About a month ago I realised my small lathe was getting rather noisy, mainly drumming of the pressed steel base and general resonance of tin-ware which really pissed me off. I noticed that the belt from the motor to the countershaft was flailing about a lot so checked its tension and noticed that the motor pulley was loose on the motor shaft - it could be rotated back and forth by maybe 1/16" at the circumference. Ah, sussed! Tightened the grubscrew, checked the belt all much better. A week or so ago, it got noisy again, repeat tighten grub screw, then again yesterday WTF? Something is not right.
I really don't know what, but as I had already bored and sleeved the pulley a couple of years ago when I got the machine and it was definitely all fitted correctly, I can only suppose it is a weak point. A single 1/4" grub screw, not even on top of the key plus a single phase motor which is obviously not as smooth as a 3phase, I presume is just not man enough for the job - so I decided to sort it for good. This is the pulley as earlier repaired, sleeved an with a collar to strengthen the hub.
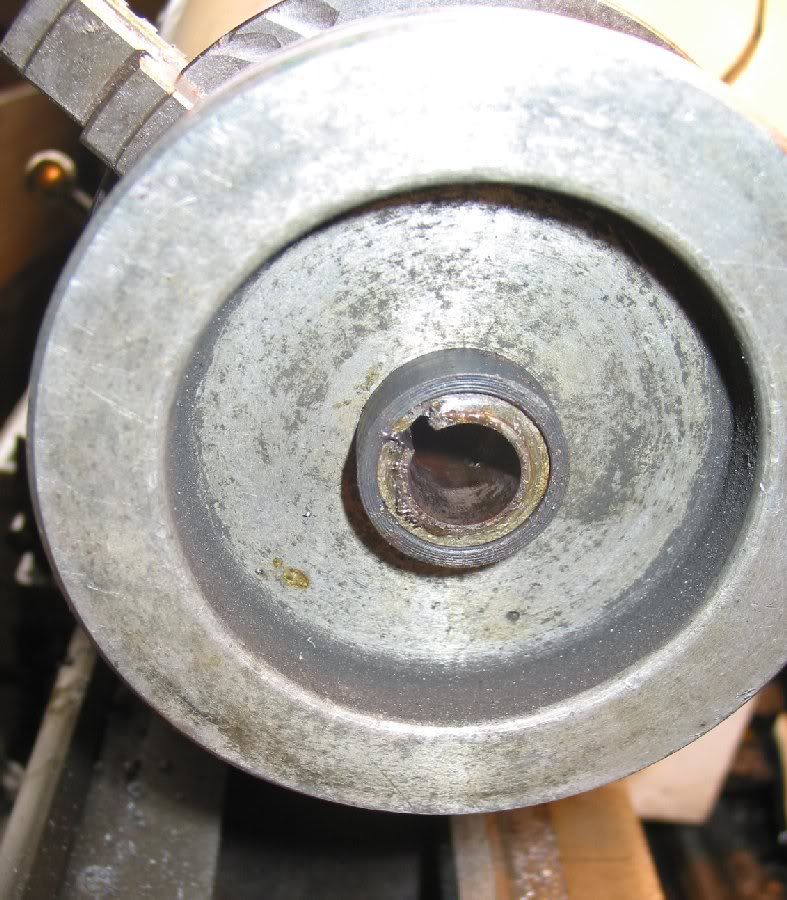
I turned up a home brew taper-lock-ish bush, but with a flange on the big end and bored it to match the motor.
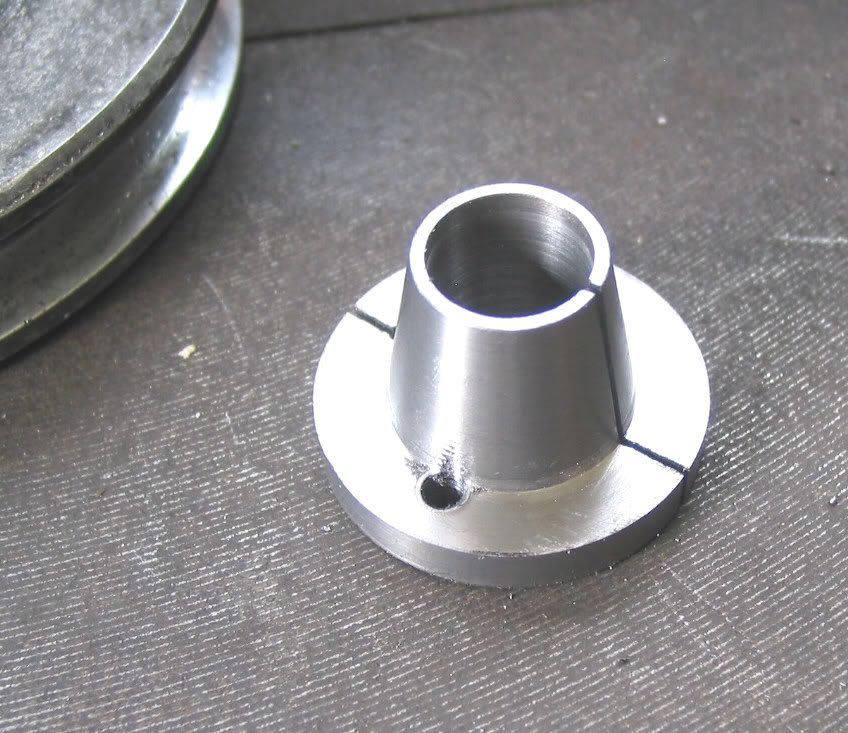
After roughing the outer taper with the compound set at an arbitrary 10deg, I was concerned to ensure that when I machined the bore of the pulley it would exactly match the bush. To bore the pulley, I would need the compound swivelled the other way to so I could bore it big end out to be able to check the fit, but the degree markings on the cross slide are only good to a degree and I wanted better than that or I could end up with an indeterminate swash-plate, not a true-running pulley. So to make a final cut on the taper bush, I switched the compound as I for the pulley bore and took a light cut off the back of the bush with the tool upside down. That way I know the two tapers will be identical. The pic is of another job, but shows the scheme.
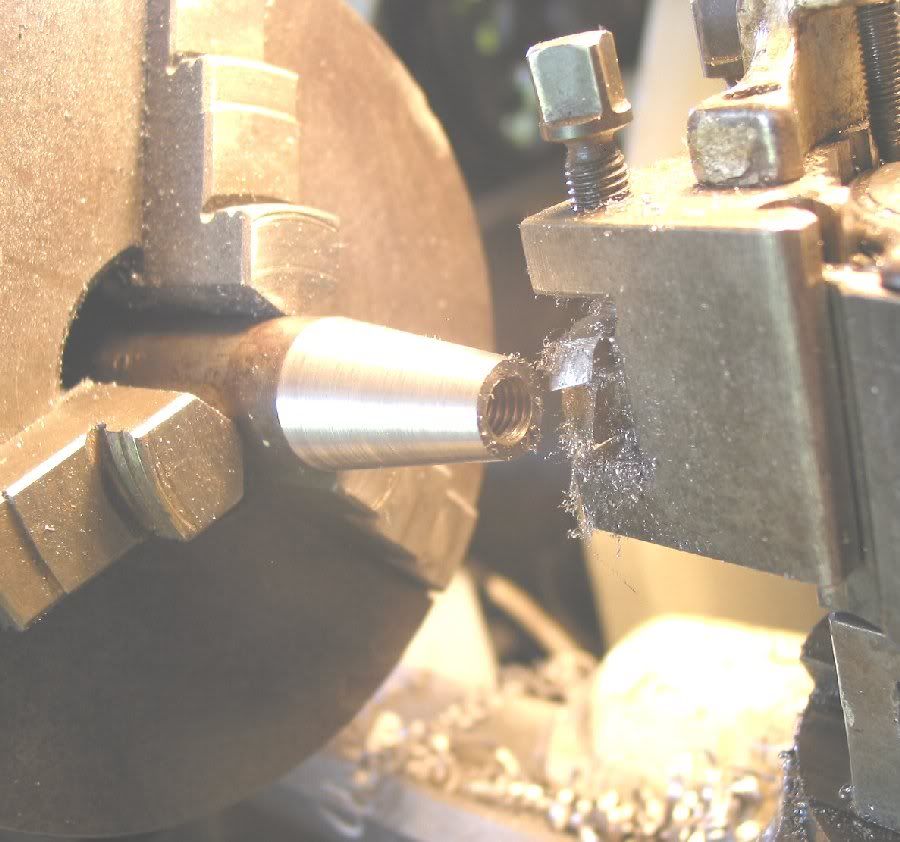
The other problem, has anyone rumbled it yet? I'm using the lathe to repair the lathe drive pulley - no pulley to drive the lathe! I hunted round for a spare pulley that could be pressed into service, but nothing that wouldn't require more effort than the repair. I was considering postponing the finishing until I go over to my parent's place (about once a week) and use another lathe there, but then happened to put the pulley down on the bench next to a gash 4" chuck..... oooer?!
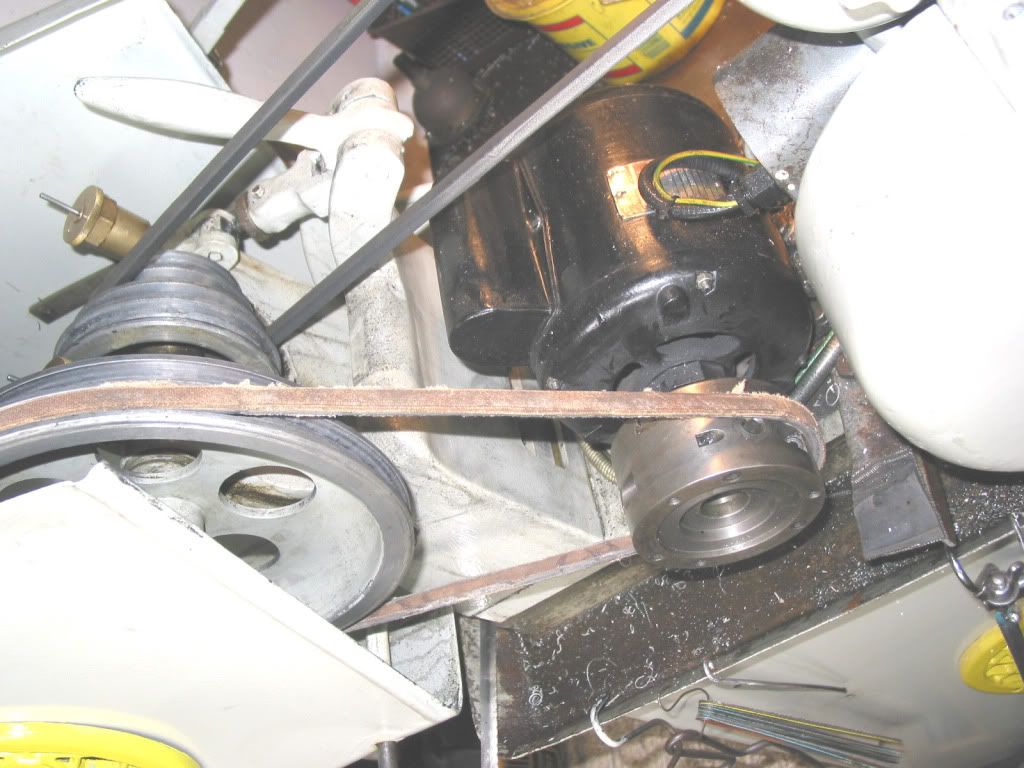
I wouldn't recommend it as a regular practice, but for a half-hour job to save a day and a 50 mile round trip, swapping to a shagged old belt from the compressor that was kept in the 'just in case' heap and is a bit longer than the right one and I didn't even have to adjust the motor, just dropped it on and got on with the job.