Ok folks, if you can stand another thread on building a Stuart 10v... here goes. This may take a little while as time, energy and temperature allow me out in the workshop.
Also I afraid I didn't take any picture when I started.

I initially started machining using the Andrew Smith / Pengwern book Building a Vertical Steam Engine, but after Harold Hall published his series in Model Engineer I have started using some of his methods, I will mix and match as time goes on and no doubt improvise as I learn more.
First job was the boxbed, after measuring up I had 2.5mm to take off in total to get the height down to the 28mm specified, so that's errr 1.25mm per face. A quick clean up with a file to remove any flash and I mounted it up in the four jaw chuck to face the underside. So that's the first challenge.. how much to take off in the first cut? Every thing I've read about machining castings says to make sure your first cut takes of the hard surface. How deeps that then? In the end I took off 0.5mm using the slowest speed on my lathe (170 rpm). That seemed to work ok, so I flipped the boxbed over in the chuck and did the same the other side. First bit complete

On to the sole plate. This one caused me a bit more thought. Stuart castings don't have a lot of excess meat on them, when I measure up I only had just over 1mm to take off, and that I decided I need to take off the top face to give me the correct dimension from the bearing centre line to the top face. So I filed and lapped the bottom flat on my granite chopping board, sorry surface plate( I think its quite good that Tescos have started doing engineering supplies

) I then milled the top face down using my mill. I've still to drill the holes and open up the slot for the bearings.
Next I decide to tackle the standard, First off the feet exactly as per the book, using the 3 jaw chuck and a centre running on a plug in the bore. Its at this point I started using Harold Hall's method and made up a jig /fixture to drill the feet and then mount it on my homemade face plate
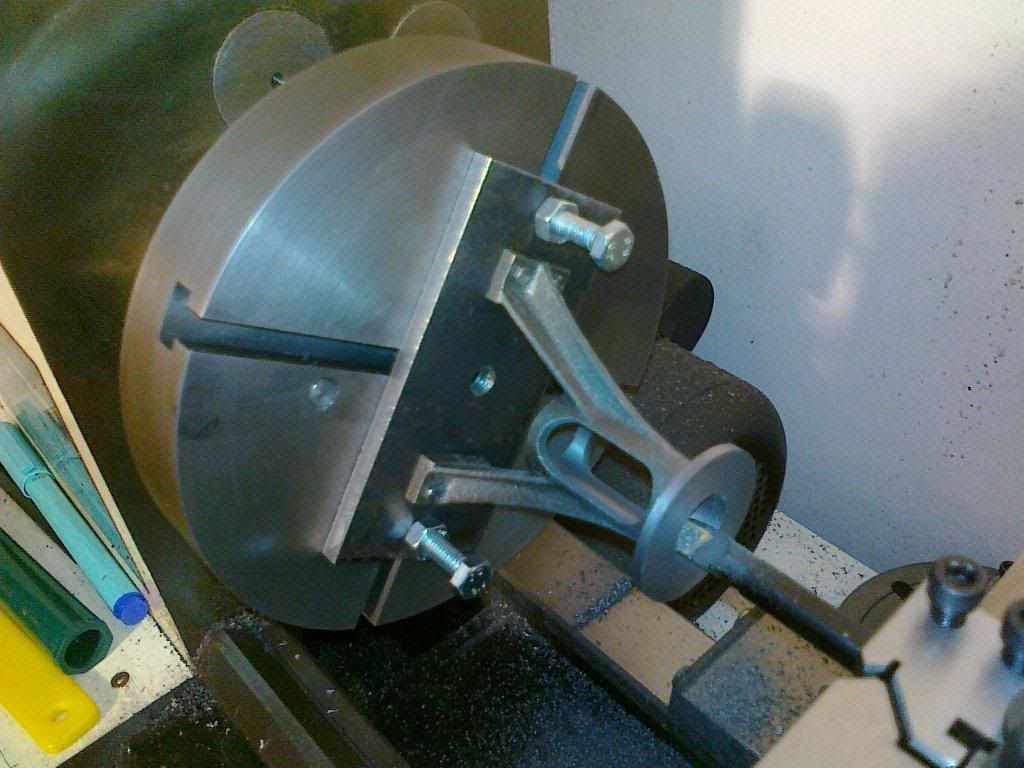
(sorry about the ropey photo there it was taken with my phone)
So progress up to now is
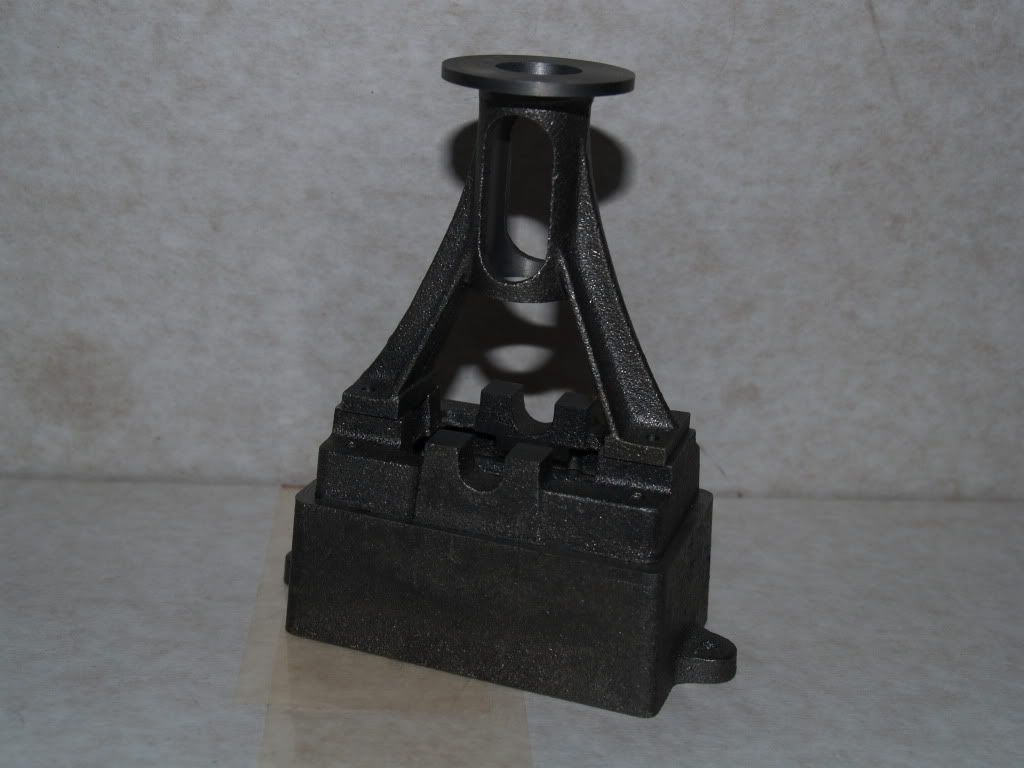
I'm starting on the cylinder next, once my workshop has warmed up. The 300w security lamp/heater is struggling at the moment though.
Any thoughts or comments so far are welcome.
mark