This is more of a record of my machine shop learning experiences.

Hopefully other beginners like me can learn from my unintended outcomes and the old timers well they might just get giggle.

For my first turning project I went ahead and made my first tool. which was a fly-cutter to bolt to the face plate. On an 8 inch face plate it covered a large surface. Machining up my second project (which was a much needed angle bracket) I count both these projects a success as well as being very educational.
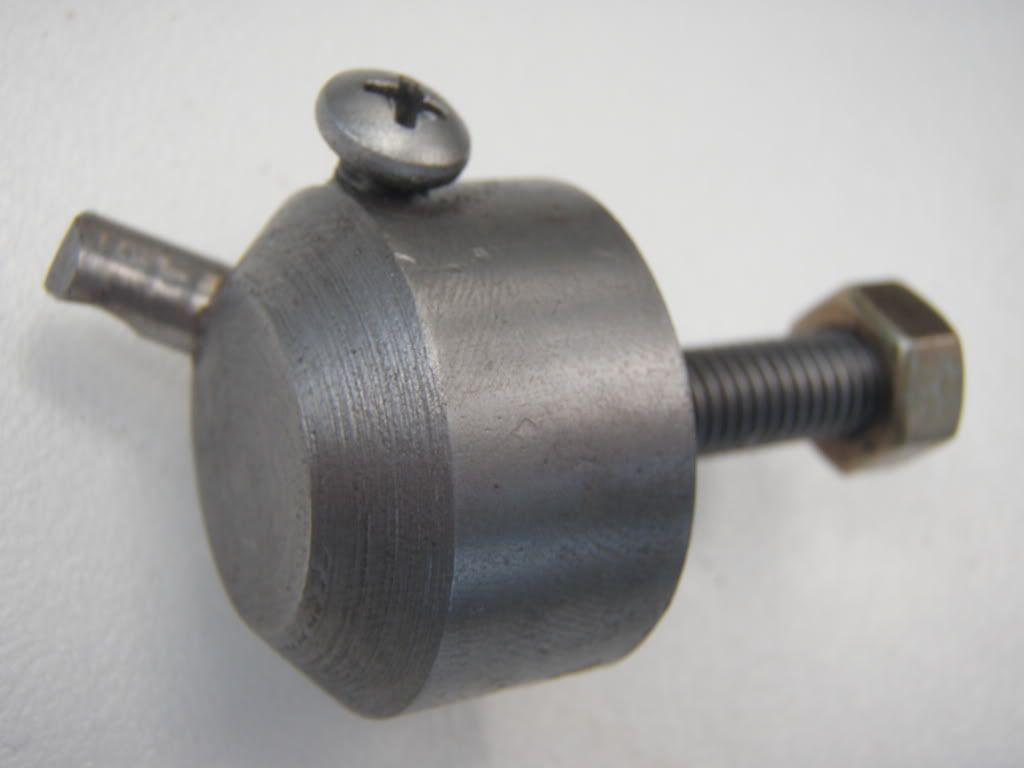
Having bought a lathe without the benefit of 20/20 hind sight I soon discovered it is difficult to mill anything on a lathe that has no T slots in the cross slide. (you'll see in later photos).

I don't think Mrs was quite as easily convinced

but it was obvious to others, This Workshop Needs a Mill.
Of course the type of mill drill I could afford, typically comes with a drill chuck but no collet chuck
So the start of my next Project #3MT Collet Chuck
Now on with some milling! What .. No T Nuts!
Oh well! lets make some .. on the mill?
At this point there is a song stuck in my head.
### With what shall I hold it dear Eliza? with what? ###

by chance I have a few ½ Whitworth cap head bolts, (what a shame there not 5/8 I think they would fit even better) any way, if I file a few mm off each side of the head they should do nicely to hold the vice down while I mill a piece of bar to make some T Nuts (with light cuts of course, I don't want to rip a chip out of my nice new mill table)
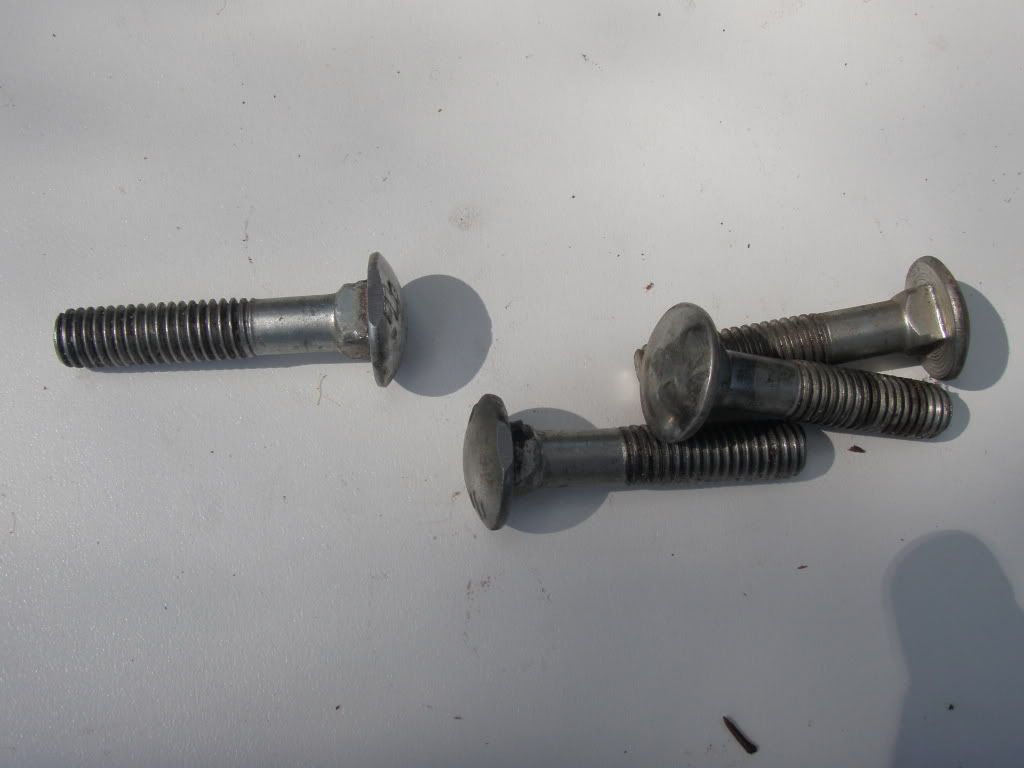
Now where were we – thats right making a #3MT Mill Collet Chuck.
The first hurdle is the #3 taper.
The book says the Taper starts at a diameter of .778 and for 3-3/8ths of an inch it tapers out 0.0502 per inch on the diameter.

I don't know about you but as a novice I'm struggling to understand what it means let alone measure it with a ruler and calipers.

But I have seen something that could help, on the cover of one of Tubal Cain's books. See below if Nexus Don't mind the plug

so from this example, if I mount the 3MT centre between centres ( at the head end center drill a piece of very old round bar) and then line up the side of the compound slide with the edge of the taper, it has to cut a 3MT right?

Worked out o.k. in my head but when I went to the lathe there's two problems

1.the edge of the compound slide is well below the center height and
2.tail stock is in the way.
If I make a parallel block (on the mill) I can sit that on the compound slide and measure the gap at both ends of the center at centre height.
The rest is is just threading and turning.
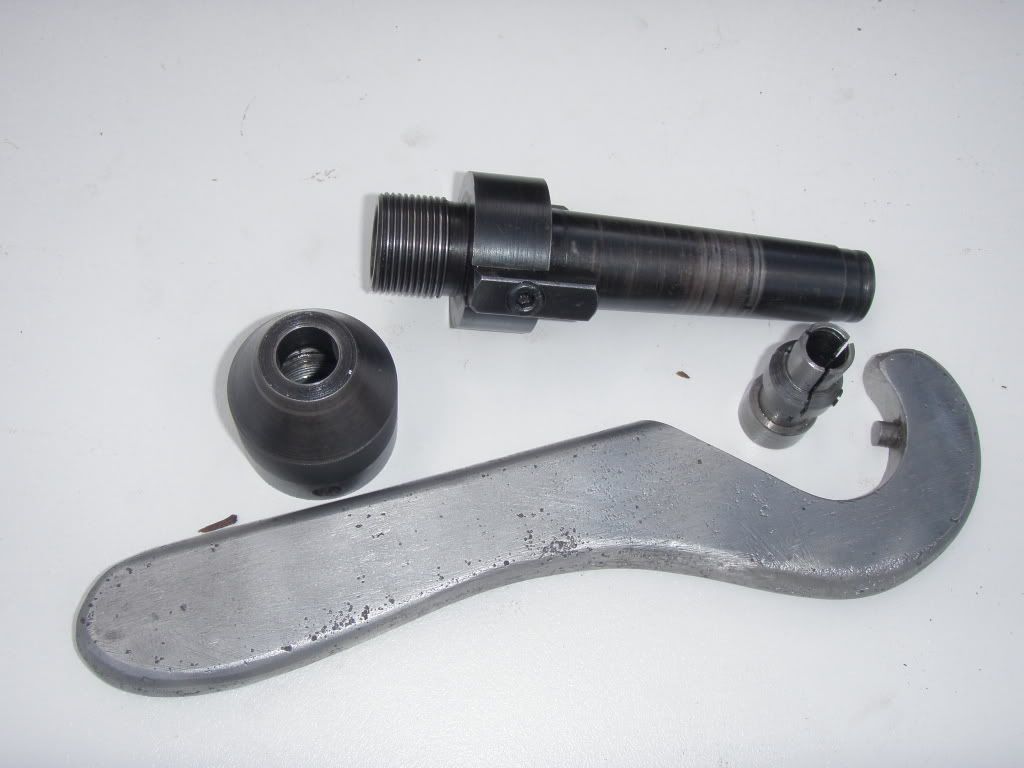

Except the collet tightening handle and the bluing, I'll talk about them another time.