lost , this was the missing link and once fitted it all seems to work ok.
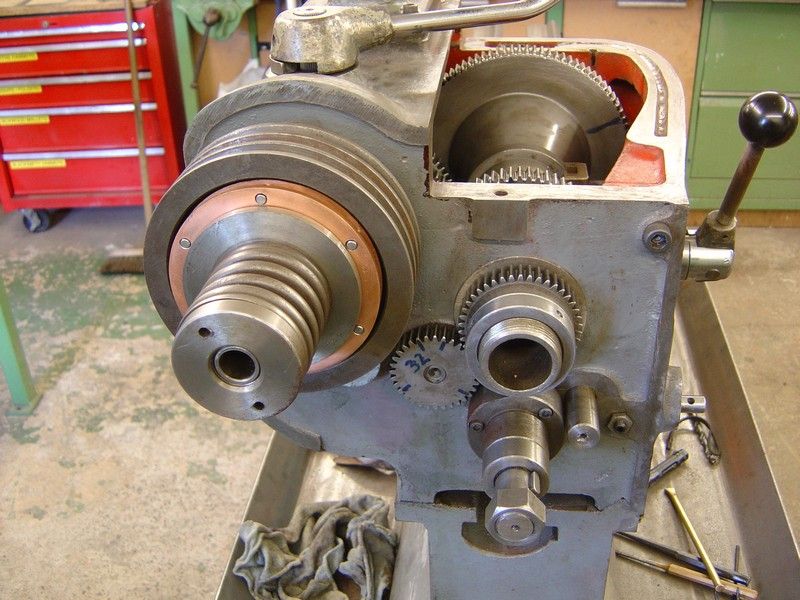
The next stage is to prepare things for painting , a good bit of sanding , filling and priming needed, at least things should look as if they are progressing once some paint goes on.
Cheers Mick.