I have finally got round to making a start on my next ( Yep, I've caught it...
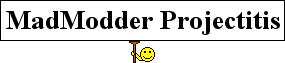
) project, and while tempted to do a Rocking engine, I had to stick with with my initial plan of building Bog's Paddleducks engine.
So I had previously got some materials gathered for this build, and not having any cast iron at all, but having a brass block that was itching to be reduced to a nice cylinder-shaped block, I decided to use brass for the cylinder.
Here is the raw brass block, the other dimensions are 25mm thick and 50mm high.

I then used my very expensive marking dye system and used my vernier caliper to mark out a rough shape to then transfer to my very expensive bandsaw (my right arm

)

So I next ground up a tiny toolsteel for my tiny flycutter as per the Bogstandard curved profile that I read about on a thread here somewhere. This is my second attempt at grinding the curved shaped flycutter, I have a larger flycutter that doesnt cut as well as this latest attempt, practice I guess

So with this newly ground up tool I am totally impressed with it. The finish on brass is soo silky smooth!!! Compare it to using a end-mill and there is just no contest. I also learnt that my X2's Z axis is made out of a very tough but flexible form of spagetti. I am intending on re-inforcing the upright column, but in the meantime I have to be mindful of taking lighter cuts.

I have an even smaller flycutter, they're so dinky.
By the way, is there an accepted method of working out what speed to set the mill at for flycutting?

( the smaller flycutter seemed happy to run faster)
So after squaring and sizing the 4 sides I then squared off the 2 ends with a 4-flute mill.

It's amazing how the little brass chippings/shavings get everywhere (especially down the neck of my teeshirt, and they are pretty hot too

) My workbench was (and still is) covered with a golden snowstorm.

I then had to smooth the 2 ends with some 360grit wet+dry placed on a granite plate to try and get them to match the smooth flycutter-ed surfaces.
And here it is, the first part made to size (well within 0.02mm on 2 dimensions and dead on the 3rd

)

That's all I got done today, not much to see so far, but it's good to be back on an engine project and I cant wait to get back into the workshop to crack on with it.
Tim
Edit: If you want to see larger versions of the pictures of this build click
here