Lots of info. Letting them settling into my head. May need some files to thin the outer shell for more to pass through...
Andy, the gap between the spindle end and the cover is rather small. I think I can file the plastic thing (any name for this protruding circular thing with a hole in it?) shorter to make more space for a thicker bolt head.
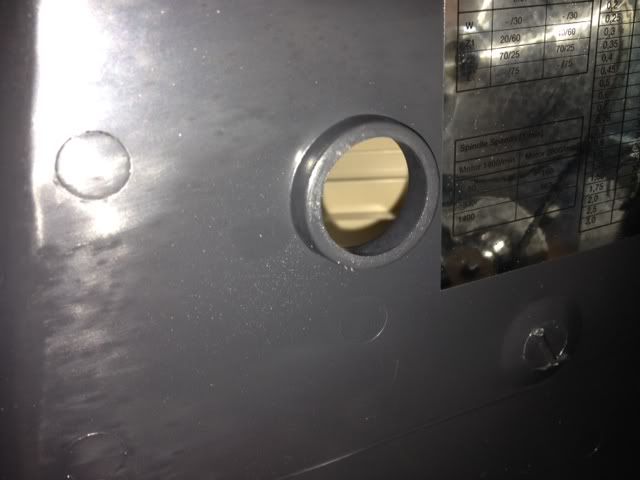
I believe the bolt head can bear against the end of the spindle though it only measures about 1.5mm in thickness?
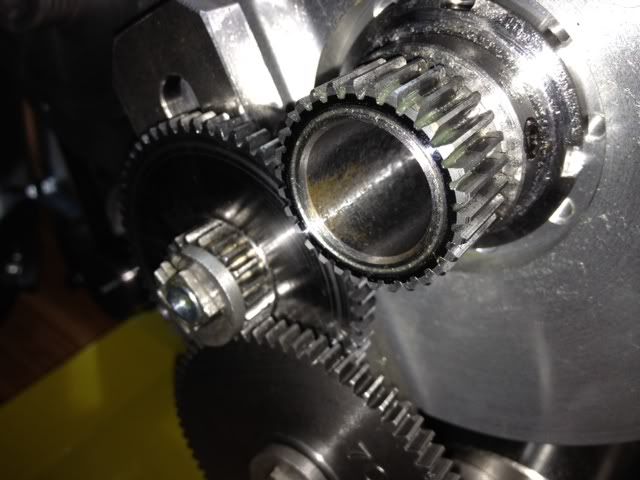
The hole in the cover is almost 25mm but the alignment is off to one side (spindle bore and the hole in the cover are not concentric). By the way, is the "nut" you mentioned the head of the bolt of the drawbar or it is really a nut to be fastened onto a rod making the drawbar?
Pete, the Sherline lathe has MT1 spindle which I mounted tools, collet chuck (ER16) etc. Except when using the faceplate with dead center in the spindle, I use the supplied drawbar. I asked about how can I do with the MT3 spindle bore on the proxxon lathe because I couldn't figure out how to use a drawbar on it. Thanks for clearing the part on its possible use without the drawbar.
I've 2 Sherline mills (one CNC'd and one for manual work). May not do vertical milling on the lathe that often unless when need arises.
Norman, I just ordered this afternoon (SG time of course

) a 4-jaw independent chuck and the centre turning accessories. When I bought my lathe, I also purchased the fixed and follower rest (or traveling steady per proxxon website). I did cut external threads on a piece of steel to make a bolt with a short length of stainless (stainless because that was the only piece in my box with close enough diameter) sticked into the bolt head to make a locking lever for the tailstock. Now I don't have to search for the hex key to lock or unlock the tailstock.
I'll continue to look for simple projects to do to get the basic right before moving to more complex stuff. The collet chuck for ER32 collets (those that mount onto the backplate of the lathe) will be one I would like to attempt. Most importantly, I want to learn clockmaking.
Regards,
Wong