It would have been Andrew, but I didn't know it wouldn't work at the time I bought them. The earlier cap wasn't cored out the same and had enough meat. Different manufacturer, I guess.
It was borne out today -- stopped at another hardware store further out of town while stocking up on kerosene and LP gas for the storm. Bought a couple more 3/8" pipe caps, and indeed they weren't relieved behind the threaded portion.
I also wanted to get rid of chatter, and had an idea on that score. When I got home, I switched the 3 jaw spindle for my milling spindle which has a 5/8" socket and 2 set screws. Then I turned the unthreaded end of a piece of 3/8" (nominal) pipe nipple to 5/8" to fit the socket. This gave a sort of 'collet chuck" and arbor to mount the pipe cap on, with much less overhang and weight than the 3 jaw had.
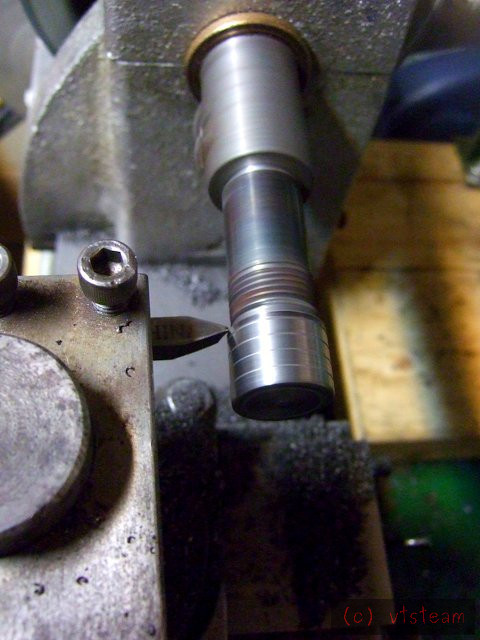
The turning went really well this time -- no chatter and these newer pipe caps were nice soft grey iron -- cut like butter. So that seems to have been the problem before -- bad pipe caps -- for engine building purposes at least! I might go back and by some more of those caps next time I'm in the area. They were only $1.79 each. Cheap for a piston.
The storm has held off so far this evening, so I was able to drill the new piston for a wrist pin. I used bit of brazing rod for that, and a few minutes ago was turning the crankshaft and watching the piston move up and down. Fun!
