About two years ago, I got a DRO for my lathe for Christmas, and have waited to clean and fix up the lathe before installing it, and not willing to take it out of service even for a week or so, have had the DRO on the shelf eating its head out in the stable, so to speak. In my radial engine build, I found it necessary to remove the headstock of my lathe, and do a general cleanup of the whole of it, and got a chance to measure all the ways and check for wear, and turned out surprised, needing no real work, just lots of elbow grease cleaning up fifteen years of swarf.
A couple weeks ago, having had a bad morning, I decided it was time to take a break and do the duty of installing the DRO. It is a "Shooting Star Technology" setup, using racks with pinion encoders, with an accuracy and readout of half a thousandth, and one I've had working on my mill for some time with good results.

First off was establishing where the X axis would be placed. Plenty of room at the back, and no interferance as long as I don't put on my taper attachment, which I haven't used in years.
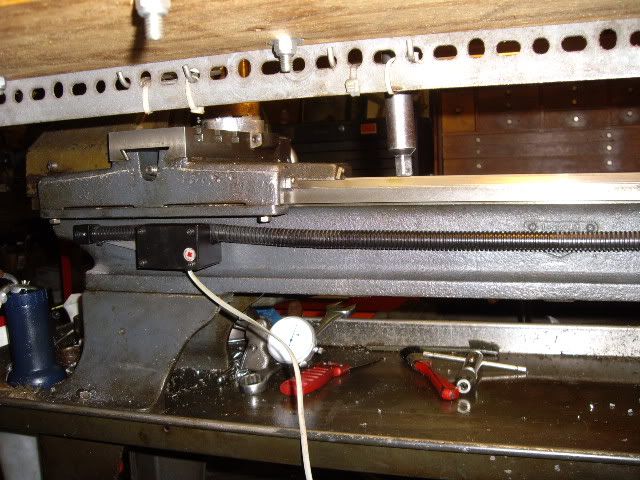
traversing the carriage to the tailstock end, ensuring proper clearance, and establishing where the mount hole for the rack will be
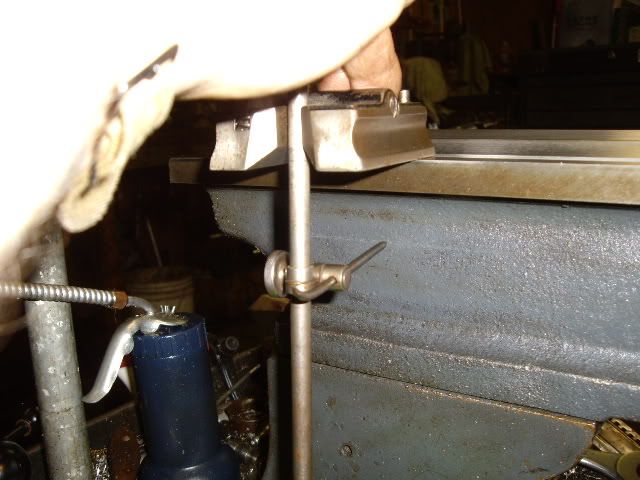
marking out the heighth from the rear way on the tailstock end with a surface gauge
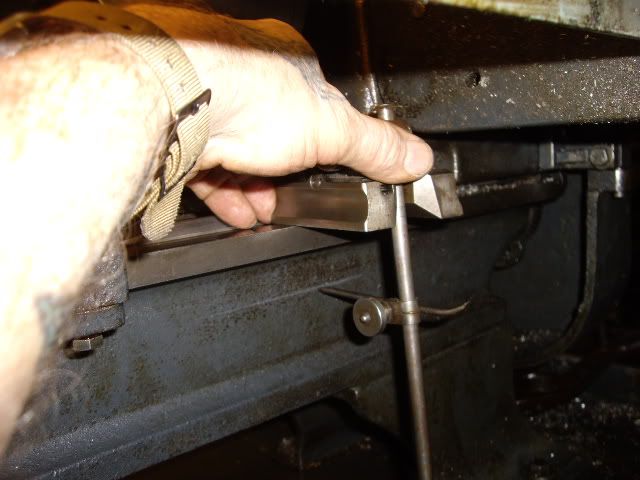
marking out at the headstock end with the gauge still at the same setting
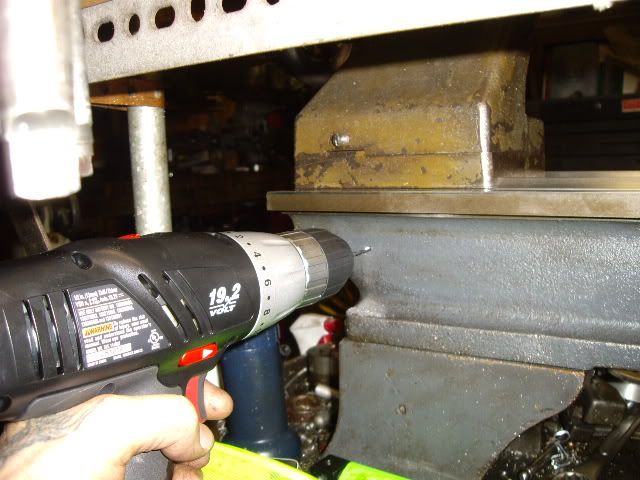
drilling the mount hole at the tailstock end of the bed
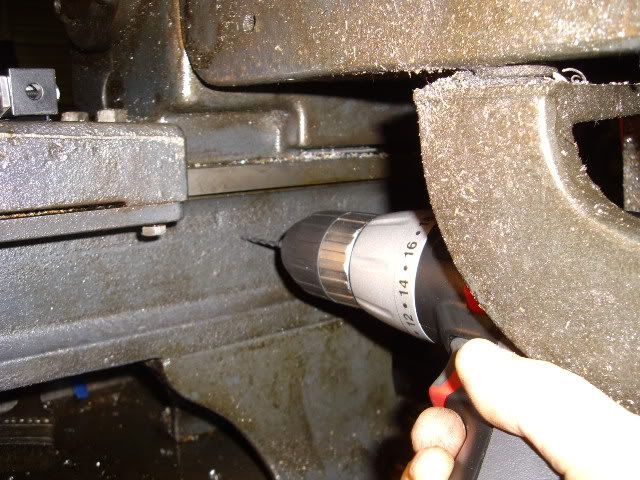
drilling out the headstock end mount hole
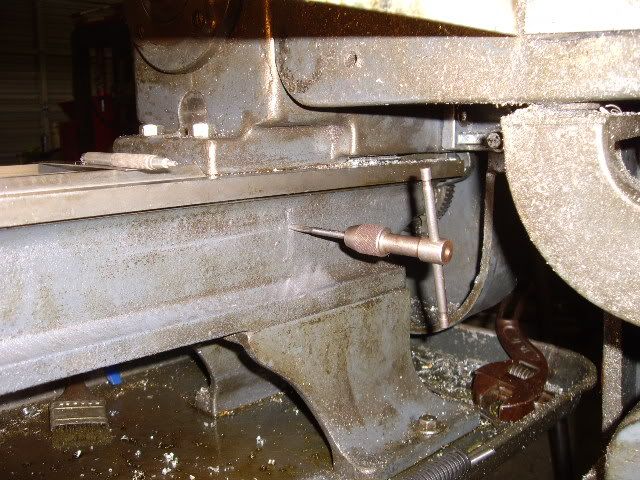
tapping for the 10-32 mount screw
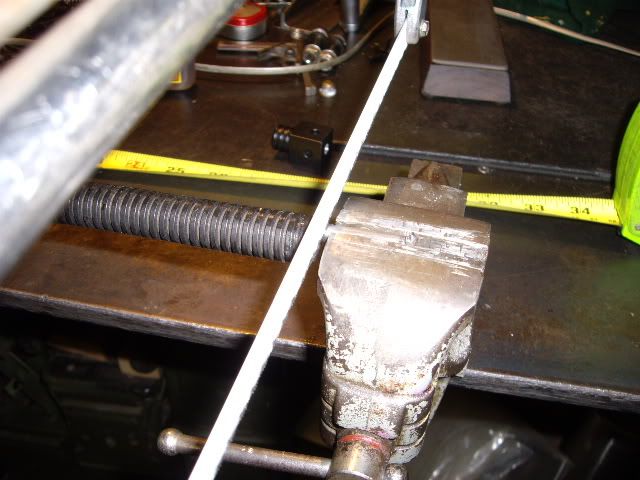
cutting the rack to size
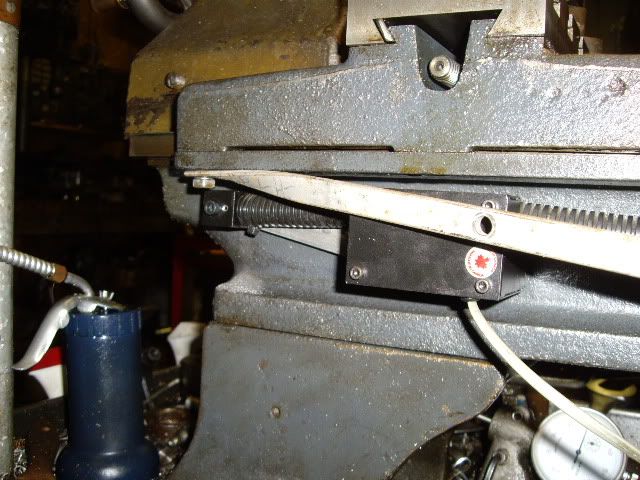
bending up a piece of eighth by half inch stock to mount the readout head for the X axis
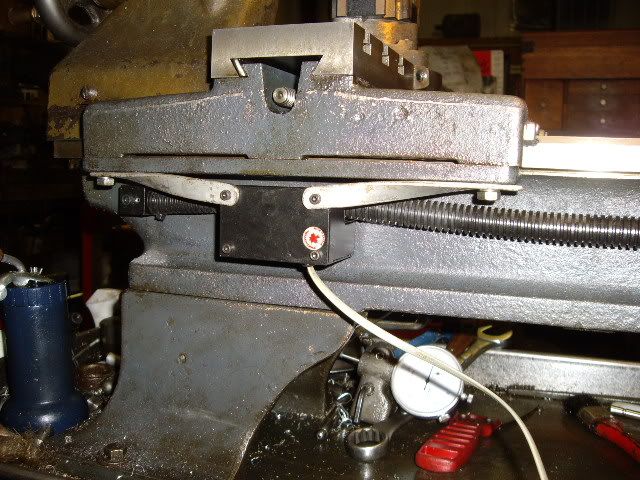
two straps cut and fit to hold the readout head secure and accurately

looking at the cross slide, planning for mounting the rack and read head on the front of it
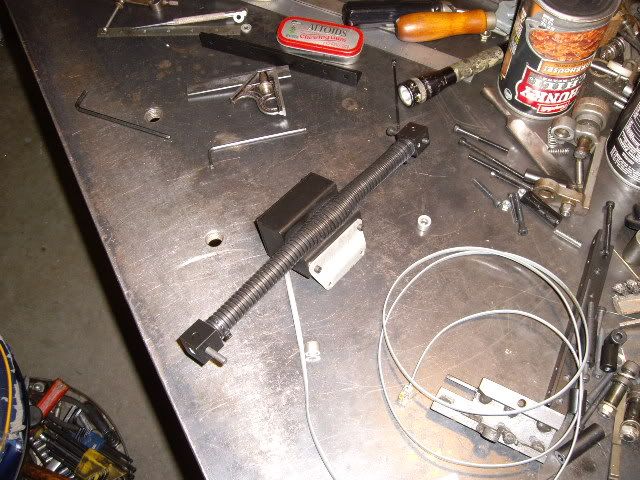
choice made, rack cut to length, bracket to attach the readout head attached to the bottom of it, to screw to the carriage
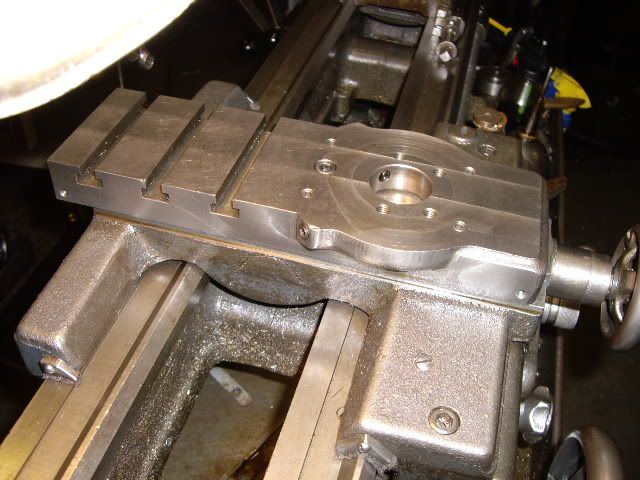
cross slide drilled and tapped, remounted on the carriage, note holes at each end of the slide for mounting the rack
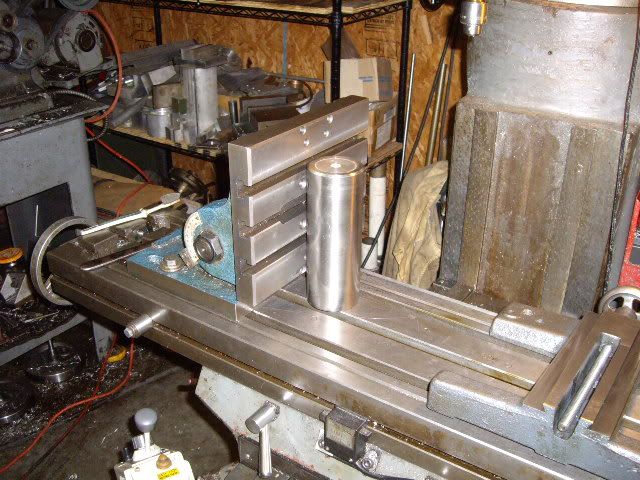
setting up the angle plate to support the carriage vertical, for drilling the readout mount holes
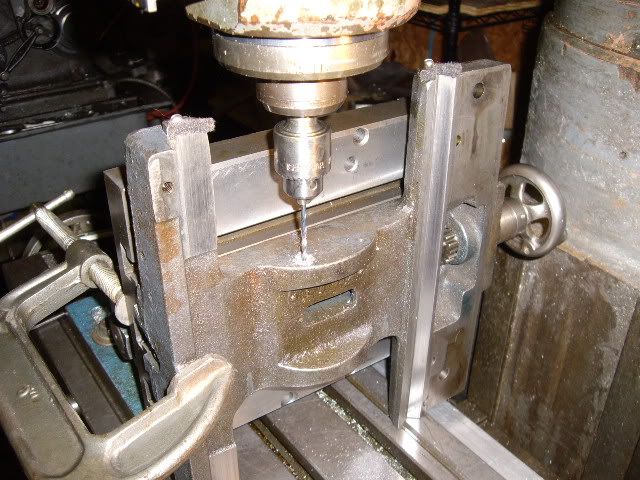
drilling mounting holes in the carriage
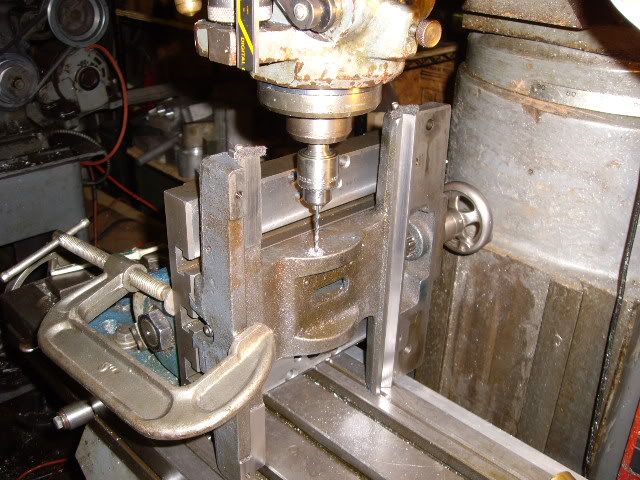
another view of the set up for the carriage
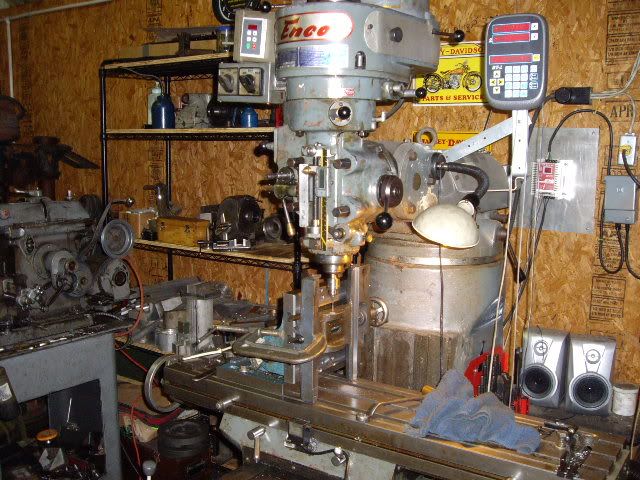
a perspective shot of the carriage on my mill.

carriage reassembled to the lathe with the cross slide set up for assembly on the carriage for mounting the rack and readout head
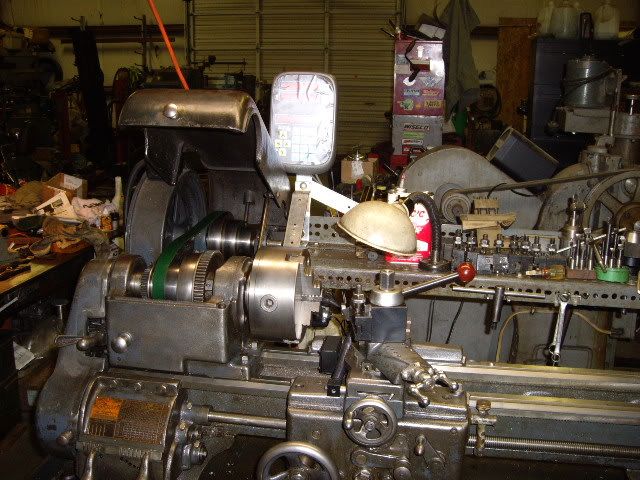
cross slide in place with rack and readout head mounted, not happy, I've lost two inches of room in front of the carriage, and put the readout head in the best place to collect swarf and get hit with a chuck.

another view of a bad choice
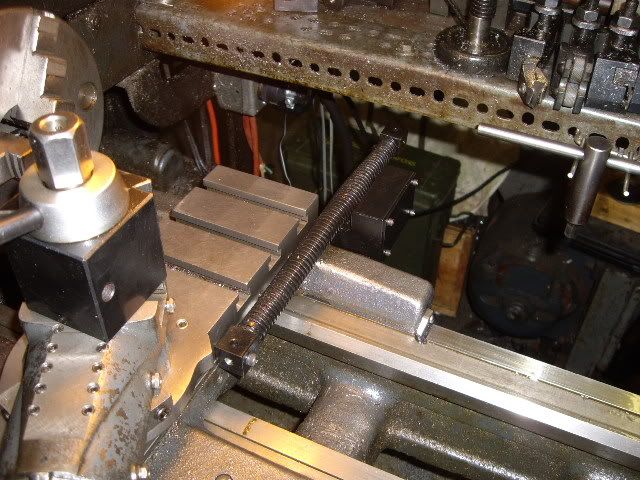
a week later, with the rack and readout head mounted on the rear of the carriage and slide, a much better set up.
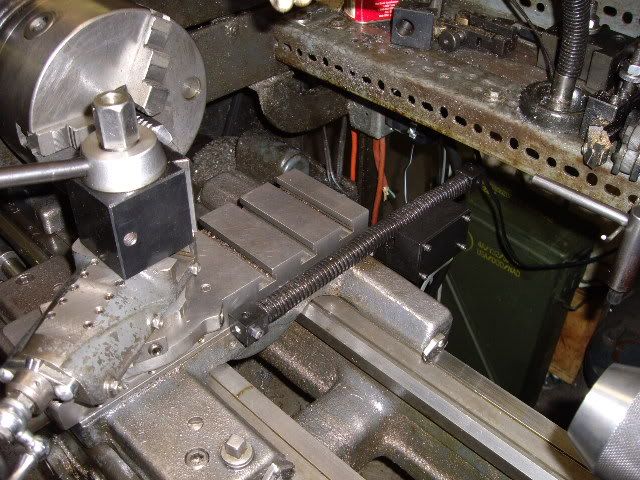
Another view of the completed installation, everything working as designed.