So I dug out the spindle -- since I'm getting close to boring the headstock. I had sent for this one, standard Mini-lathe replacement, on sale from Little Machine Shop, and I must say I'm not enamored of it. Originally the idea was to save some time and machining by using a ready made, ground spindle, with morse taper , etc. But I really don't like that big hub on the end, behind the flange. It's not a bearing land, the bearing sits behind it. Therefore it adds 7/8" of overhang past the bearing.
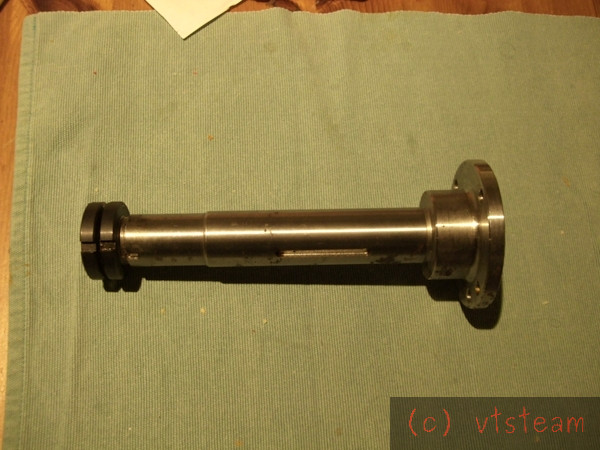
If you add in the flange and an adapter plate to fit my chuck, we're talking 1-1/2" of overhang, not including the chuck thickness, which I think is about 4". My whole aim with this lathe was to increase stiffness wherever possible, and reduce chatter.
Another disadvantage is the loss of turning length that nearly 6" of overhanging components yields on this relatively small lathe.
So I've been thinking of cutting part way into that hub and moving the bearing closer to the flange. The only fly in that ointment is the spindle wall thickness getting too thin around the mouth of the morse taper (about 23mm ID) -- which is why I think the step is there.
So I've been thinking about increasing the journal land and bearing ID there. The original bearings for the nose of the spindle are spec'ed as 30206 rollers of 30mm ID. That gives roughly 4mm wall thickness at the bearing where it is located further back.
If I go to 35 mm journal, step up to a 30207, roller and move it forward I'll have 6mm wall thickness at the bearing, and lose 17mm of overhang. So I think that's going to be the plan.
Also, thinking about the whole flange, plus adapter plate, plus chuck thickness overhang, I'm considering eliminating the adapter plate and building the existing flange out to match the chuck's needs for register and attachment. That would probably mean brazing a ring onto the existing flange, and then turning it to suit.
In fact I've even considered extending that idea of flange improvement into a 9" faceplate, and just making a means to attach the chuck to the faceplate. I like faceplate turning -- most of my career on the Gingery lathe was faceplate turning, and I have a myriad of simple chucks and attachments for doing all kinds of work on that. I've seen people grip one chuck with another -- why not similarly grip a chuck on a faceplate?
Faceplates give the shortest overhang possible for gripping large work.
Maybe an ideal for me would be a faceplate and ER collet system, and dispense with the 3 jaw altogether. Anyway, things to think about.........