Hi Rob, I don't know where you've got with your engine, but in reviewing your posted pictures, and looking at your equipment as shown, if it were me, I'd go back to the original cylinder or one like it, and complete out the "poppin" you've started with, as it is one of the more easily gotten running forms, and with it together and running, you will have the opportunity to see issues which are not apparent except from a running engine.
In my own experience, it seems the most important aspect of these engines is a dead straight bore, lapping it to a fine finish, and getting the piston fitted with less than half a thousandth, and free the length of the bore. The valve arrangement of "poppin" is probably the least friction of any of those I've used, and the easiest I've had so far, in getting timed, and a good seal.
I'm using Luftkin spring gauges, the kind that lock with a twist of the handle, to measure, measuring the gauge with a micrometer, to get the bore round and straight, and using the natural action of the lap to get the taper out, taking a piece of delrin, turning it to the measured diameter, coat the lap with a polishing compound, and then rubbing in some jeweler's rouge, and carefully rotating the lap in the lathe at slow (150) or so, and sliding the cylinder on to the lap. My lathe turns about half a thousandth taper in two inches, so I make the lap to fit the large end, and gently, with lots of polish with rouge, work the cylinder all the way on and lap it until it mike's out within a tenth end to end.
If you have more taper, or if I have a longer cylinder, I sometimes have to make two laps, or, if it is a size I expect to duplicate, I will make an adjustable lap, which is the best solution, as you can keep adjusting until it's perfect, and not have to quit just because that's all the lap will do.
Once the cylinder is lapped, then turn the piston, making sure the coefficient of expansion of the piston is less than or equal to that of the cylinder liner, and you can go with the piston as turned, if you feel you have a fine enough finish, or you can lap the piston as well. With that bronze liner in the aluminum cylinder, I'd go with an iron piston. I'd bore a bit of aluminum bar to the nominal size of the bore, say we're talkng about half an inch, and the bore turned out say .504 after reaming it, and lapping it to a nice cross hatch pattern measuring dead even the length.
I'd ream out the aluminum about an inch deep, bore it if the lathe bores straight, and bore the oversize, otherwise ream it, cut it off and then split it down its length, and set it aside. Turn the iron piston blank, with lapping clearance, or cut it off, and put it on the end of a piece of shaft, then smear the piston with polish and rouge, assuming the lap fits over the piston, and using a hose clamp to adjust the fit of the lap, and springing it if it's too tight, so it must be clamped to lap, and then lap the piston tightening the lap as it works smooth.
Once it enters the cylinder, you get to find any tight spots, and decide if the whole cylinder is tight, more lapping on the piston, if it is just a couple spots in the cylinder, then its lap the cylinder in just those spots. This done right, with everything working out, will fit closer than a tenth, if necessary, although it is shortuts through the lap making part.
If you get your piston and cylinder to this point, I think you'll find "the poppin" plans will give you an operational engine, and the timing specs are good enough to get you started, although timing is another thing which every engine decides what it likes for its self.
The single greatest obstacle with these engines, in my own opinion, is that starting one cold, the principle product of burning alcohol is water vapor, and if you've oiled your cylinder at all, the first few strokes will quickly emulsify the oil and water vapor, and suddenly the engine has five times the friction as it did before the flame. I squirt WD-40 in the port, flip the engine through a few times, and generally get fifteen seconds or more running, with the vapors of the WD burning, and aiding in running, and have to rinse out the water two or three times, while the engine gets hot enough.
With my last engine, I started it after all the assembling, with an iron liner in aluminum fins, with no oil (forgot it), and found the engine turned up and ran up to speed with the first flip, and it was already hot when I remembered to oil the cylinder. I can take it apart and dry it, and it will run up again, the same way, but it needs oil to run, and so I put up with rinsing out the emulsion each time.
I am currently replacing that piston with one of graphite, precisely because it will run in the iron cylinder liner without oil, and should be able to run right up even from cold.
My Duclos "flame sucker" will start right up cold if I get the flame exactly right, and get lucky, but it won't run with oil, it doesn't have enough power, and I use graphite powder to lube it, read scribbling in the cylinder with a pencil, and the same on the piston. It has a half in bore, the other engine I just built has an .815 bore, and needs more than graphite powder. That is the one getting the graphite piston, and probably a graphite valve as well.
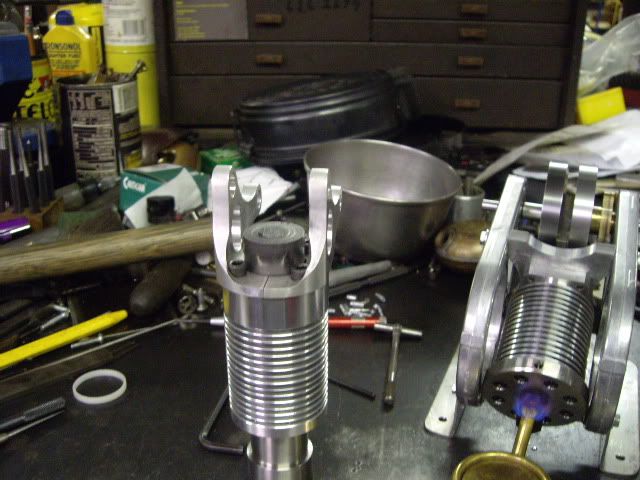
The engine to the right of the picture is "Vlad the inhaler", the engine I am modifying with the graphite piston. It is in essence, a modified "poppin", using the head and cylinder set up of that engine, with odd bits from the scrap bin for the rest. If you look at my post on the Jerry Howell vacuum engine, it shows using a well seasoned piece of oak, (seasoned more than thirty years) turned to about a nine or ten inch lap, with a brass tube pressed and locktited into aluminum for a cylinder, which is why I used the oak, as it is open grained, and carries the rouge well with the soft brass. That would be the engine parts array coming together on the left in the picture.
I don't want to steal your post, or impose my ideas on anyone, but I've found that getting the piston fit to the cylinder has been the cause of most of my problems with these vacuum engines, with friction in valve train being second. Vlad has the simplest valve train of any I've built, and been among the easiest to enjoy except for the issue with flushing her, and that is why the graphite piston experiment. It isn't exactly the same as the "poppin" valve train, but very close, and if you just don't get that engine running, try going to a larger bore, with a corresponding stroke, bigger means easier to start and more forgiving of tolerances.
I hope this helps you get your flame eater together, and enjoyable, they can be a great pleasure to have when a more complex engine is giving one fits, and not cooperating.

Cheers, mad jack