I posted this originally over on the HSM site in part answer to a query of why are there more small lathes than mills and we are not talking imports here.
Sorting some bike pics out the other night , all from 1974 I found the pic's of making the new pistons for the Jones racer.
Made from forged lumps of RR56 alloy [ Thank you Rolls Royce although you didn't know ] all the machining was done on a ML7 lathe I owned at the time, in fact it was the only machine tool I owned for a number of years, just as most of my contemporaries.
There are only 4 pics so they will fit into this post, I can't remember if there were more but these 4 are all that survive.
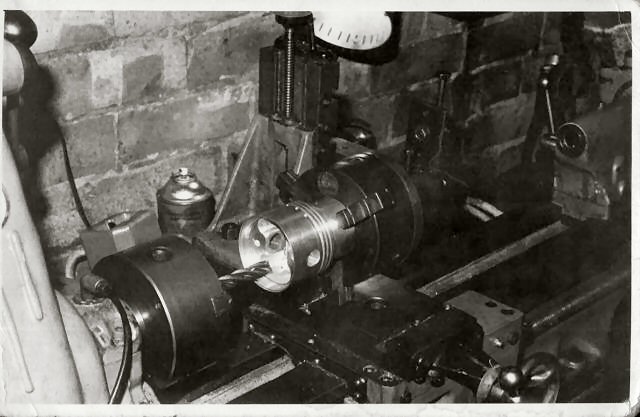
This shows the rough turned piston with oil holes already in, gudgeon pin hole in [ wrist pin to the cousins ] and using a vertical slide and home made indexer, seen better in pic 3 , the inner shape is being formed.
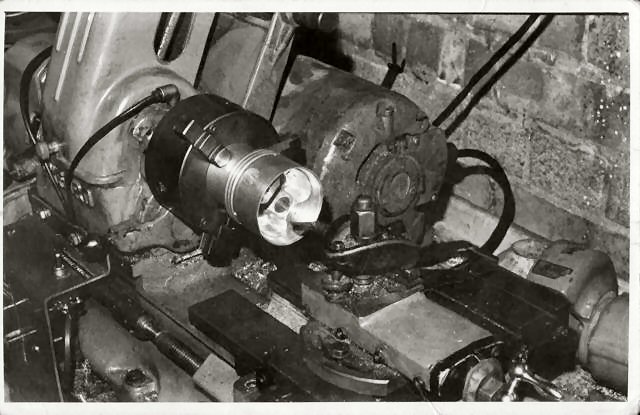
Not too clear in this pic but the boring tool is a long L shaped tool so it can remove metal past the bosses and expose the oil holes.
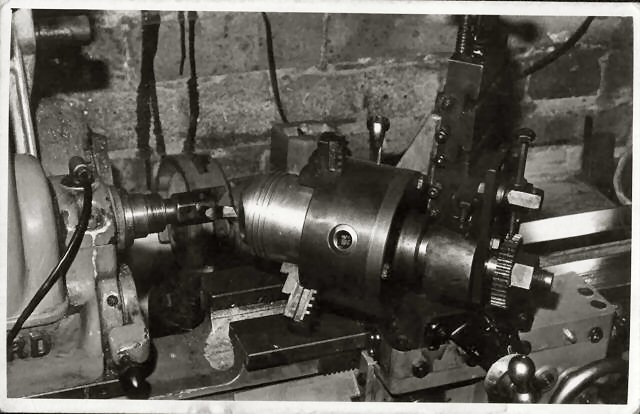
Nearly finished and putting the valve undercuts in with a fly cutter. Simple indexing attachment using 40T changewheel is visible, only the outside diameter to finish at this stage.
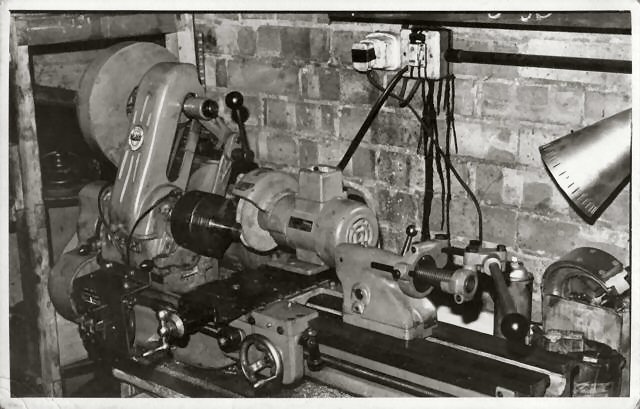
Setting up for grinding the gudgeon pins, probably staged as the pins were smaller than this, note lever feed tailstock and the front brake of the Jones in the background.
All together 4 pistons were made for two of the engines, these went on to do many laps in the Isle of man and Nurnburgrink in Germany, in fact they must still be in the bikes as they exist today as no further work was ever done on them except cosmetics.
Would it have been easier to do on a mill ? Definitely, but that lathe cost £150 brand new in 1969, a mill new in 1975 would have cost £800 and I was on £14 pounds a week wages, just married and with one child.
John_S.