Hi all, thanks for all the interest and interesting comments, much appreciated. This engine has sort of decided its self how it would work, and what it will look like, but I've managed to get it to a point where I really like it, and it's close to eating some flame. I had to take my dog to the vet yesterday, he started limping the night before, and as it turned out it had nothing to do with the fibrous growth on his foot, but a torn ligament in his knee, so Buddy's on bed rest for about eight weeks. When I got home, I put him to bed, and went right to the shop and got started where I left off. It was hard to leave off the night before, so close, however it was good to know exactly where to start.
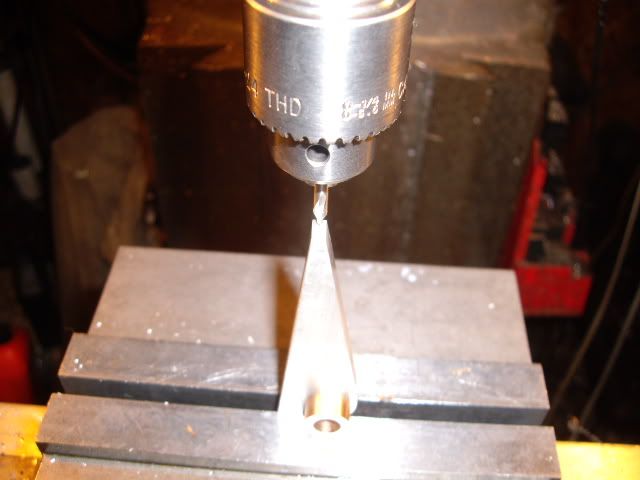
having played with the valve lever I knew where I wanted the pin to be, so I set the lever up in the mill vise, centered a #1 center drill by eye, drilled, and then drilled the hole 1/16th, about half an inch deep at what I think is a good angle.
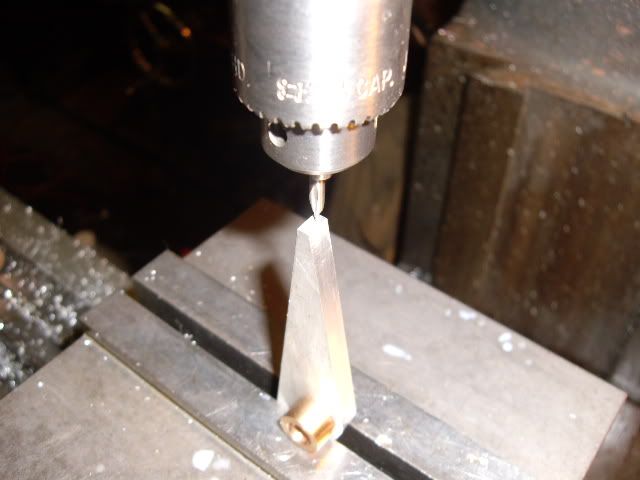
when it is running, I expect to mill out some of the lever and "skeletonize" it, for lighter weight and looks
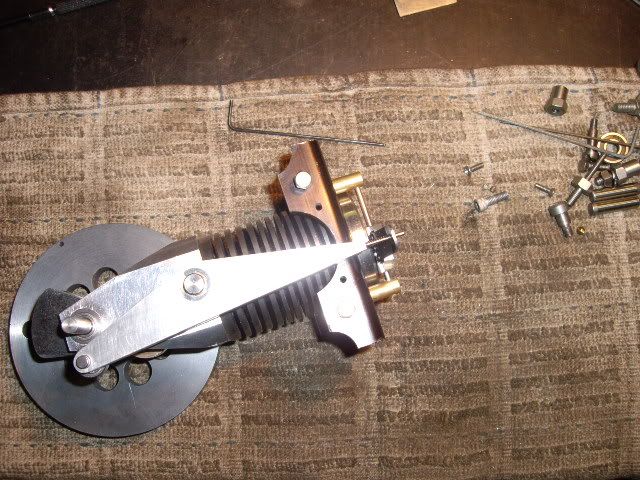
with the lever in place, I was able to establish the place for the hole for the pin in the valve carrier extention, and drill with some wiggling of the extention in the direction the pin will angle during valve actuation, the pin is in place, with a piece of spring cut from a bic lighter flint spring, cut to length
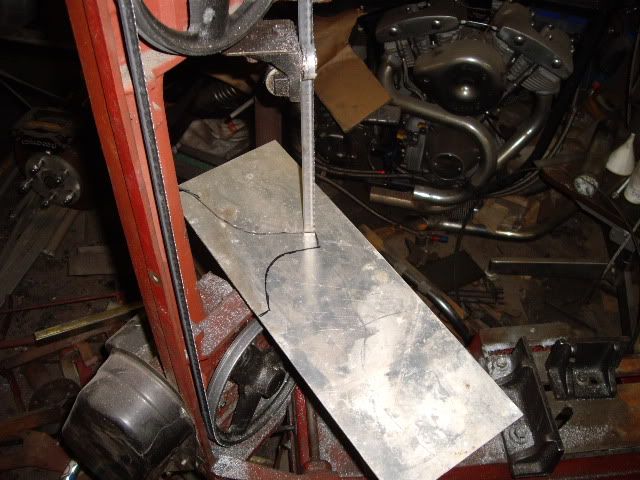
after playing with the valve for a while, I laid the "engine" on my pad of paper, sketched around it with a pencil, then without the engine, cleaned up the lines and curves, cut out the paper pattern, and copied it onto the 1/8th in aluminum with a marker, then put the plate on the bandsaw to cut out the first side
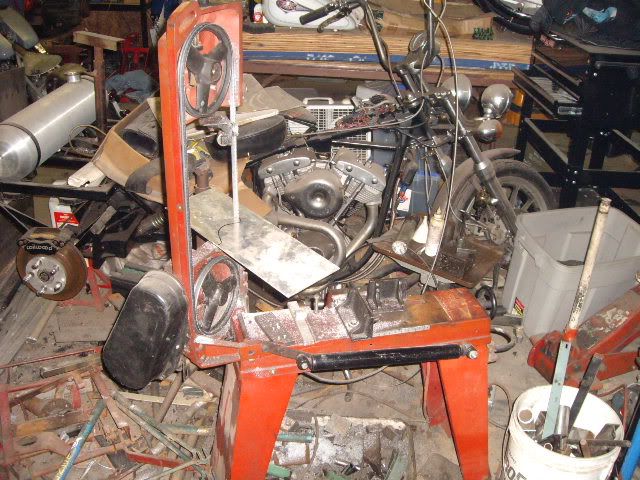
The bandsaw, standing in the middle of much of the scrap it produces, going on twenty five years, rebuilt the first week I had it, and running with only a few repairs along the way, and Chinese


the second side, traced from the first
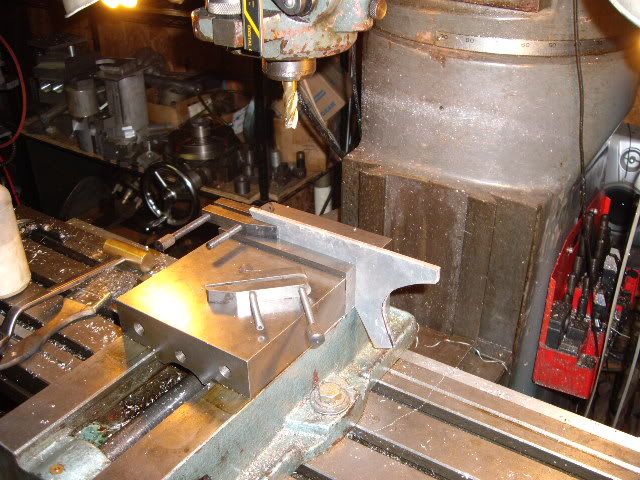
after cutting the second side, setting up in the mill to get the bases even and straight
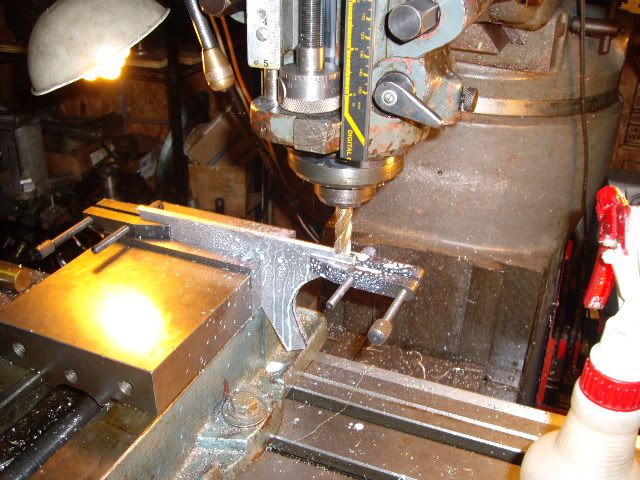
clamps in place to minimize vibration, taking about a 15 thousandths cut off the bottom of both sides together
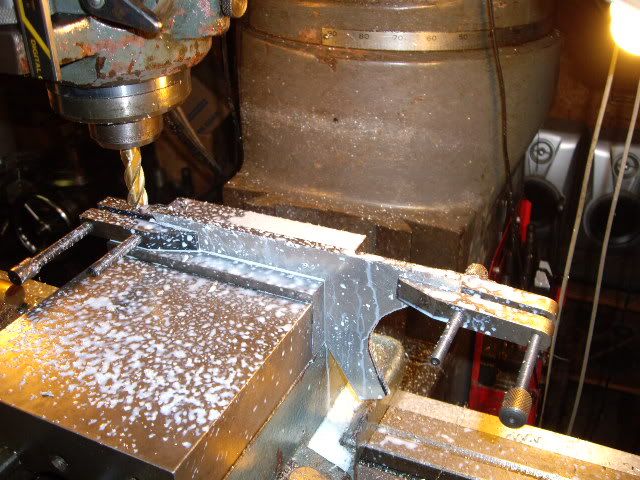
the end of the cut, fifteen was enough, no rough edge left on either side
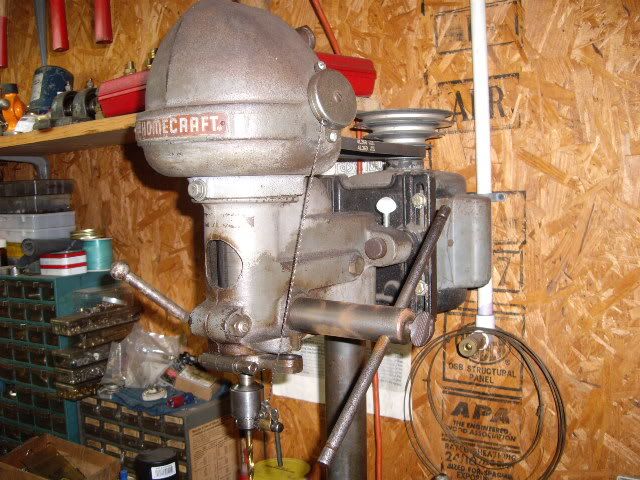
having taken the clamped together plates and cleaned up the profile with a six by 48 in belt sander, I scribed a line on one side and marked out the mount holes for the cylinder assembly, then drilled two holes through both on my small drill press, reserved for high speed, note the chuck key return arrangement, it was on the press when I bought it at a yard sale, a great idea for keeping the chuck key
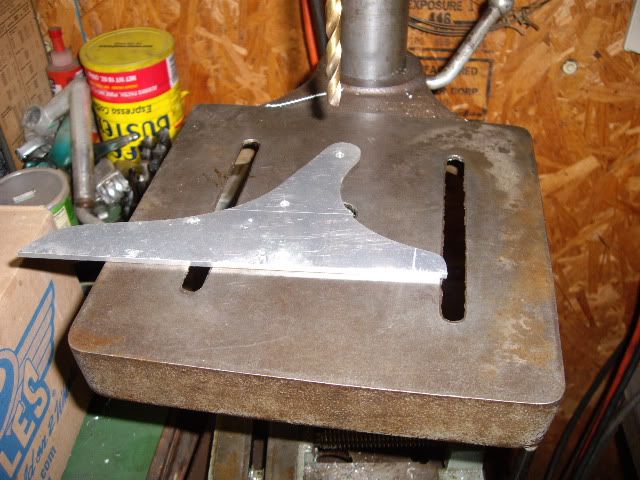
having drilled the first two holes, which are the same on both sides, now drilling two more holes which are only on one side, just the breaks of using recycled pieces for a mounting
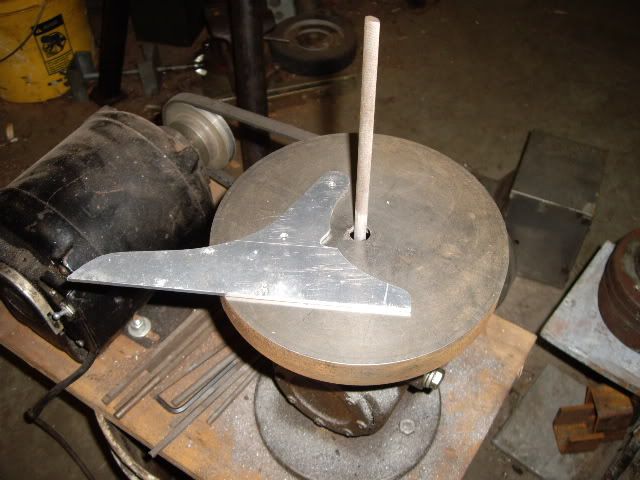
the second side plate interfered with the valve lever a bit, so it got a hole drilled, two cuts on the bandsaw leaving a triangle cut with a radius top, and with a round file in the filing machine, cleaning up the burrs and ugly of the saw cuts, and radiusing the cuts to match the overall flow. The filing machine is from Metal Lathe Accessories, and is a very nice well designed machine, invaluable for profiling the thin metal especially
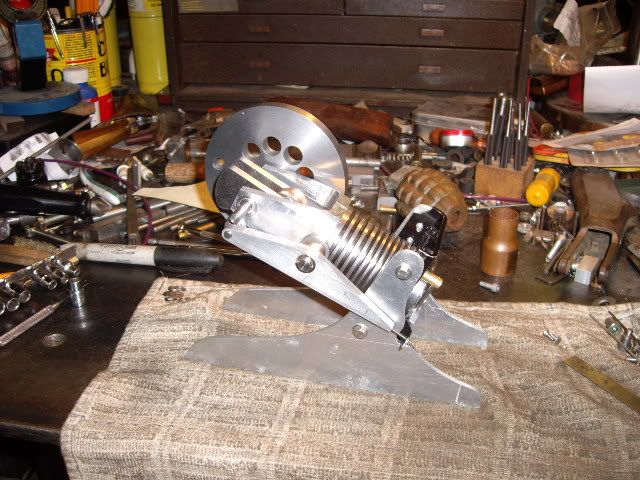
Both sides bolted on, now I get to see live, what I've been trying to see in my head for a while.
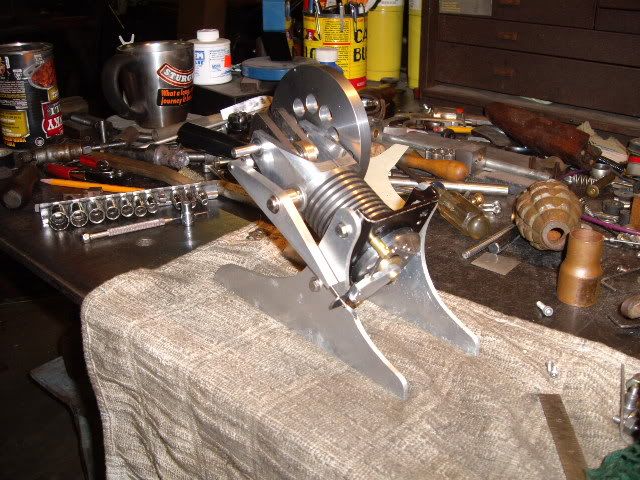
another side view with the valve gear easily seen
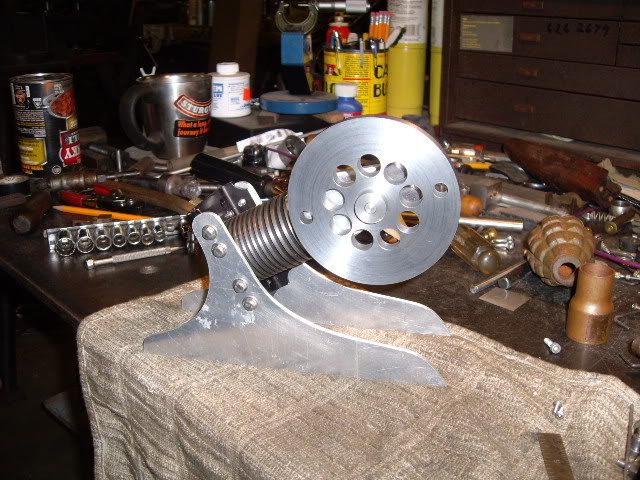
the other side, mostly a view of the flywheel, but looking pretty much like I want
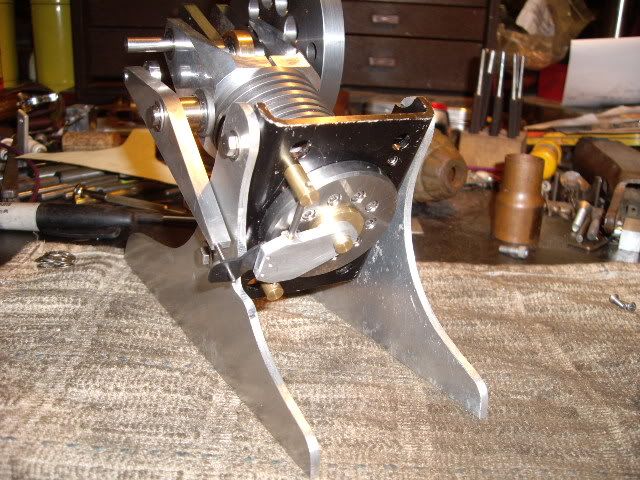
here's a shot of the head end, where the flame will be
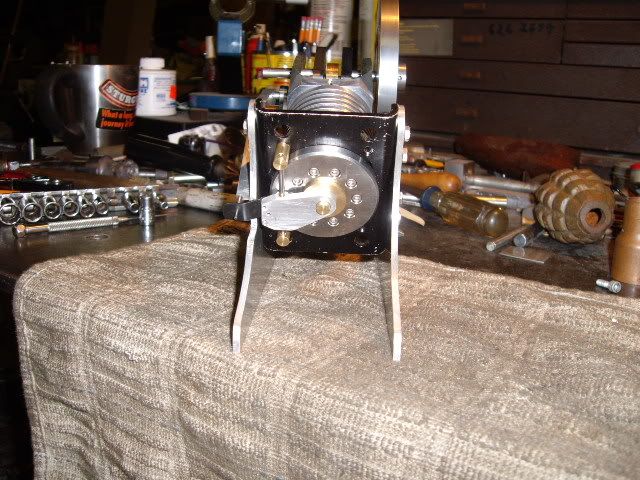
looking straight in at the head, now I have to concoct a cam, having played with the valve lever and measured between the cam roller and a 5/8ths in bearing I slid on the shaft to act as the minimum diameter and baseline for the cam
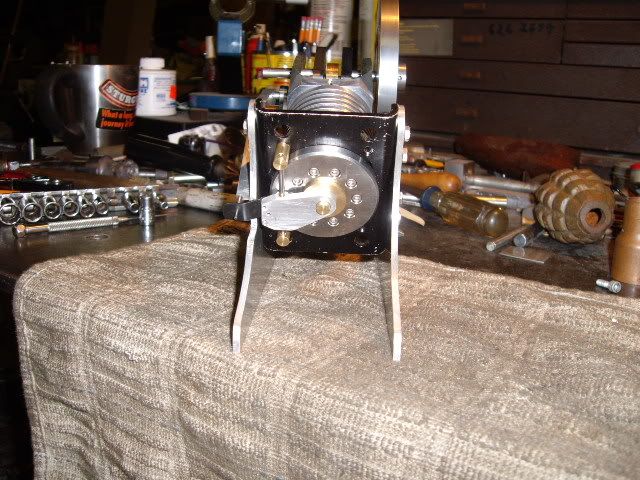
one last shot, the port is 5/8ths diameter, the bore is 3/4 in, with an inch and a half stroke, the valve is 7/8ths in diameter moving up to open. I've got to try to do some adjusting on a friend's Volkswagon fuel injection, by ear since I don't have diagnostic equipment, so hopefully it will go smooth, and I can get a cam turned, and maybe be able to put flame to this eater. Thanks for watching, for the advice, and for all the interesting comments. I really enjoy the presence of friends and aquaintences participating in such a build, and enjoy being among the audience as well. Almost feels like a club, I wish I could invite you all to visit, and could return the invite myself.

:thumbup:mad jack