Right, despite even more moaning for her, here is a quick update - with some machining!
I thought I'd make a start on finishing the wheels off, which were just blanks at the moment.
To turn wheels, there's a sort of accepted method in the loco world and it makes sense. You face and bore / drill the blank in the outside jaws, then turn up an arbor to finish the tread / flange. Once the arbor is turned, you don't take it back out of the lathe so it stays true to the lathe axis, however, as you'll see, in this case I did because I made the bloomin' bits the wrong way around!

Anyway, here goes - it needs to be a fairly large dia to give the wheel some support from behind, another quick way I suppose you could do it is use some rod near to the right size, skim down then with a nut clamp the wheel up against the jaws of the chuck, but here is my method:
Found some suitable material and turned and faced one end for a nice datum:
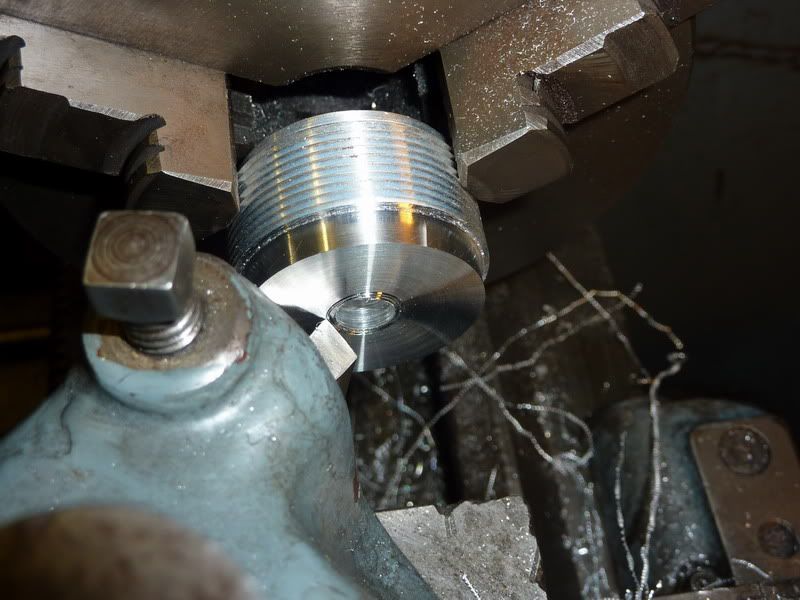
Turned it around so I could grip the datum and turned a larger, new datum on other end which will be gripped in the chuck until all wheels are complete:
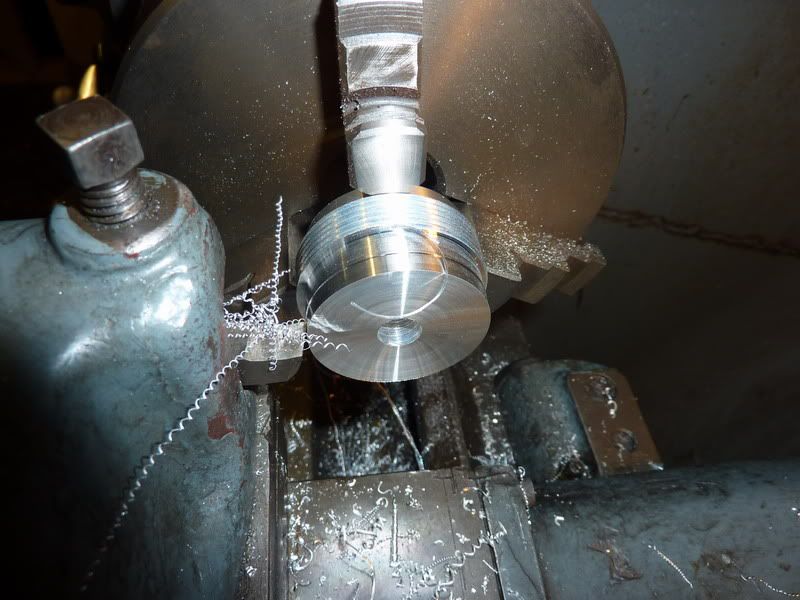
Opened the hole up then tapped it:
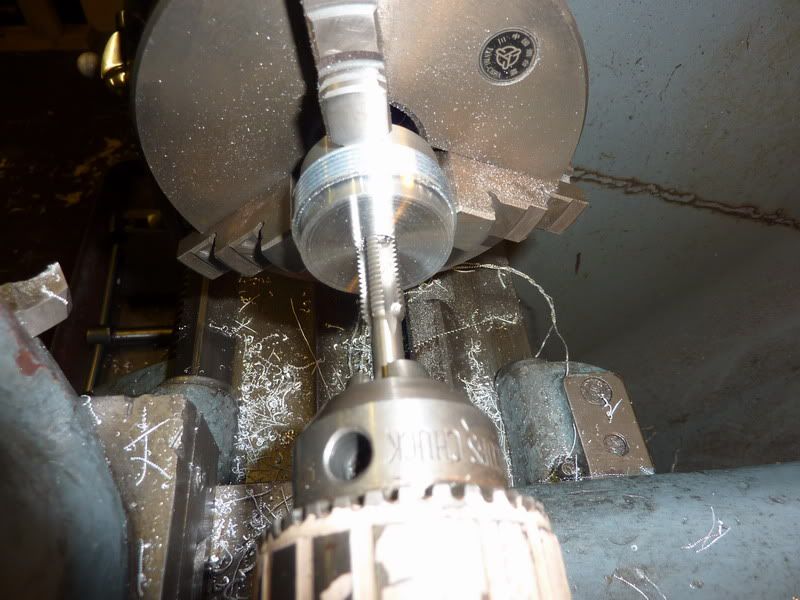
at this point I should have started bolting wheels on and turning them but I realised I'd made this part first instead of the bolt!

So I scribed a line at one of the jaws and made a note of which jaw to ensure it was back in the chuck where it was before - this can't gaurantee zero runout still but I could hardly detect any.
Started making the bolt, face a bit of hex to length:
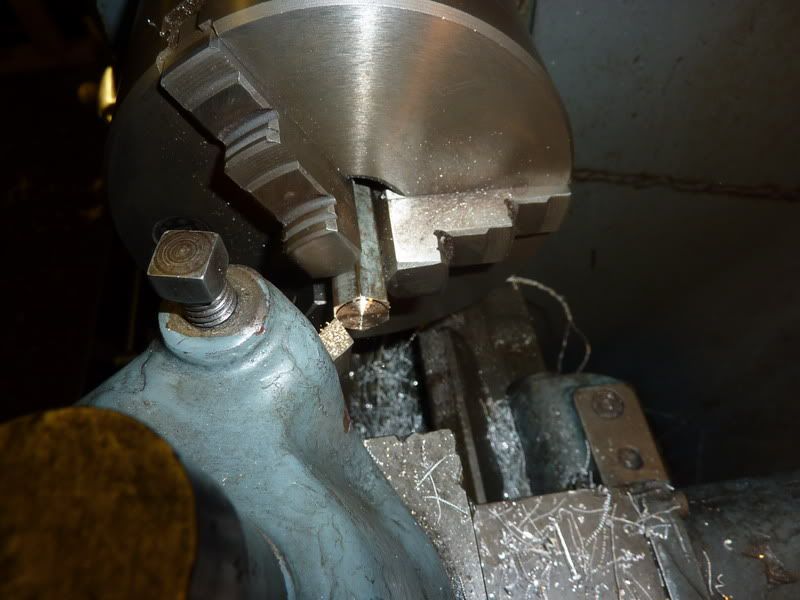
Turning down to size:
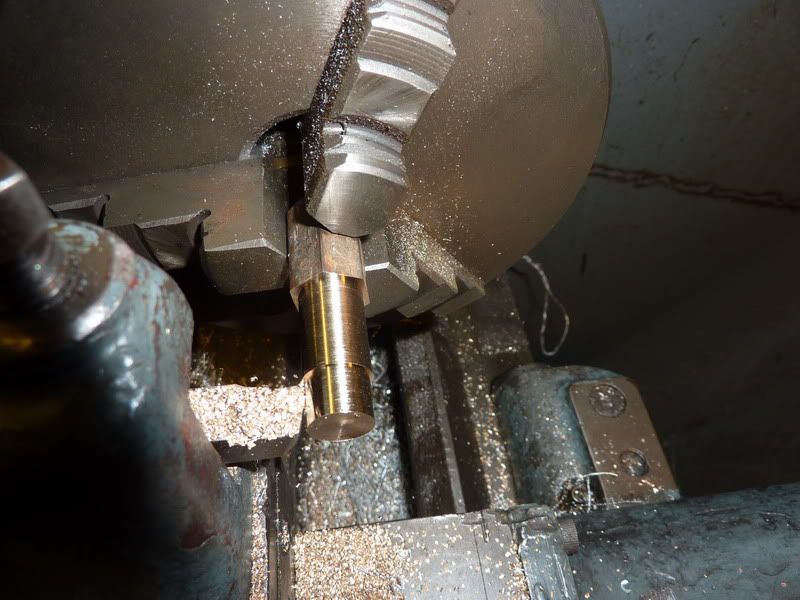
I hate finishing cuts, I took half a thou off but it was still not enough - that's when I get in patient then overshoot on the next cut! This one was ok luckily, maybe a tinsy bit looser than I would of liked but still ok:
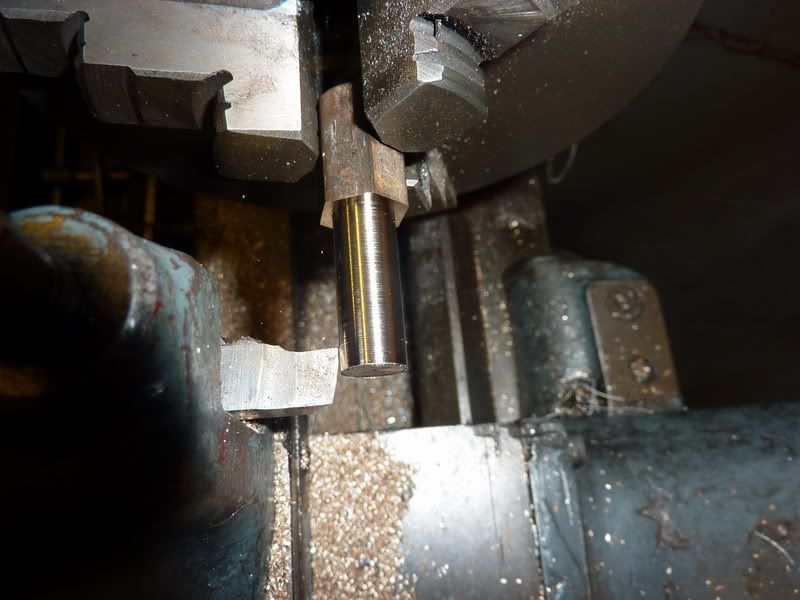
Putting a shortish thread on the bolt, only thing I needed to do was make sure the plain shank was shorter than the thickness of the blanks so it will clamp up:
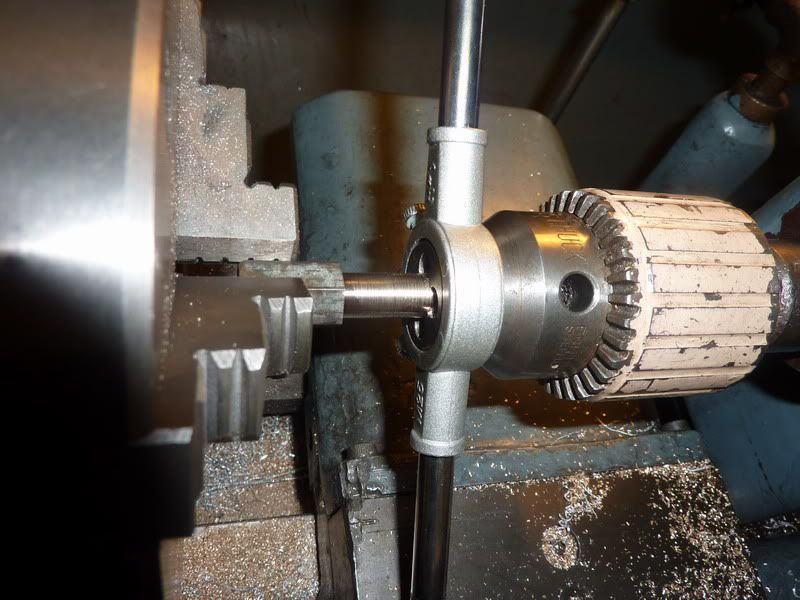
Then I realised I had been given a tailstock die holder for xmas and hardly used it - much easier / better result with this! :
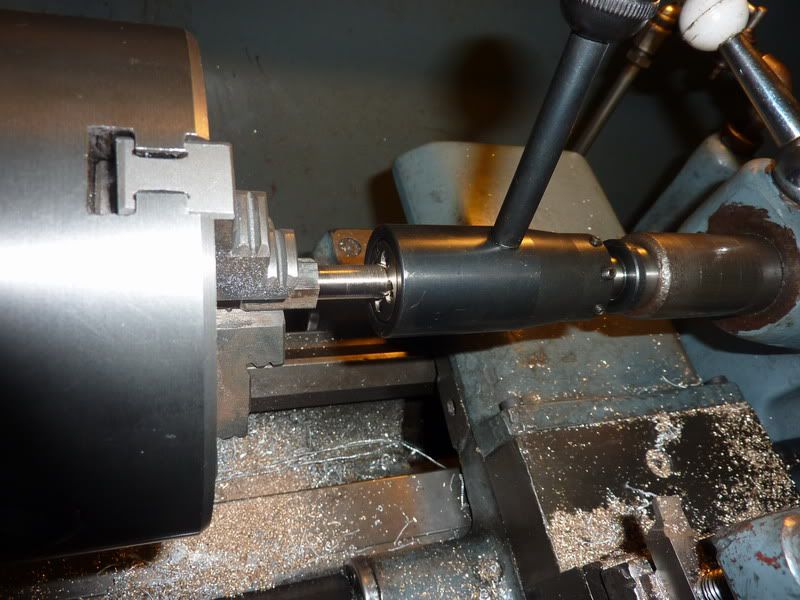
Here is the finished bolt:
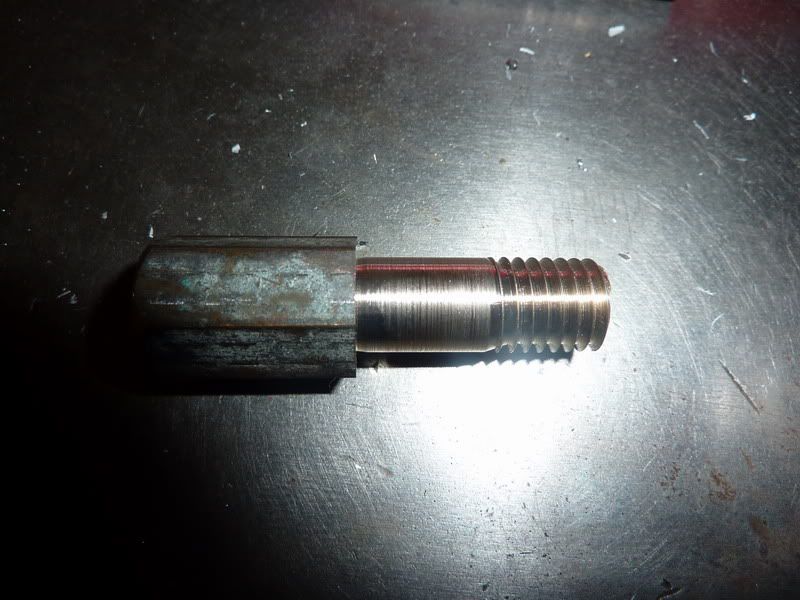
Actually it wasn't, I only left the head long because that's how it worked out - no point sawing, parting things for the sake of it but then as an after thought I put a centre hole in to support it from the other end, so it was a good job I left the head of the bolt long, gives me more room to get in:
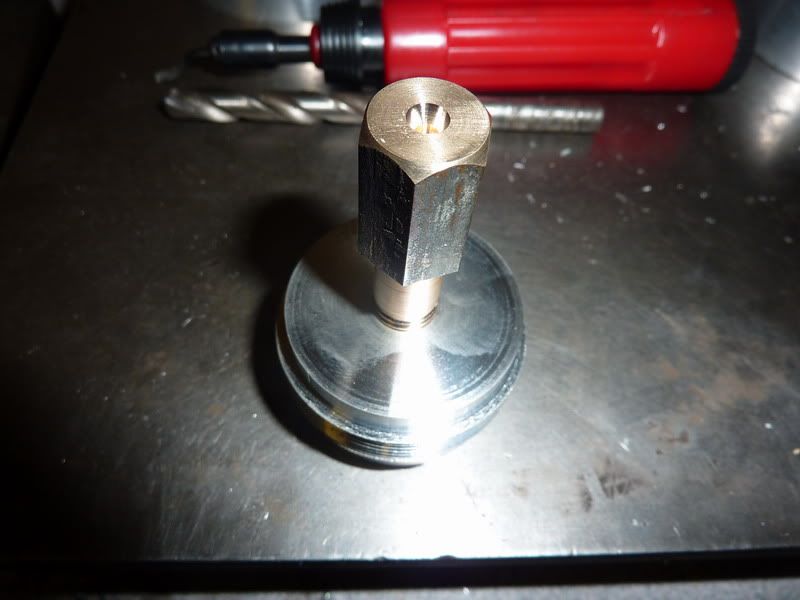
Wheel mounted on the arbor and started truing up the OD:
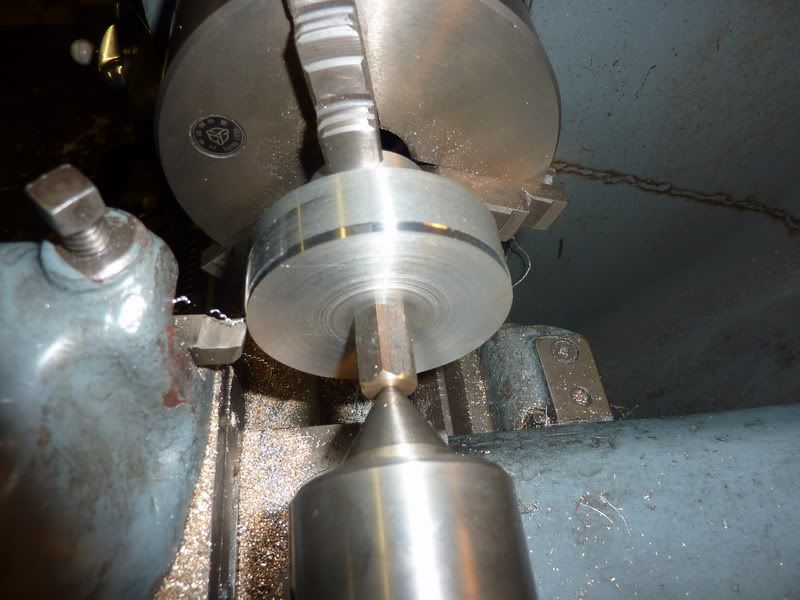
Then turned the tread leaving the flange 1mm over-size. I will need to grind a tool with a 1mm rad to go in and form the radii, think I will get all wheels to this stage first though so only have to change tool once:
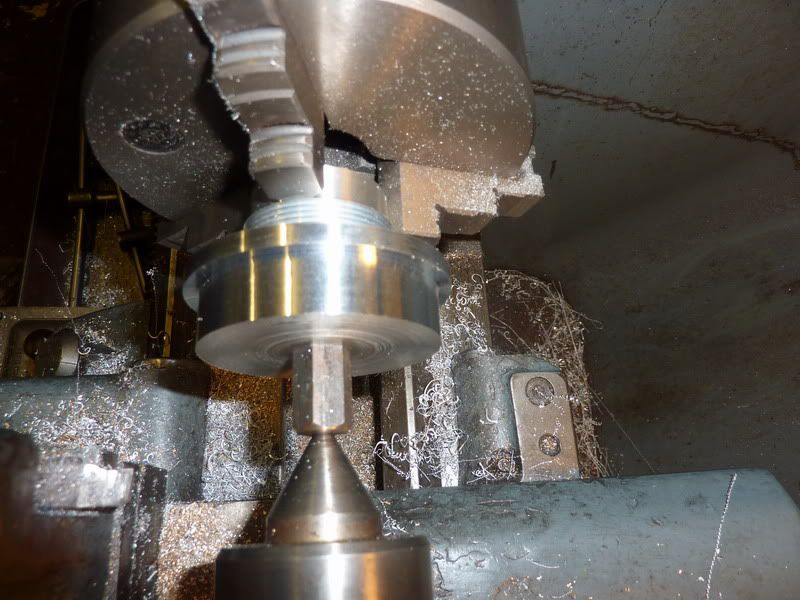
I'm sure many people have seen this sort of method before but thought it was worth showing. An other way is to turn down a longer piece of material to leave a spigot the right size sticking out, then thread and use a nut to clamp - just more work whittling down a larger diameter. Or, you can buy expanding mandrels, never tried these though.
Hopefully tonight I'll get the wheels finished and it'll be a rolling chassis of sorts, though not rigidly fastened together and I can't put fasten the wheels in place as the motor hangers & gears need to go on first.
Nick