Hey guys, I managed to sort it out. Basically it had come off the threaded lead screw at the front end, the lead screw has no threading at the end as a safety feature and so that is doesn`t carry the table into the gearing! Obviously at the other end it would just come off the thread. I had thought about this myself and had tried pushing it but with no luck earlier today. After reading Darrens thoughts about the Gibs I realised I should slacken them right off to give me more play and try and lock the table back onto the thread. I didn`t think it had worked as the travel is so slow (which I realise is right for a good finish on these machines) but it took me a while to notice it was moving.

Found it a home (grandparents) and didn`t sell it!

New 1ph motor installed

New pully installed

Table now traversing on the horizontal and vertical power feeds
To do:
1. Lock on the swivel table and mount the vice
2. Buy/make and install a tool holder (I have one but it is much much too big - maybe mod it?)
3. Check it all over again
4. Make some swarf....
Thanks for all the replies so far on this thread. It has been really helpful - I think sometimes it is just nice to write things down and it helps you mull through your ideas yourself as well as all the excellent replies you get back
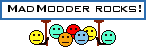
By the way I have obviously been reading the manual for this and I`m really chuffed to find that this shaper has both the additional add-ons that were available. It has the vertical power feed which is not standard and also the swivel table, rather than the fixed. Again, both of these were add-ons when originally purchased.

I didn`t have a clue about this when I first got it so quite nice supprises.
Vids and pics to come soon - with it not being at my house I need to make a concious effort to remember to take the camera!
Chris